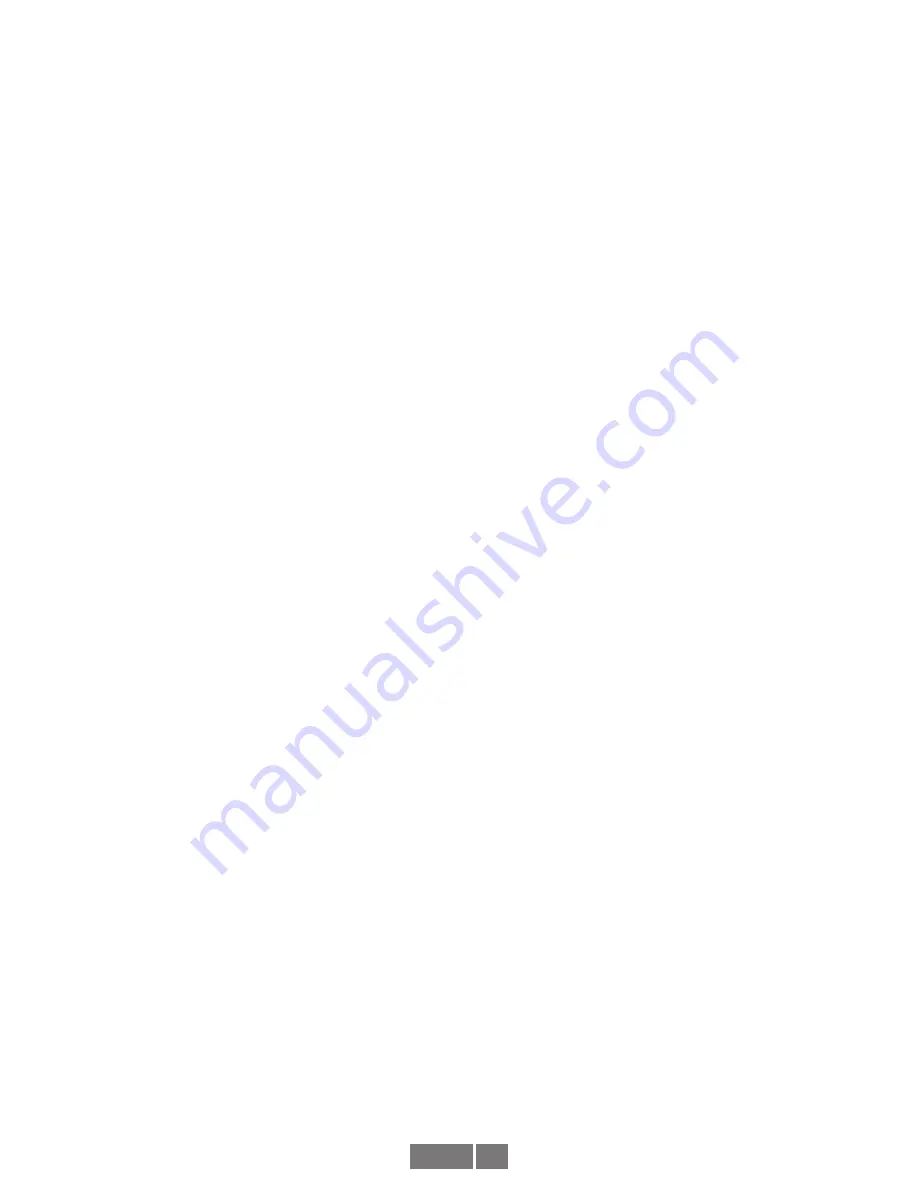
XR125 3
CAUTION
DO NOT use silicone sealants or caulk of any kind on
the motor or encoder face; these can cause
misalignment or sensor scraping damage. Do apply
antiseize compound (copper) to the encoder face to
assist in easy removal. The XR125 electronics are fully
sealed; water may enter and leave the rotor area as
needed. Remove the bottom pipe plug in the housing if
frequent moisture buildup is expected.
A special marine-sealed version of the housing is available (option
006) if there is a concern about ice or salt buildup inside the
encoder.
(OPTIONAL) OUTBOARD SEAL PLATE KIT INSTALLATION
For applications requiring shafts to pass completely through the
XR125, Avtron offers an outboard through-shaft seal plate kit with
V-ring seal. See Table 3 for part numbers and Figure 3. Note that
for large through-shaft bores T8 and T9, no seal is available. For T9
through-shafts, no cover is needed.
1. Install the encoder rotor as shown above.
2. Remove the existing cover of the encoder. Retain the screws
and washers.
3. Mount the XR125 stator housing as shown above.
4. Install new through-shaft cover using the (4) #10-24 screws
and
washers from step 2.
