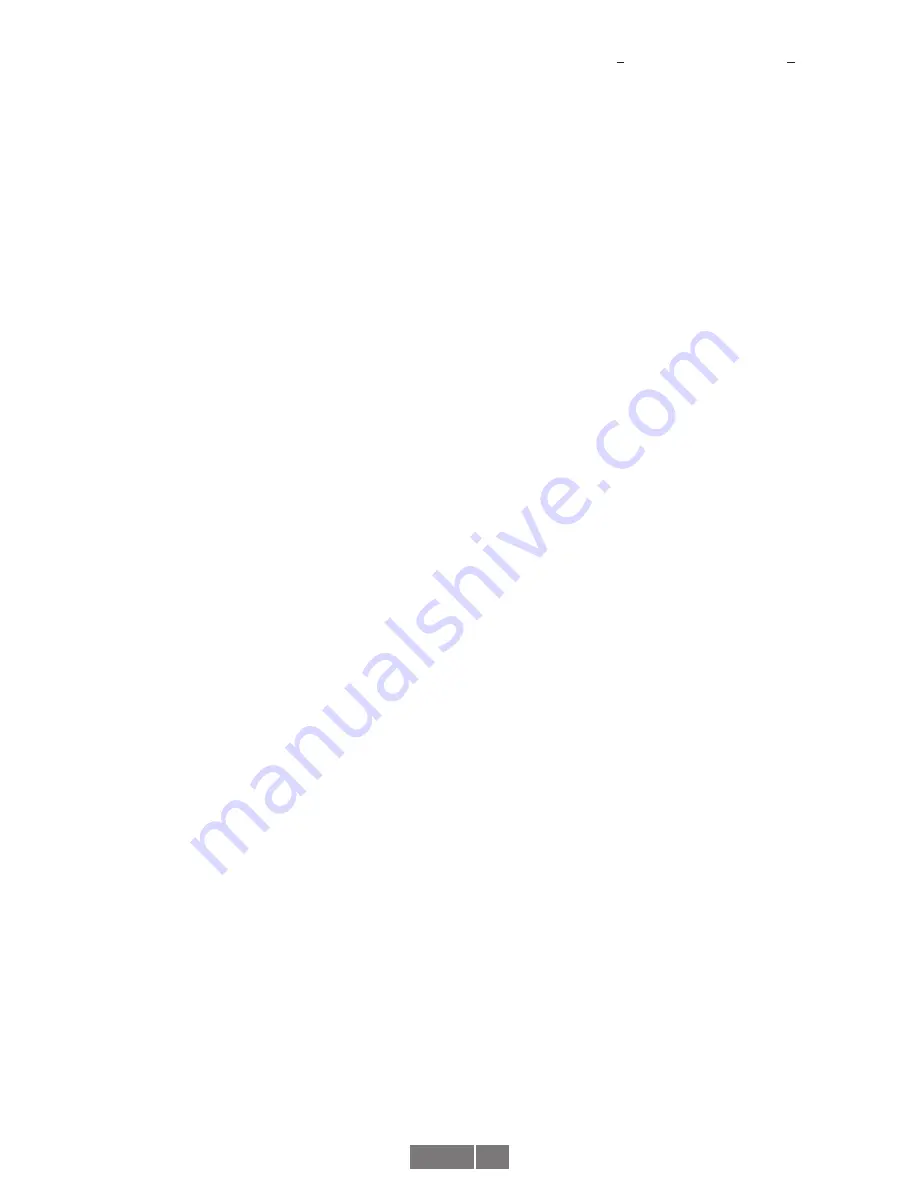
AV850 4
NOTE
If additional magnetic shielding (option 004) has
been added to the sensors, be sure to remove the
sensors before installing the stator housing.
The stator housing is retained to the motor using four, 1/2-13 x 3” bolts
and spring type lock washers (supplied). If the stator is to be sandwich
mounted between an accessory such as a brake and the motor, select
the bolt length accordingly. Apply anti-seize compound to the perimeter
of the AV850 where it will contact the motor C-face.
Carefully move the stator housing into position, avoiding contact with
the rotor. DO NOT FORCE the housing into place. Install the four
mounting bolts (torque 30 to 35 foot pounds) [47.5-40.6 n-m].
CAUTION
DO NOT use silicone sealants or caulk of any kind on the
motor or encoder face; these can cause misalignment or
sensor scraping damage. Do apply anti-seize compound
(copper) to the encoder face to assist in easy removal. The
AV850 electronics are fully sealed; water may enter and
leave the rotor area as needed. Remove the bottom pipe
plug in the housing if frequent moisture buildup is expected.
(OPTIONAL) OUTBOARD SEAL PLATE KIT
INSTALLATION.
For applications requiring shafts to pass completely through the AV850,
Avtron offers an outboard through-shaft seal plate kit with V-ring seal.
See Table 4 for part numbers and Figure 4.
