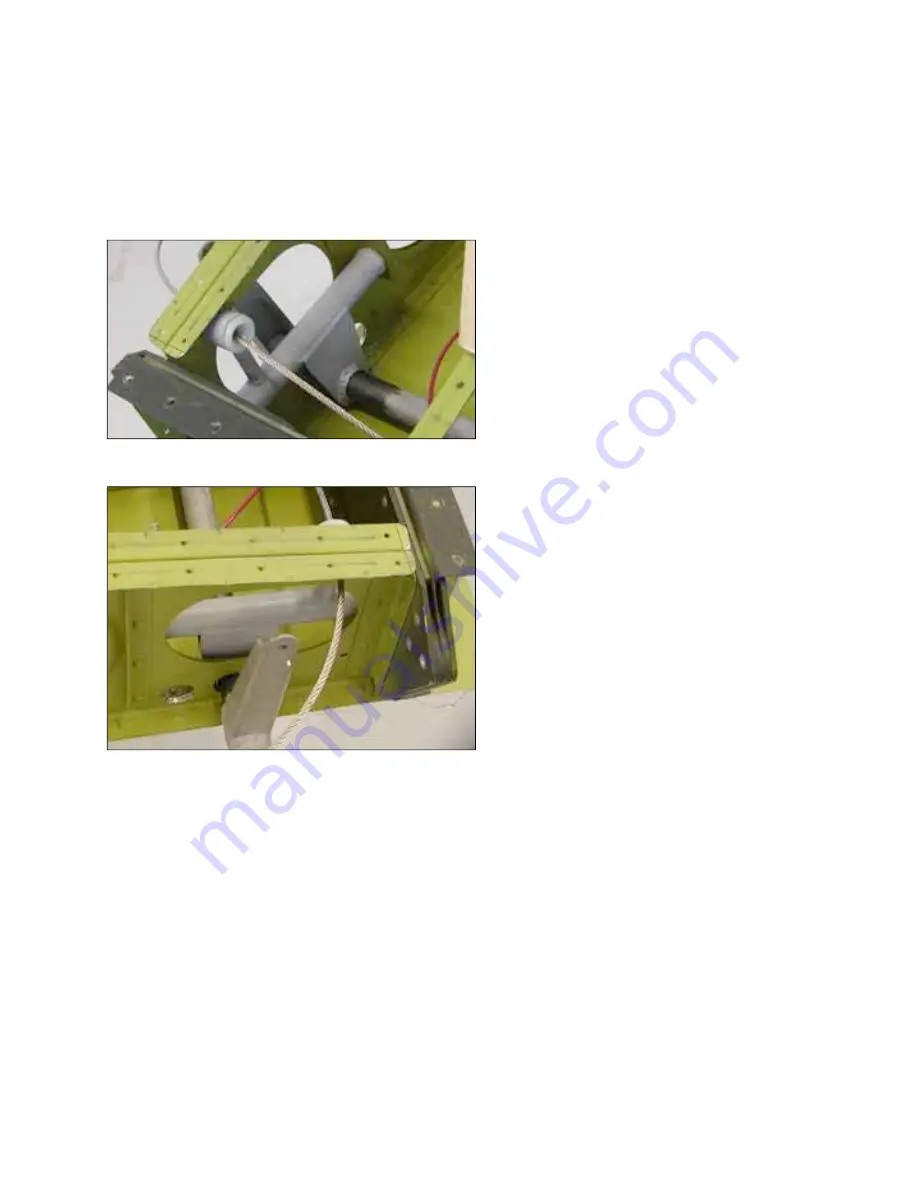
8
flap push rod between them to hold them in align-
ment. Then clamp the top end of the push rod
where it bolts to the arms down to the crossmember
tube to keep it from moving while drilling it.
The root actuating arms have to be mount-
ed at a specific angle on the torque tube to give the
flap cables the most efficient angle for pulling.
With the outboard actuating arms still
clamped against the fore and aft tubing crossmem-
ber, position the inboard arm as per Drawing No.
14.
Because there is limited room between the
fuselage and the wing root, it is essential that the
flap actuating arm be centered in that gap. For that
reason, it’s advisable to drill the hole through the
actuating arm and torque tube AFTER the wings
are on the airplane to ensure no interference occurs.
IT S RECOMMENDED THAT THE OUTBOARD
ACTUATING ARMS BE DRILLED WITH THE
WINGS ON THE AIRPLANE.
Come in from the bottom (or turn the wing
over) and center punch where you’ll drill the hole
in the arms. Then drill one arm with a fresh 1/8” bit
(make it fresh, so it cuts cleanly and easily). Using
that as a guide, drill with the 11/64” and ream. Then
put a bolt in place to keep it lined up.
Do 1/2 of the outboard arms at a time, so
one of them is finished and bolted in place, which
will hold the other one in position and eliminate
minor mis-alignments and wallowed-out holes.
These will be bolted with Nyloc nuts.
If you want, you can install the flap springs
now, which will help hold everything under tension
and keep everything from moving.
A Note About Drilling
The back side of every hole you drill is
bound to have at least a certain amount of burr
standing up. The burr will be less if you use a sharp
bit and don’t push too hard, but you’ll still get a
burr. Your life will be much easier later on, if you
file off every burr you can reach, including those
inside the actuating arms. Not only does this pro-
duce a nicer looking unit with fewer stress risers
but it makes putting the torque tube in and out
much easier. This is where a Dremel tool with a lit-
tle sanding drum on it would come in handy for
those inside burrs.
The Flap Actuating Cable
Later, after you put the wings back on the
airplane semi-permanently and position the actuat-
ing arms and drill the mount bolt, you’re ready to
attach the actuating cable. The flap arm was deliv-
ered with a 3/16” hole (AN3) hole, however you
use a 1/4” shackle rather than a 3/16” shackle to
give a longer distance at the arm, which increases
cable clearance from some structure.
A 3/16” (AN3) bolt will be sloppy in the
shackle so bush it down with short pieces of 1/4 x
.028” tubing. If you can’t find that size tubing, con-
tact AviPro. The only charge is for shipping. Later
kits have six inches of the tubing supplied.
The actuating arm at the inside end of the torque tube uses a
1/4” shackle for connecting with the flap cable and it is bushed
down to 3/16” with 1/4” x .028 tubing.
Sand the paint off the inside of the pivot bushing and the tube
and it
’
ll be easier to insert it and it will work much easier.
Summary of Contents for Bearhawk N33RB
Page 1: ......