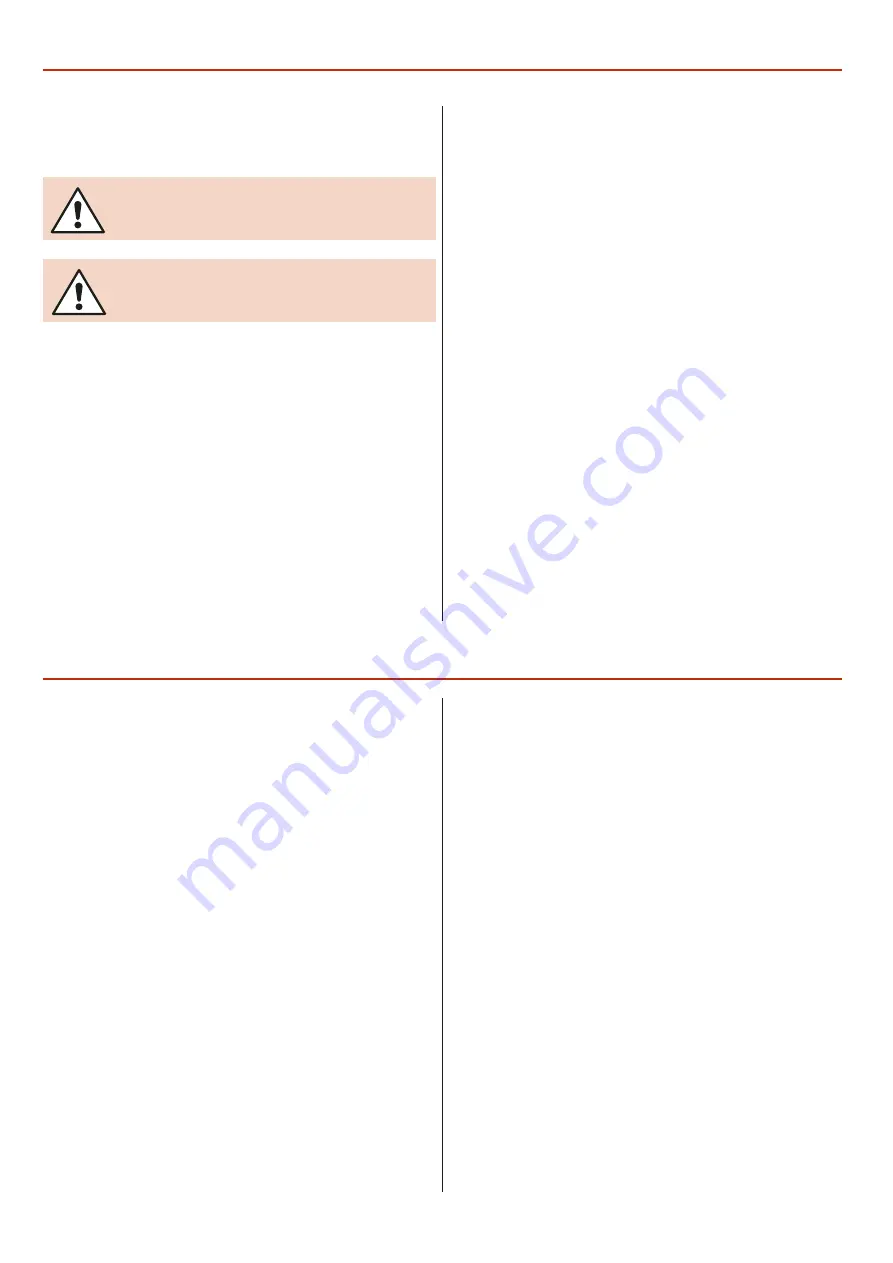
General Instructions for 230V Machines
4
The following will enable you to observe good working
practices, keep yourself and fellow workers safe and maintain
your tools and equipment in good working order.
WARNING!! KEEP TOOLS AND EQUIPMENT
OUT OF REACH OF YOUNG CHILDREN
Mains Powered Tools
• Tools are supplied with an attached 13 Amp plug.
• Inspect the cable and plug to ensure that neither are
damaged. Repair if necessary by a suitably qualified person.
• Do not use when or where it is liable to get wet.
Workplace
• Do not use 230V a.c. powered tools anywhere
within a site area that is flooded.
• Keep machine clean.
• Leave machine unplugged until work is about to commence.
• Always disconnect by pulling on the plug body and not the
cable.
• Carry out a final check e.g. check the cutting tool
is securely tightened in the machine and the correct
speed and function set.
• Ensure you are comfortable before you start work,
balanced, not reaching etc.
• Wear appropriate safety clothing, goggles, gloves,
masks etc. Wear ear defenders at all times.
• If you have long hair wear a hair net or helmet to prevent it
being caught up in the rotating parts of the machine.
• Consideration should be given to the removal of rings and
wristwatches.
• Consideration should also be given to non-slip footwear etc.
• If another person is to use the machine, ensure they are
suitably qualified to use it.
• Do not use the machine if you are tired or distracted.
• Do not use this machine within the designated safety areas
of flammable liquid stores or in areas where there may be
volatile gases.
• Check cutters are correct type and size, are undamaged
and are kept clean and sharp, this will maintain their
operating performance and lessen the loading on the
machine.
• OBSERVE…. make sure you know what is happening
around you and USE YOUR COMMON SENSE.
KEEP WORK AREA AS UNCLUTTERED AS IS PRACTICAL.
UNDER NO CIRCUMSTANCES SHOULD CHILDREN BE
ALLOWED IN WORK AREAS.
Specific Safety Instructions for Woodturning Lathes
1. Do not use ‘split’ work pieces.
2. Always start at the lowest speed when starting a new task.
3. Try to render a new work piece “round” (or as close as is
practical) before turning.
4. Check that the tool rest is at or slightly below the centre line
of the work piece.
5. Check the work piece is securely mounted in the lathe
before switching on the power.
6. Rotate the work piece by hand, to check that it is:
centralised, clear of the tool rest, not ‘split’ or has loose knots.
7. Where lathes have the facility to be reversed; check the
machine is rotating in the correct direction.
8. If your lathe has the facility to run in reverse, you must ensure
that the mounting accessories (chucks, faceplates etc.,) can
be ‘locked’ onto the lathe mandrel, and in the case of
chucks have some form of security device to prevent them
‘unwinding’ during reverse operation.
9. Make sure your tools are stored/racked away from the
turning area of the lathe. Do not reach over a rotating work
piece at any time.
10. Do not ‘dig in’ or try to take too large a cut.
11. Do not leave the lathe running unattended; or leave the
machine until everything is stopped.
12. If you are turning between centres with ‘softish stuff’,
check and reposition the tailstock centre frequently.