1. Install the encoder rotor as shown above.
2. Remove the existing cover of the encoder. Retain the screws
and washers.
3. Mount the AV850 stator housing as shown in Figure 4.
4. Install new through-shaft cover using the (4) #10-24 screws
and washers from step 2.
5. Apply silicone lubricant or medium grade machine oil (20
weight) to the outboard side of the cover where the V-ring seal
will contact it.
6. Slide the V-ring seal onto the shaft, and ensure that it is
compressed against the cover. See installation Figure 4.
(OPTIONAL) SHAFT GROUNDING KIT INSTALLATION
(Rotors “FA-F9”, “GA-G9”)
Refer to separate Shaft Grounding Kit Instructions (M190-AV850)
(OPTIONAL) CHECK ROTOR POSITION
1. Remove a sensor or blank side cover plate.
2. Verify the rotor magnetic stripe is aligned with the grooves (see
Figure 5).
3. Replace the sensor or side cover plate.
WIRING INSTRUCTIONS
CAUTION
Remove power before wiring.
Wiring diagrams are shown in Figure 6 and 7.
For bidirectional operation of the encoder, proper phasing of the two
output channels is important. Phase A channel leads phase B channel
for clockwise shaft rotation as viewed from the anti-drive or accessory
end of the motor (encoder mounting end). Wiring option “G” provides
a pinout compatible with Northstar™ encoders, with a cable shield
connection on pin 10. Note that this option does not ground the shield;
Avtron still recommends grounding the shield at the drive end of the
cable for all wiring options.
CORRECTIVE ACTION FOR PHASE REVERSAL
1) Remove Power.
2) Exchange wires on cable, either at encoder cable end or at
speed controller end (but not both).
a. Single Ended 2 Phase Wiring (see wiring diagram)
Exchange A and B at the use end of the wires.
b. Differential 2 Phase Wiring (see wiring diagram) Exchange
either
A
with
A in the phase A pair OR B with B in the
phase B pair but NOT both.
3) Apply power.
4) Verify encoder feedback is correct, using hand rotation of shaft,
or jog mode of the speed controller.
Interconnecting cables specified in the WIRE SELECTION CHART in
Figure 6 are based on typical applications. Refer to the system drawing
for specific cable requirements where applicable.
Physical properties of cable such as abrasion, temperature, tensile
strength, solvents, etc., are dictated by the specific application.
General electrical requirements are: stranded copper, 22 thru 16 gauge
(Industrial EPIC Connector options can use 14-20 AWG), each wire pair
individually shielded with braid or foil with drain wire, 0.05 uF maximum
total mutual or direct capacitance, outer sheath insulator, 1,000 ft.
max. See WIRE SELECTION CHART in Figure 6 for some suggested
cables.
See Figure 7 for examples of alarm output wiring.
NOTE
When using the industrial connector (“1”, “G”, “P”, “Q”,
“V”, “X”, or “Z” options), the minimum wire size is 20 gage,
and 20 gage (only) wire ends must be tinned with solder
before connection at the screw terminals.
MAINTENANCE
GENERAL
This section describes routine maintenance for the Avtron AV850
Encoder. For support, contact field service for Avtron Encoders at
216-642-1230. For emergency after hours service contact us at
216-641-8317. The AV850 SMARTach III circuitry includes a diagnostic
package that includes Adaptive Electronics and a Fault-Check output.
ADAPTIVE ELECTRONICS
A perfect duty cycle consists of a waveform whose “high” and “low”
conditions are of the same duration (50%/50%). The AV850 adaptive
electronics extends the life of the AV850 by constantly monitoring and
correcting duty cycle over time.
FAULT-CHECK
After power-up and the rotor position is checked by the sensor, the
Fault-Check LED will turn GREEN.
If the adaptive electronics reach their adjustment limit for any reason,
the Fault-Check alarm and LED will notify the drive and operator of an
impending failure. The LED will turn RED if the Adaptive Electronics
reach their adjustment limit. This output occurs before an actual
failure, allowing steps to be taken to replace the unit before it causes
unscheduled downtime. Fault-Check annunciation is available as an
“alarm” output through the connector and as an integral LED.
TROUBLESHOOTING:
If the drive indicates a loss of encoder/tach fault and the AV850 fault-
check LED is not illuminated, check the encoder power supply. If power
is present, check polarity; one indicator of reversed power supply is that
all outputs will be high at the same time. If the drive indicates encoder
fault, but the LED shows GREEN, then check the wiring between the
drive and the encoder. If the wiring appears correct and in good shape,
test the wiring by replacing the AV5 sensor module. If the new module
shows GREEN, and the drive still shows encoder loss/tach fault, then
the wiring is faulty and should be repaired or replaced.
If the alarm output and/or LED indicate a fault (RED):
1. Remove a sensor plate or one of the sensors, and use
the built-in gauge to check the location of the rotor (see Figure
2.1). Ensure the label marked “This side out” is facing away
from the motor.