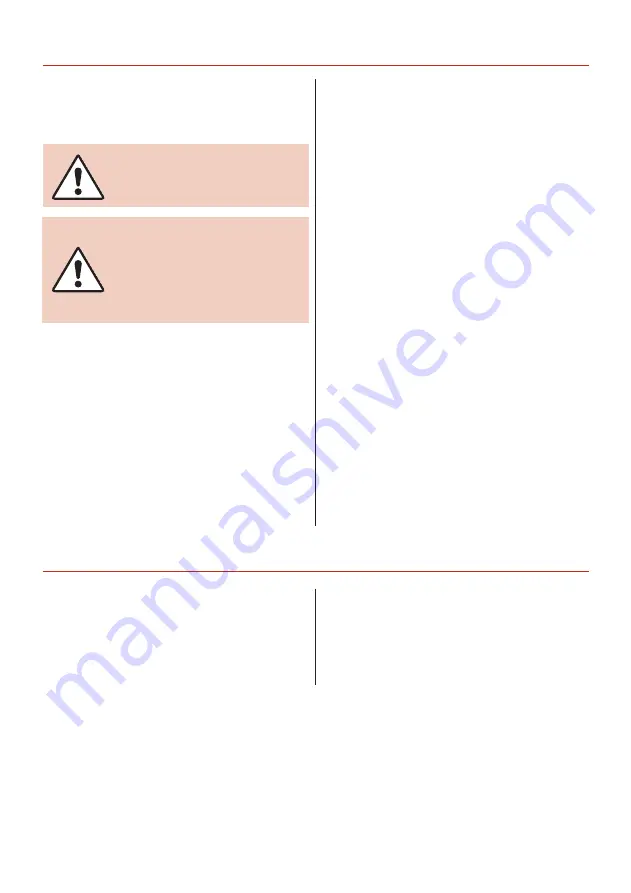
4
GENERAL INSTRUCTIONS FOR 230V MACHINES
SPECIFIC SAFETY INSTRUCTIONS FOR MORTICERS
The following will enable you to observe good working
practices, keep yourself and fellow workers safe and main-
tain your tools and equipment in good working order.
Mains Powered Tools
• Tools are supplied with an attached 13 Amp plug.
• Inspect the cable and plug to ensure that neither are
damaged. Repair if necessary by a suitably qualified
person.
• Do not use when or where it is liable to get wet.
Workplace
• Do not use 230V a.c. powered tools anywhere
within a site area that is flooded.
• Keep machine clean.
• Leave machine unplugged until work is about to
commence.
• Always disconnect by pulling on the plug body
and not the cable.
•
Carry out a final check e.g. check the cutting tool
is securely tightened in the machine and
the
correct speed and function set.
•
Ensure you are comfortable before you start work,
balanced, not reaching etc.
• Wear appropriate safety clothing, goggles, gloves,
masks etc. Wear ear defenders at all times.
• If you have long hair wear a hair net or helmet to prevent
it being caught up in the rotating parts of the machine.
• Consideration should be given to the removal of rings
and wristwatches.
• Consideration should also be given to non-slip
footwear etc.
• If another person is to use the machine, ensure they are
suitably qualified to use it.
• Do not use the machine if you are tired or distracted.
• Do not use this machine within the designated safety
areas of flammable liquid stores or in areas where there
may be volatile gases.
• Check cutters are correct type and size, are
undamaged and are kept clean and sharp, this will
maintain their operating performance and lessen the
loading on the machine.
• OBSERVE…. make sure you know what is
happening around you and USE YOUR COMMON SENSE.
WARNING!! KEEP TOOLS AND
EQUIPMENT OUT OF REACH OF
YOUNG CHILDREN
KEEP WORK AREA AS
UNCLUTTERED AS IS PRACTICAL.
UNDER NO CIRCUMSTANCES
SHOULD CHILDREN BE ALLOWED
IN WORK AREAS.
1. Ensure that the morticer is firmly fixed to its base as the
force exerted through the operating handle could be
enough to over-balance the machine.
2. Ensure that the operating handle is returned to the
upright position after cutting a mortise.
3. Mortice chisels have very sharp ends, handle them with
great care.
4. Make sure that the timber is held firmly down against
the table by using the table clamp. This prevents the
possibility of the timber being pulled upwards as the
mortice chisel is withdrawn from the hole.