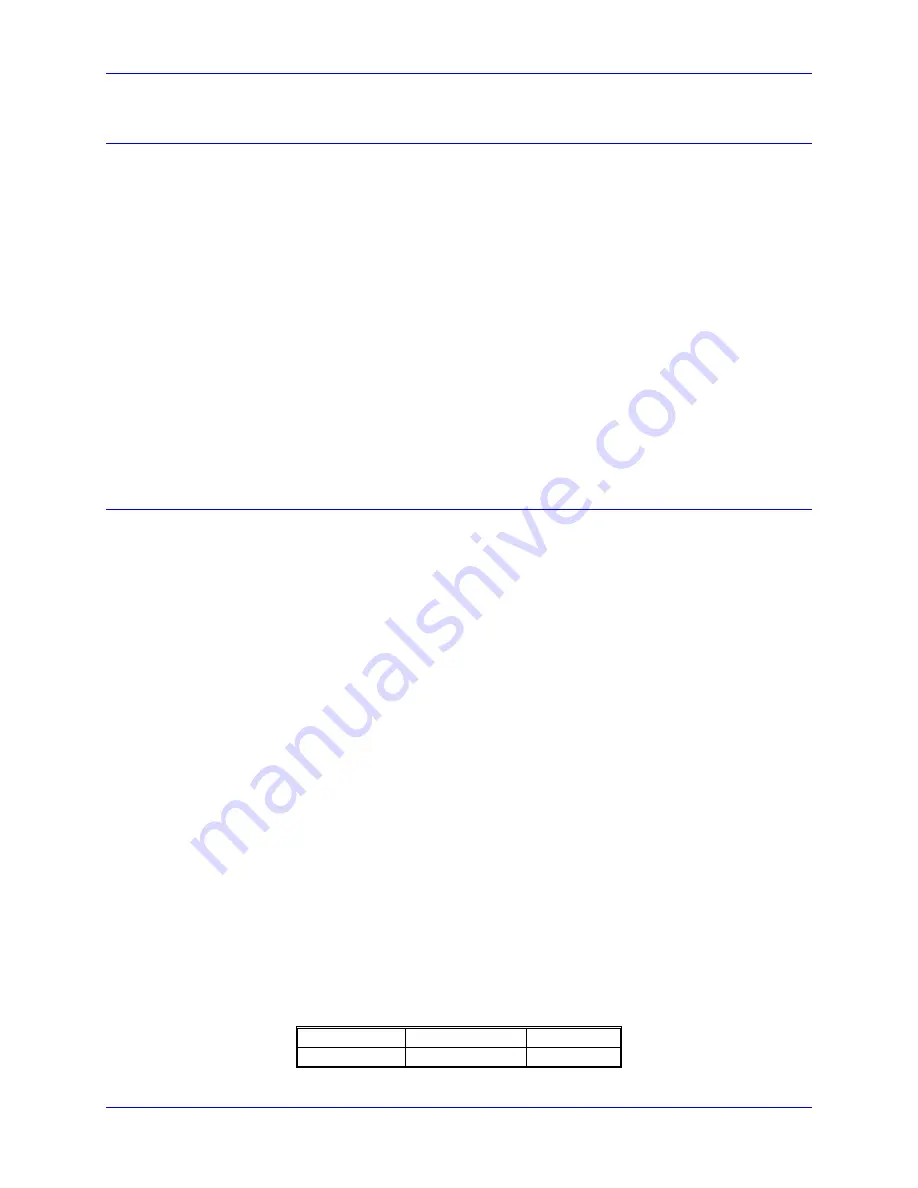
Accessory 24E2
ACC-24E2 Clock Settings
The Phase Clock and Servo Clock must be configured on each ACC-24E2x base board. Each system can
have only one source for the servo and phase clocks and jumpers must be set appropriately to avoid a
timing conflict or a watchdog condition.
Starting in UMAC-Turbo firmware version 1.937, the firmware will set the clock settings automatically
for the ACC-24E2 cards in the UBUS. To enable this feature, set jumper E13 from 2 to 3 for all of the
ACC-24E2s plugged into the UMAC. At re-initialization (either $$$*** command or power up with E3
jumpered on UMAC), the firmware will know that all of the cards are in the auto configuration setup and
will assign the card with the lowest base address setting (usually $78200) the task of sourcing the clocks
by setting variable I19 to the appropriate register. The clocks will be set initially to the factory default
servo update cycle and phase clock cycle. For a better understanding of this feature, refer to description
of I19 in the Turbo Software Reference Manual.
For UMAC Turbo systems with firmware older than version 1.937, set one of the ACC-24E2s to transmit
(E13 set 2-3) the phase and servo clock (usually the card at the lowest base address setting) and the rest of
the ACC-24E2s to receive (E13 set 1-2) the phase and servo clocks.
For MACRO systems, the clock select jumper should be set to receive servo and phase clocks. For the
ACC-24E2, E13 should be set 1-2.
Resistor Pack Configuration
Differential or Single-Ended Encoder Selection
The differential input signal pairs to the PMAC have user-configurable pull-up/pull-down resistor
networks to permit the acceptance of either single-ended or differential signals in one setting, or the
detection of lost differential signals in another setting.
•
•
The ‘+’ inputs of each differential pair each have a hard-wired 1 k
Ω
pull-up resistor to +5V. This
cannot be changed.
The ‘-’ inputs of each differential pair each have a hard-wired 2.2 k
Ω
resistor to +5V; also each has
another 2.2 k
Ω
resistor as part of a socketed resistor pack that can be configured as a pull-up resistor
to +5V, or a pull-down resistor to GND.
If this socketed resistor is configured as a pull-down resistor (the default configuration), the combination
of pull-up and pull-down resistors on this line acts as a voltage divider, holding the line at +2.5V in the
absence of an external signal. This configuration is required for single-ended inputs using the ‘+’ lines
alone; it is desirable for unconnected inputs to prevent the pick-up of spurious noise; it is permissible for
differential line-driver inputs.
If this socketed resistor is configured as a pull-up resistor (by reversing the SIP pack in the socket), the
two parallel 2.2 k
Ω
resistors act as a single 1.1 k
Ω
pull-up resistor, holding the line at +5V in the absence
of an external signal. This configuration is required if encoder-loss detection is desired; it is required if
complementary open-collector drivers are used; it is permissible for differential line-driver inputs even
without encoder loss detection.
If Pin 1 of the resistor pack (marked by a dot on the pack) matches Pin 1 of the socket (marked by a wide
white square solder pin on the front side of the board), then the pack is configured as a bank of pull-down
resistors. If the pack is reversed in the socket, it is configured as a bank of pull-up resistors.
The following table lists the pull-up/pull-down resistor pack for each input device:
Device
Resistor Pack
Pack Size
Encoder 1
RP22
6-pin
6
Hardware Setup