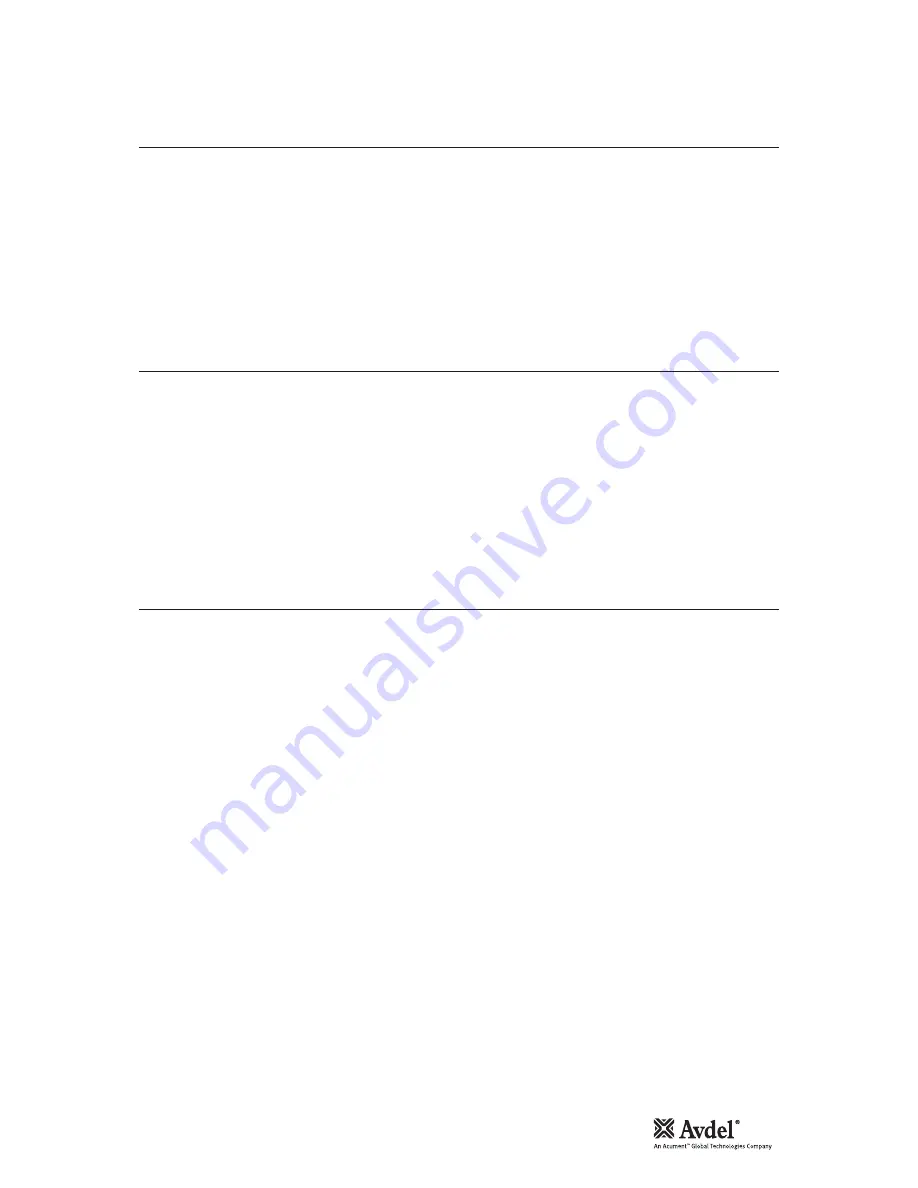
17
Minor Maintenance
Major Maintenance
Assembly
Electrical Maintenance
•
To replace the fuse unscrew the Fuse Holder Cap
30
by hand and remove the fuse.
•
To replace the 'Plug-in' Components, ie. Timer
26
and Relay
24
, loosen the four corner screws found on top of the Electric
Enclosure
31
with a flat screwdriver and remove the cover. The Timer
26
and Relay
24
can now be re moved by simply
'unplugging'. For identification of these items, see the wiring diagrams on pages 18-20 and the general assemblies and parts lists
on pages 10-16.
•
To reset the Thermal Overload
20
on the Contactor
21
, remove the cover as above and depress the blue button located on the
contactor assembly.
•
Remove the Enclosure Lid
31
as above.
•
Pull the two wires leading to the solenoid off the Bridge Rectifier
27
and feed them through the Gland
18
in the Enclosure
32
.
•
Loosen the motor connections at the Contactor
21
and the motor earth wire from the Isolator
22
and free the wires.
•
Separate the Enclosure
32
from the Mounting Plate
17
by loosening and removing the four screws found in the four corners at
the bottom of the Enclosure using a flat screwdriver and a 7 mm spanner
•
All the major components ie. Contactor
21
, Transformer
13
and the Bridge Rectifier
27
can now be removed and replaced using
a flat screwdriver and a 7 mm spanner.
•
If it becomes necessary to effect major maintenance on the motor, the Enclosure Adaptor Plate can be removed by loosening and
removing the four screws securing it to the motor. Ensure that its relative position to the motor is noted.
•
If the Mounting Plate
17
has been removed from the motor, replace and secure with the four screws using a flat screwdriver and
a 7 mm spanner.
•
Feed the motor wires through the base of the Enclosure
32
and re-mount it on the Mounting Plate
17
and secure with the four
screws using a flat screwdriver and a 7 mm spanner.
•
Re-connect the motor wires as given in the wiring diagrams on pages 18-20 using a 4 mm flat screwdriver.
Note: 3 phase motors are not direction sensitive.
•
Replace and tighten all panel wires using a flat screwdriver.
•
Feed the solenoid wire through the Gland
29
and connect to the Bridge Rectifier
27
and tighten the gland using a 20 mm
spanner.
•
Replace the Enclosure Lid
31
and secure using a flat screwdriver.
Note: Replacement of the valve solenoid has been detailed in the Mechanical Maintenance Section on page 7.
•
Connect to the power supply, switch 'On' and test for the function of the Directional Valve Solenoid and the Sleep Mode
With these basic Functions in Operation, the HydraPac is ready for use.