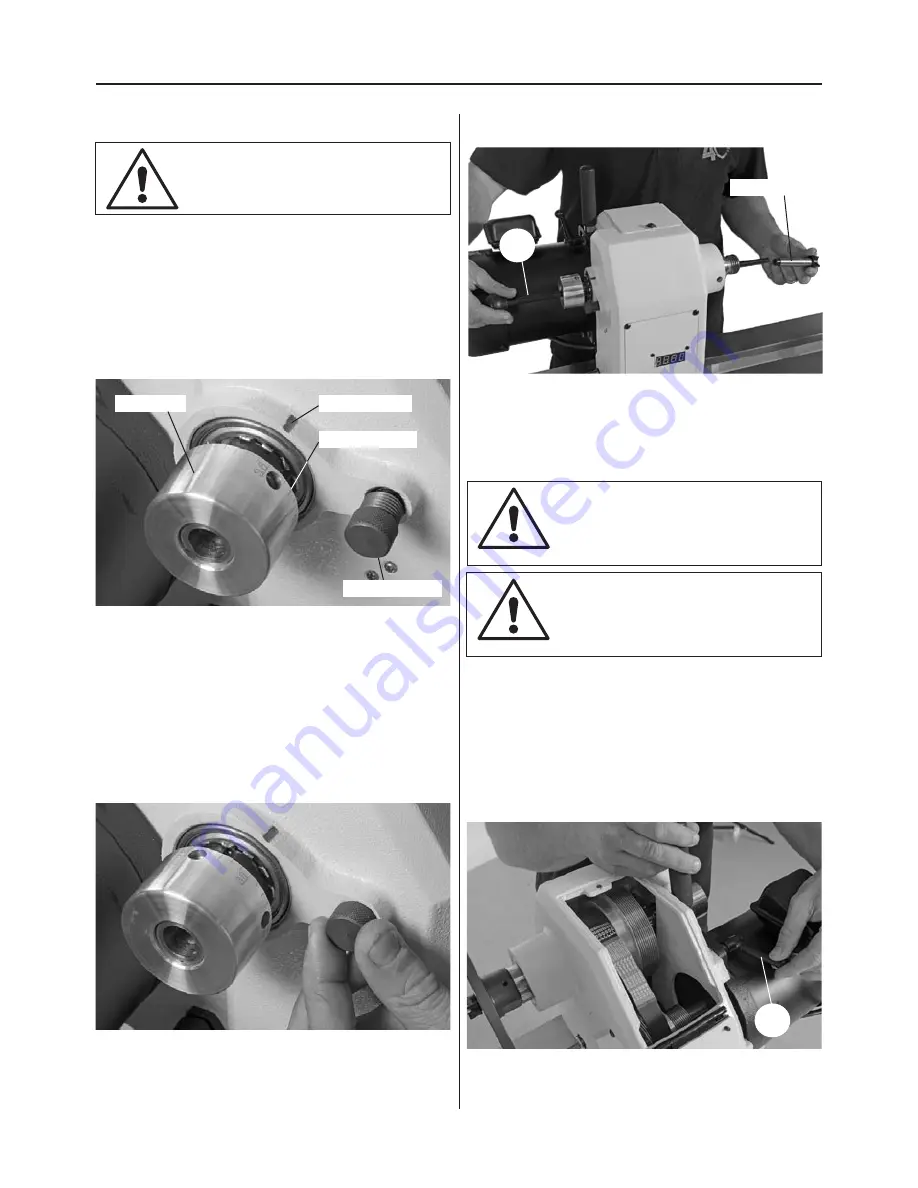
Operating Instructions
13
Indexing facility
Removing the Drive Centre
The Indexing ring is situated to the left side of the
headstock which incorporates 36 positions at (10˚)
segments. To the side of index ring is the index
locking pin to lock the spindle in position. The
indexing facility is useful for fluted columns, clock
faces and accurate hole positioning. (See figure 23)
Figure 23
Index ring
Index lock pin
10˚ Segments
Index marker
Figure 24
Line up the measurement you require on the index
ring with the index marker on the headstock and
screw in the index locking pin to lock the spindle in
position. (See figure 24)
NOTE: Make sure the measurement is in line with
the index marker otherwise the locking pin may
not in gauge properly.
To remove the drive centre from the spindle, locate
the push rod (C), insert it through the index ring
assembly and push the drive centre out, see figure 25.
Figure 25
Drive centre
C
Changing the belt speed
Note: The lowest speed pulley combination
is furthest from the faceplate, the smallest
motor pulley diameter to largest spindle
pulley diameter.
DISCONNECT THE LATHE FROM
THE MAINS SUPPLY BEFORE
CHANGING THE BELT
DISCONNECT THE LATHE FROM
THE MAINS SUPPLY
Open up the pulley access panel on top of the
headstock by removing the Hex screw. Slacken the
belt by loosening the motor locking handle (a),
move the motor until the belt is slack enough to be
reposition. (See figure 26)
Figure 26
Loosen the motor locking handle (a) enough
to allow the pulley to be repositioned
a
Continues Over...
Repeat the procedure for the live centre in the
tailstock.
Summary of Contents for AT1628VS
Page 15: ...Parts Breakdown List 15 Headstock Assembly A...
Page 16: ...Parts Breakdown List 16 Headstock Assembly A...
Page 17: ...Parts Breakdown List 17 Headstock Assembly A...
Page 18: ...Parts Breakdown List 18 Body Assembly B...
Page 19: ...Parts Breakdown List 19 Body Assembly B...
Page 20: ...Parts Breakdown List 20 Stand Assembly C Optional...
Page 21: ...Parts Breakdown List 21...
Page 22: ...Wiring Diagram 22...
Page 23: ...Notes 23...