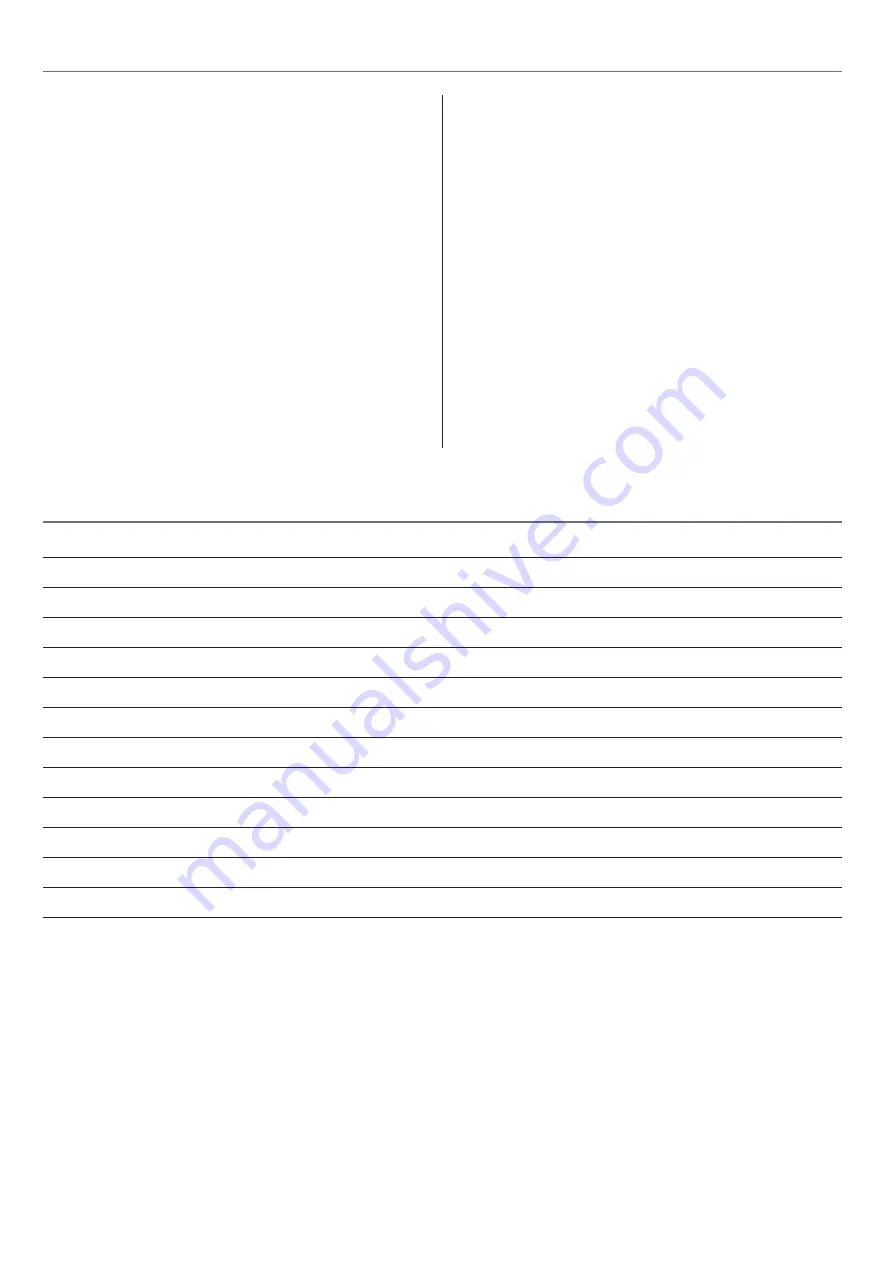
Specific Safety Instructions for Wood turning Lathes
6
1. Do not use ‘split’ work pieces.
2. Always start at the lowest speed when starting a new task.
3. Check that the tool rest is at or slightly below the centre line
of the work piece.
4. Check the work piece is securely mounted in the lathe before
switching on the power.
5. Rotate the work piece by hand, to check that it is centralised,
clear of the tool rest, not ‘split’ or has loose knots.
6. Where lathes have the facility to be reversed; check the
machine is rotating in the correct
direction.
7. If your lathe has the facility to run in reverse, you must ensure
that the mounting accessories (chucks, faceplates etc.,) can
be ‘locked’ onto the lathe mandrel, and in the case of chucks,
have some form of security device to prevent them ‘unwinding’
during reverse operation.
8. Make sure your tools are stored/racked away from the
turning area of the lathe. Do not reach over a rotating work
piece at any time.
9. Do not ‘dig in’ or try to take too large a cut.
10. Do not leave the lathe running unattended; or leave the
machine until everything is stopped.
11. Some turning tools may have specific sharpening angles
that have been determined by the manufacturers; when
re-sharpening, adhere to these angles to maximise the finish
of your work.
Specification
Code 107657
Model AP508WL
Rating Professional
Power
2.2kW 230V 1ph
Speed
60-1,200, 100-2,200, 140-3,700 rpm
Spindle Taper
MT2
Spindle Thread
M33 x 3.5 mm
Taper Tailstock
MT2
Distance Between Centres
762mm + 500mm with extension bed (depending on the centres fitted)
Max Diameter over Bed
508 mm
Tool Rest Stem Diameter
30 mm
Overall L x W x H
1,800 (plus 500 mm with Bed Extension) x 600 (plus 330 mm with Side Extension) x 1,230 mm
Weight
280 kg
Summary of Contents for 107657
Page 1: ...AP508WL Woodturning Lathe AT 208 02 2022 BOOK VERSION 7 Code 107657 Original Instructions ...
Page 4: ...What s Included 4 B C D E O F K H J G I N P L Q M ...
Page 22: ...Exploded Diagram Parts List 22 ...
Page 24: ...Exploded Diagram Parts List 24 ...
Page 26: ...Exploded Diagram Parts List 26 ...
Page 28: ...Wiring Diagram 28 ...
Page 29: ...Notes 29 ...
Page 30: ...Notes 30 ...
Page 31: ...Notes 31 ...