5. Apply silicone lubricant or medium grade machine oil (20
weight)
to the outboard side of the cover where the V-ring seal will
contact it.
6. Slide the V-ring seal onto the shaft, and ensure that it is
compressed against the cover. See installation Figure 3.
MOUNTING THE XR125/XR12 WITHOUT A STATOR HOUSING
The XR125 (XR12 rotor) may be mounted without the use of
a C-face or XR125 stator housing. See XR12 manual for details.
WIRING INSTRUCTIONS
CAUTION
Be sure to remove power before wiring the encoder.
Be sure to ground the cable shield: Avtron recommends
grounding the shield at the isolator module for Zone 1
applications or in the drive cabinet for Zone 2
applications. Cable should not be grounded multiple
places. An intrinsic safety ground is required at the
XRB1 Isolator Module.
CAUTION
SMARTSafe encoders include a local ground lug for
customer convenience and encoder frame grounding
if required to meet local electric code requirements or
site operator protection standards. This is NOT the
required XRB1 intrinsic safety ground connection
required for hazard protection against ignition of
explosive atmospheres for Zone 1 and Zone 21
applications!
CAUTION
The XRB1 isolator used for Zone 1 and Zone 21
protection requires an intrinsic safety ground to provide
hazard protection. Failure to connect this ground, or
providing an inadequate safety ground path can result
in an spark/ignition hazard which can result in property
damage, injury, or even death.
For bi-directional operation of the encoder, proper phasing of the two
output channels is important. Phase A channel typically leads phase
B channel for clockwise shaft rotation as viewed from the anti-drive
or accessory end of the motor (encoder mounting end).
See Pinout and Phasing tables for exceptions.
Wiring option “G” provides a pinout compatible with Northstar
TM
encoders, with a cable shield connection on pin 10. Note that this
option does not ground the shield.
CORRECTIVE ACTION FOR PHASE REVERSAL
1) Remove Power.
2) Exchange wires on cable, either at encoder cable
end or at speed controller end (but not both).
a) Single Ended 2 Phase Wiring
(see wiring diagram)
Exchange A and B connections at the device end.
b) Differential 2 Phase Wiring (see wiring diagram) Exchange
either A with A– in the phase A pair OR B with B– in the
phase B pair but NOT both.
3) Apply Power.
4) Verify encoder feedback is correct, using hand rotation of shaft,
or jog mode of the speed controller.
Interconnection cables specified in the wire selection chart are
based on typical applications. Cable must be selected and installed
in accordance with IEC/EN60079-14 and IEC/EN60079-25. Physical
properties of cable such as abrasion, temperature, tensile sstrength,
solvents, etc., are dictated by the specific application. General
electrical requirements are : stranded copper, 20 through 16AWG
(Industrial EPIC connector type options can use 14 AWG). Each twisted
wire pairs overall shielded with braid or foil with drain wire, .05uf of
maximum total uutual or direct capacitance, outer sheath insulator.
See specifications for maximum cable length. Stranded 20 AWG wire
should not be used for cable runs greater then 61 meters. If 20AWG is
used with EPIC type connector options the wire ends should be tinned.
See wiring diagram for examples of alarm output wiring.
MAINTENANCE
GENERAL
This section describes routine maintenance for the Avtron XR125
Encoder. For support, contact Avtron’s field service department at
216-642-1230. For emergency after hours service contact us at
216-641-8317.
The XR125 SMARTach II circuitry includes a diagnostic package that
includes Adaptive Electronics and a Fault-Check output.
FAULT-CHECK
After power-up and the rotor position is checked by the sensor, the
Fault-Check LED will turn green.
If the adaptive electronics reach their adjustment limit for any
reason, the Fault-Check alarm and LED will notify the drive and
operator of an impending failure. The LED will turn red if the
Adaptive Electronics reach their adjustment limit. This output occurs
before an actual failure, allowing steps to be taken to replace
the unit before it causes unscheduled downtime. Fault-Check
annunciation is available as an “alarm” output through the connector
(Zone 2 configuration only) and as an integral LED.
TROUBLESHOOTING:
If the drive indicates a loss of encoder/tach fault and the XR125
fault-check LED is not illuminated, check the encoder power supply.
If power is present, check polarity; one indicator of reversed power
supply is that all outputs will be high at the same time. If the drive
indicates encoder fault, but the LED shows GREEN, then check the
wiring between the drive and the encoder. If the wiring appears
correct and in good shape, test the wiring by replacing the XR5
sensor module. If the new module shows GREEN, and the drive still
shows encoder loss/tach fault, then the wiring is faulty and should
be repaired or replaced.