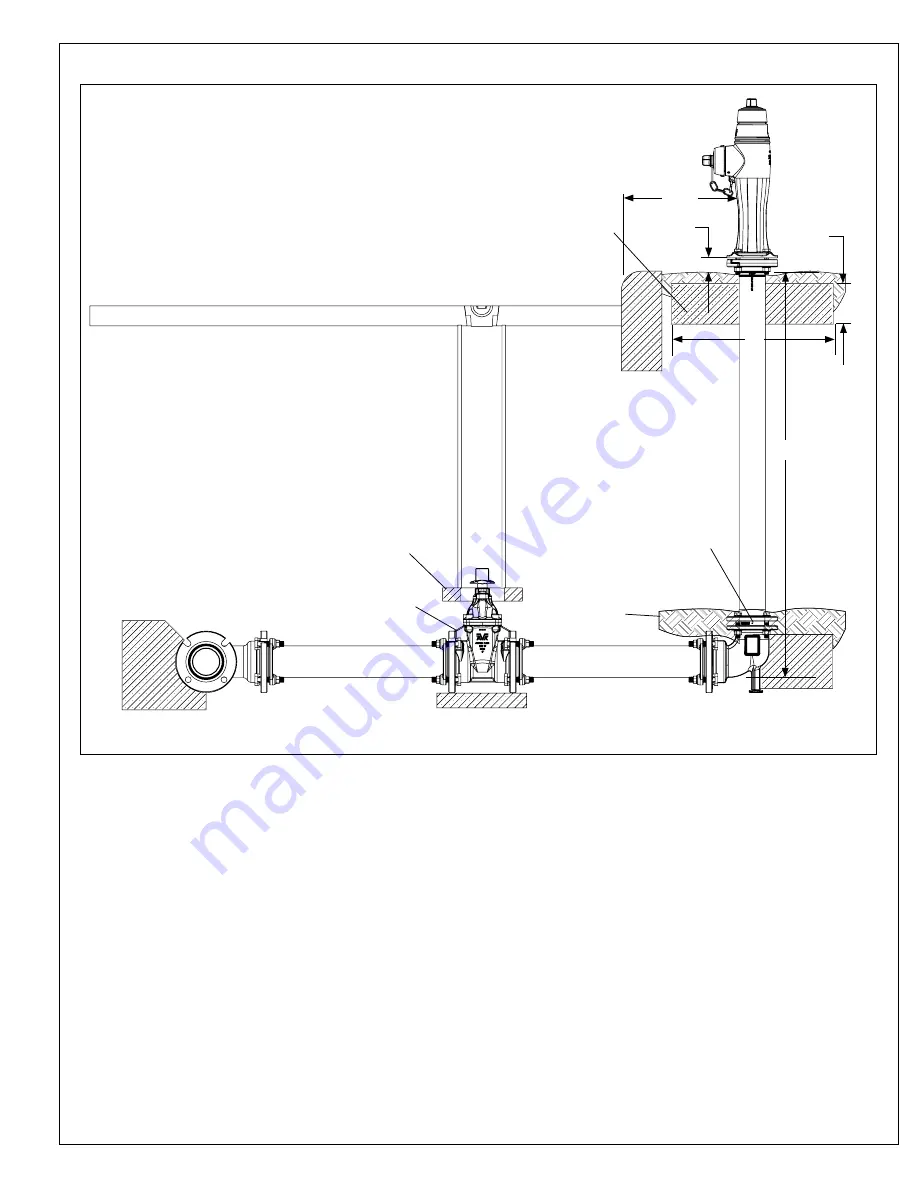
page 4
Fig. 1
Hydrant Installation
C o n c r e t e
thrust block
Concrete
Curb
Concrete collar for protection on all
hydrant installations.
Drain Detail:
Caution: When pouring
thrust block, do not cover
drain holes.
1/3 cubic yard drain field
rock.
C o n c r e t e
thrust block
Supply Valve
6"
2' min.
2" min.
2'
Bury
Concrete