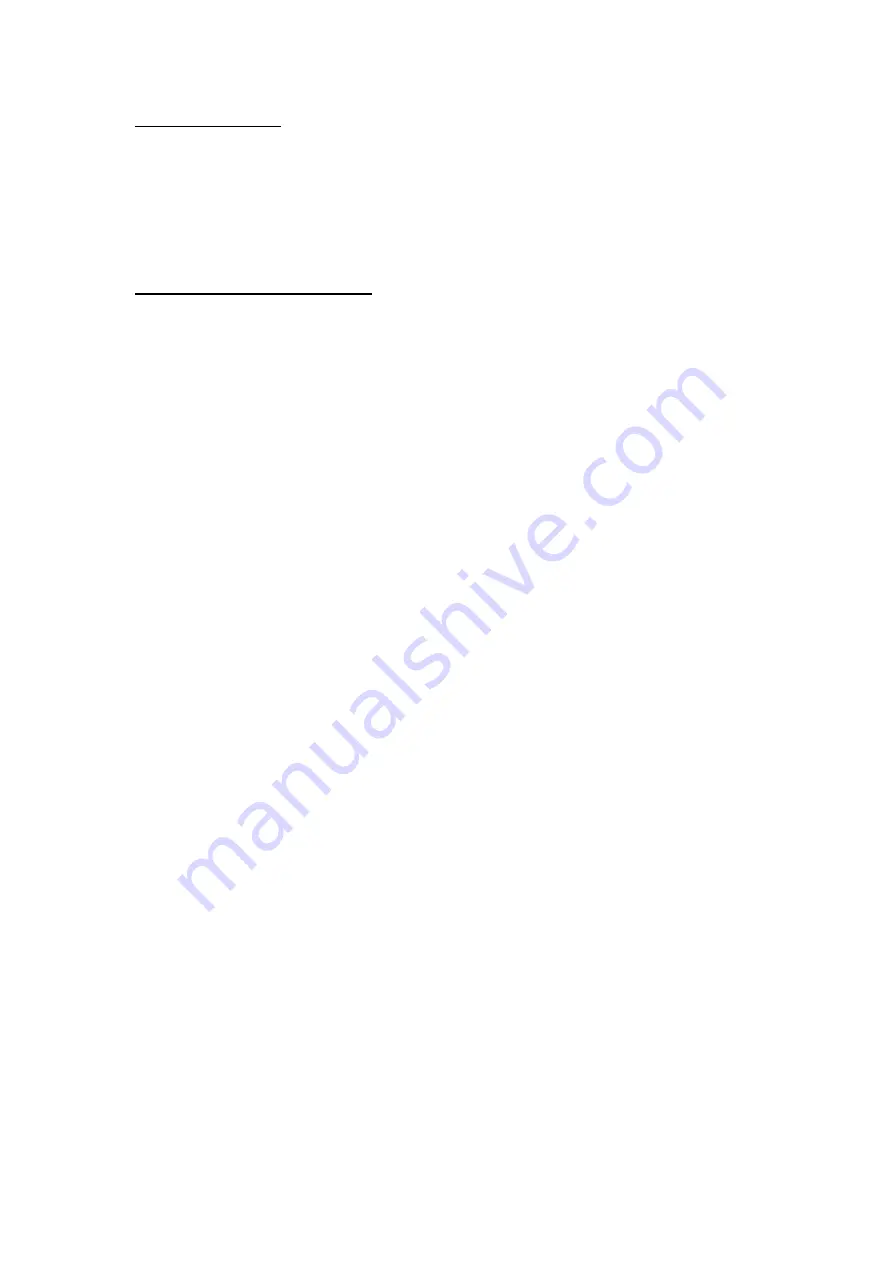
Java
140
Owner`s Manual
Anti-luff line wires
The anti-luff lines on a hang glider are important for the glider's pitch stability. They
should be replaced if they are damaged. The 'luff line 'heights' should be checked
every 100 hours or after the glider has had a heavy landing. It in not advisable to
leave the glider rigged tail into wind in a wind of more than 10 mph. This places
needless loads on the sail and 'luff lines and increases the rate at which they wear out.
Checking the ''luff line heights
'
This should be carried out with the glider fully rigged and with no wind. This is
easiest in a large building. It can done outside but only be in nil wind conditions.
The keel should be supported horizontally at the junction of the rear wires. The keel
must be completely straight. If the glider is supported by the end of the keel this will
bend the keel and give false readings for the 'luff line heights.
The VB. should be in the fully released position.
A length of thin line is required. (Nylon thread, kite string or fishing line.) This line
should be threaded between the 'luff line eyelets and pulled taught. A light strong
thread is an advantage as it will not sag too much.
The line should pass in a straight line between the two eyelets. If you are measuring
number 1 'luff line (the line closest to the keel) the thread will have to pass from the
left hand number one 'luff line eyelet, in front of the top rear rigging wire, to the right
hand number one ' luff line eyelet. If you are measuring number 4 'luff line (as in the
diagram below) the thread will pass behind the top rear rigging wire.
Checking 'luff line 4 height (h4)
The ''luff line height' is the perpendicular distance from the top of the keel to the
measuring thread or thin line.
Measure each 'luff line independently and write down the results.
Compare with the table below:
'Luff line number
1
2
3
4
Normal 'luff line heights (mm)
90
140
155
170
MINIMUM
'luff line height (mm) 80
125
140
155
If your 'luff line are less than the minimum height (Your 'luff lines are too long)
DO
NOT FLY
. Send the 'luff line set to Avian Ltd. with a note of the heights.
(Remember a bent keel will give you incorrect figures. Replace the keel and measure
the heights again.)
24