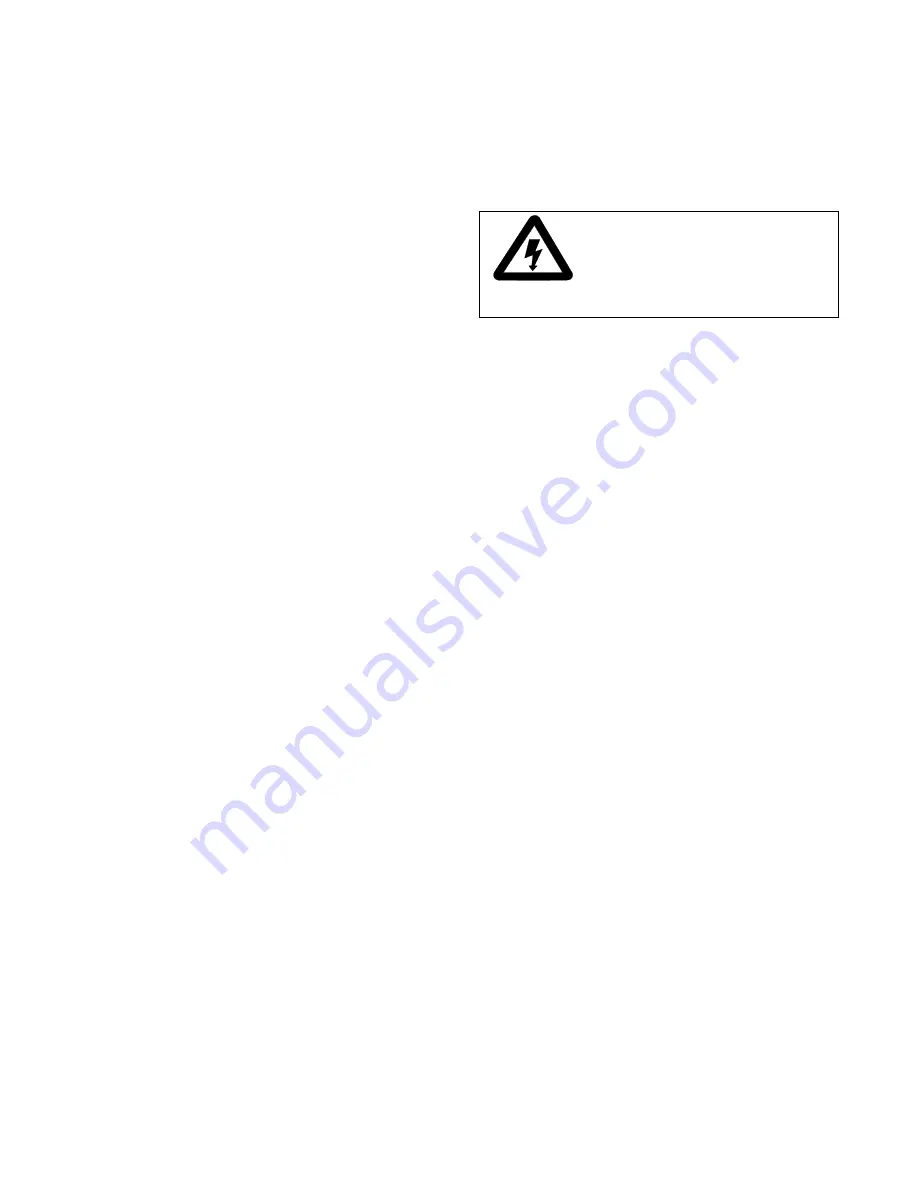
15
If the droop accessory has been supplied with the generator
it will have been tested to ensure correct polarity and set to a
nominal level of droop. The final level of droop will be set
during generating set commissioning.
6.2.1 SETTING PROCEDURE
Depending upon available load the following settings should
be used - all are based on rated current level.
0.8pf LOAD
(at full load current)
SET DROOP TO 3%
Zero pf LOAD (at full load current)
SET DROOP TO 5%
Setting the droop with low power factor load is the most
accurate.
Run each generator as a single unit at rated frequency or
rated fre 4% depending upon type of governor and
nominal voltage. Apply available load to rated current of the
generator. Adjust 'DROOP' control to give droop in line with
above table. Clockwise rotation increases amount of droop.
Note 1
Reverse polarity of the CT will raise the generator voltage
with load. The polarities S1-S2 shown on the wiring
diagrams are correct for clockwise rotation of the generator
looking at the drive end. Reversed rotation requires S1-S2 to
be reversed.
Note 2
The most important aspect is to set all generators equal. The
precise level of droop is less critical.
Note 3
A generator fitted with droop circuit, operated as a single unit
at rated load 0.8pf, is unable to maintain the usual +/-
½
%
regulation.
A shorting switch can be connected across S1-S2 to restore
regulation for single running.
Important !
LOSS OF FUEL to an engine can cause
its generator to motor with consequent
damage to the generator windings.
Reverse power relays should be fitted to
trip main circuit breaker.
LOSS OF EXCITATION to the generator
can result in large current oscillations
with consequent damage to generator
windings. Excitation loss detection
equipment should be fitted to trip main
circuit breaker.
6.3 OVERVOLTAGE DE-EXCITATION BREAKER
This provides positive interruption of the excitation power in
the event of overvoltage due to loss of sensing or internal
AVR faults including the output power device.
Important !
When the circuit breaker is supplied
loose the AVR is fitted with a link on
terminals K1-K2 to enable operation of
AVR. When connecting the circuit
breaker this link must be removed.
6.3.1 RESETTING THE BREAKER
In the event of operation of the circuit breaker, indicated by
loss of generator output voltage, manual resetting is
required. When in the "tripped" state the circuit breaker
switch lever shows "OFF". To reset move the switch lever to
the position showing "ON".
Danger
!
Terminals which are 'LIVE' with the
generating set running are exposed
when the AVR access cover is
removed. Resetting of the circuit
breaker must be carried out with he
generating set stationary, and engine
starting circuits disabled.
When fitted in the generator, access to the breaker is gained
by removal of the AVR access cover.
The circuit breaker is mounted on the AVR mounting bracket
either to the left or to the right of the AVR depending upon
AVR position. After resetting the circuit breaker replace the
AVR access cover before restarting the generating set.
Should resetting of the circuit breaker not restore the
generator to normal operation, refer to section 7, following
Fault Finding Procedure.
6.4 FAULT LEVEL CURRENT LIMIT - TRANSFORMERS
These accessories work in conjunction with the AVR circuits
to provide an adjustment to the level of current delivered into
a fault. One current transformer (CT) per phase is fitted to
provide current limiting on any line to line or line to neutral
fault.
Note: The W phase CT can also provide "DROOP". Refer to
6.2.1. for setting droop independent of current limit.
Adjustment means is provided with the "I/LIMIT" control
potentiometer on the AVR. Refer to Fig. 1 in section 4.5 for
location. If current limit transformers are supplied with the
generator the limit will be set in accordance with the level
specified at the time of order, and no further adjustment will
be necessary. However, should the level need to be
adjusted, refer to the setting procedure given in 6.4.1.
6.4.1 SETTING PROCEDURE
Run the generating set on no-load and check that engine
governor is set to control nominal speed.
Stop the generating set. Remove the wires to terminals -
K1,K2, and insulate the 'BARE ENDS' to make safe. Connect
a 5 amp 240V AC switch across the terminals K1-K2.
Turn the "I/LIMIT" control potentiometer fully anticlockwise.
Short circuit the stator winding with a bolted 3 phase short at
the main terminals. An AC current clip-on ammeter is
required to measure the winding lead current.