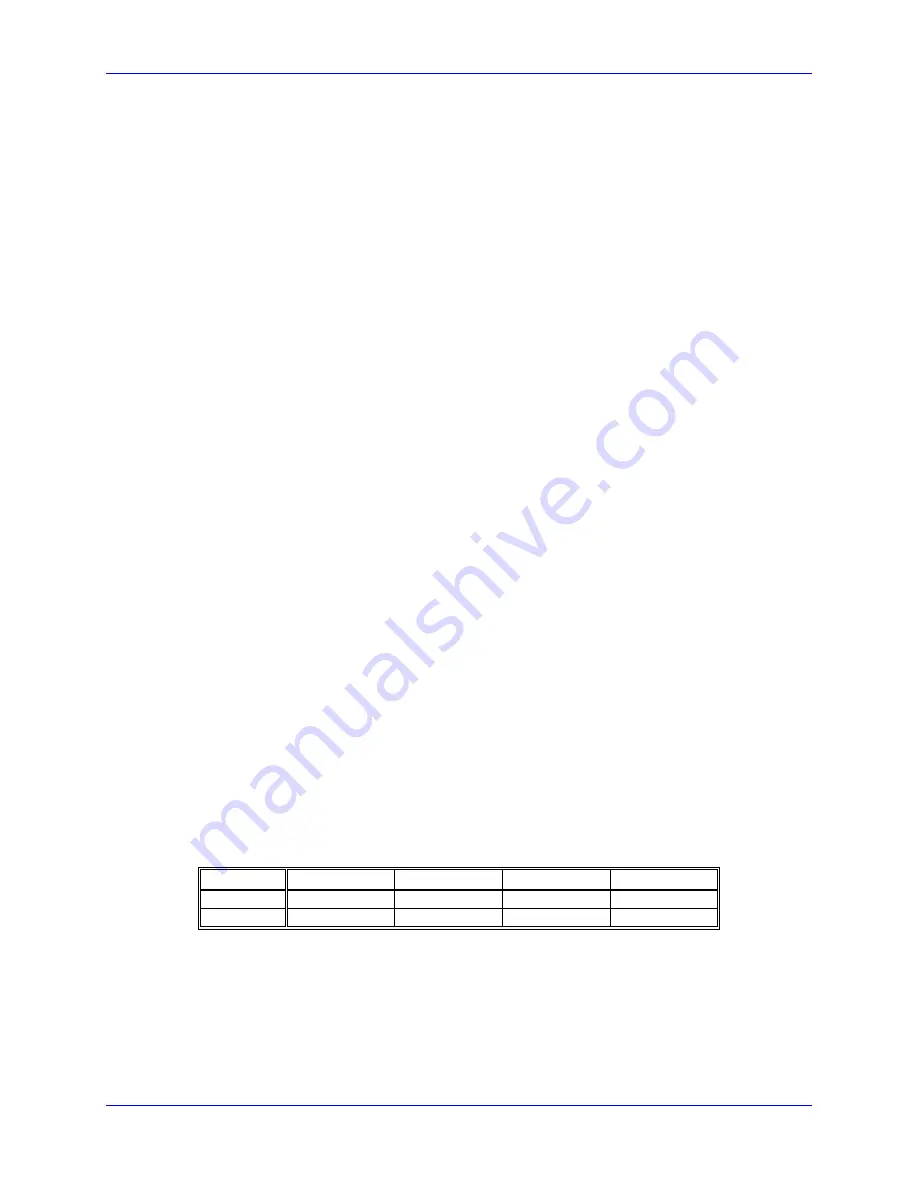
Accessory 24E2
power-on-position is the same. The information must be retrieved from MACRO Station variable
MSn,MI920 for each node transfer as specified by Ix10 at the Ultralite. MSn,MI920 does not need to be
set up because the MACRO Station will place the power-on position the appropriate register at power-up.
MLDT Software Setup of the UMAC MACRO
When the ACC-24E2 is used for MLDT feedback in a UMAC MACRO system, there are a few MI-
variables in the MACRO Station, and a few in the PMAC2 or Turbo PMAC2 driving the Station, that
must be set up properly.
Station Hardware Setup I-Variables for Servo IC
MS{anynode},MI903/MI907 (PFM Clock Frequency)
In almost all cases, the clock frequency driving the pulse-generation circuitry for all channels on the
Servo IC can be left at its default value of 9.83 MHz (0.102
µ
sec). Few will need to change
MI903/MI907, which also controls other clock signals, from its default value of 2258.
MS{anynode},MI904/MI908 (PFM Pulse Width)
The pulse width, set by MI904/MI908 in units of PFM clock cycles must be set long enough for the
MLDT to see, and long enough to contain the rising edge of the RPM start echo pulse, or the rising edge
of the single DPM echo pulse. For example, if this edge can come up to 2
µ
sec after the start of the
excitation pulse and the PMAC clock cycle is at its default of about 0.1
µ
sec, then I7m04 must be set at
least to 20.
MS{node},MI916 (Output Format Select)
For the channel associated with this node to be used for MLDT feedback, MI916 must be set to 1 or 3 for
the C sub-channel to be used for PFM-format output. On an ACC-24E2A, I7mn6 must then be set to 3
for the A and B sub-channels to be used for DAC-format output.
MS{node},MI910 (MLDT Feedback Select)
For the channel associated with this node to be used for MLDT feedback, MI910 must be set to 12. In
this mode, the pulse timer is cleared on the output pulse, and latched on the echo pulse, counting in
between at 117.96 MHz.
Station Conversion Table Processing I-Variables
The pulse timer for Servo IC m Channel n holds a number proportional to the time and therefore the
position. This must be processed in the conversion table before it can be used by the servo loop. It is best
to use the filtered parallel data conversion, a 3-line entry in the table (three consecutive MI-variables).
The MI-variables for the conversion table start at MI120.
Line 1 (Method and Address):
This 24-bit value (6 hex digits) should begin with a 3 (filtered parallel
data) followed by the address of the timer register. The possible values for this line are shown in the
following table:
Encoder Conversion Table Parallel Filtered Data Format 1
st
Line for ACC-24E2A Boards
ACC-24 #
Channel 1
Channel 2
Channel 3
Channel 4
1 $30C040 $30C048 $30C050 $30C058
2 $30C060 $30C068 $30C070 $30C078
Line 2 (Bits Used Mask):
This 24-bit value should be set to $07FFFF to specify the use of the low 19
bits of the 24-bit source word.
Line 3 (Max Change):
This 24-bit value should be set to a value slightly greater than the maximum true
velocity ever expected, expressed in timer LSBs per servo cycle. With a typical MLDT, the 117.96 MHz
timer LSB represents 0.024 mm (0.00094 inches); the default servo cycle is 0.442 msec.
MLDT Feedback for UMAC-Turbo and UMAC-MACRO
29