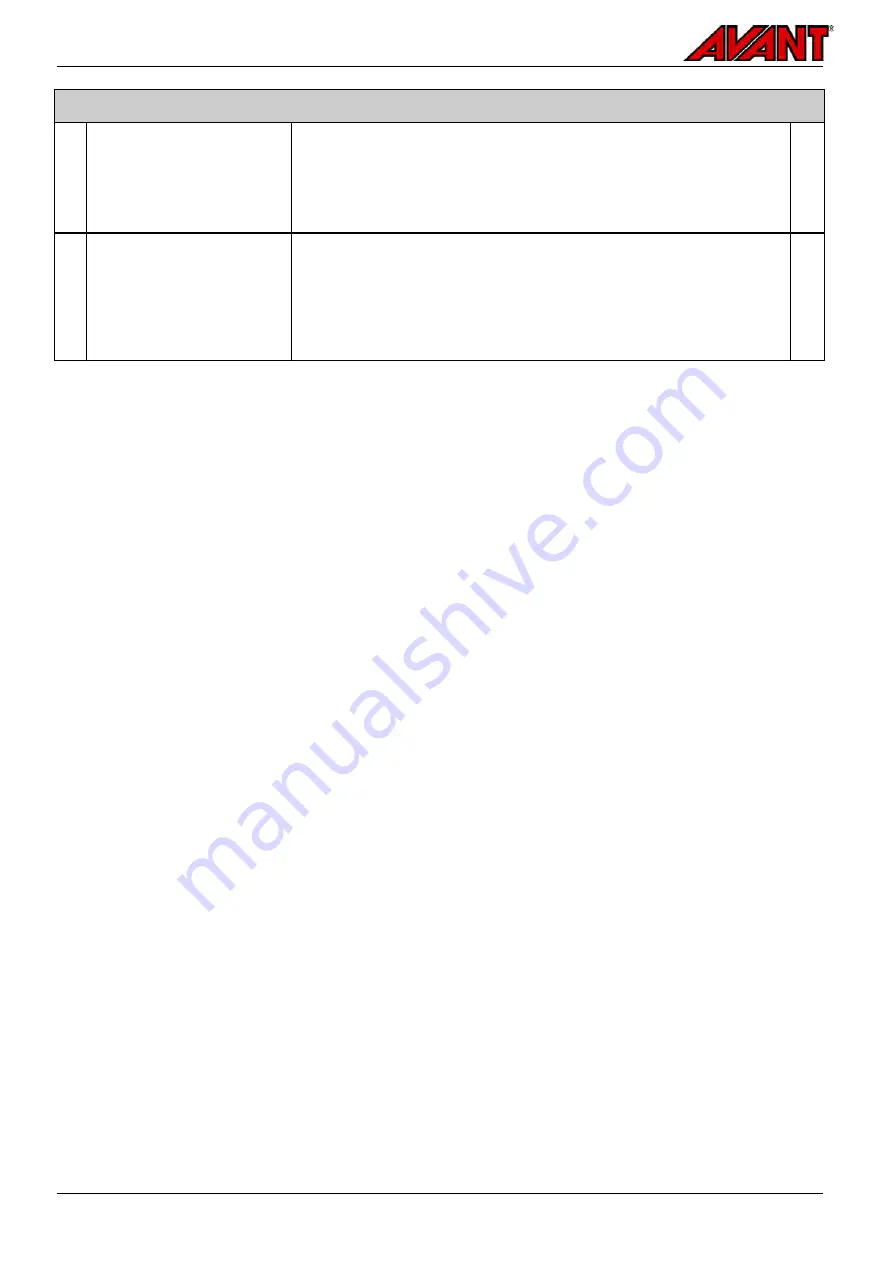
Avant e5
86
Check after starting the loader
11
Drive control and steering
Check operation of pedals and steering after start. Pedals must move freely
and not get stuck or feel stiff
Check that loader stops when not pressing the drive pedals. Do not use the
loader if braking performance is decreased or if the loader creeps
Allow the loader to warm up and check steering
12
Boom movements
Boom should move smoothly to all extreme positions when using without an
attachment
If attachment is fitted, check that the boom moves smoothly within its normal
operating range
Hydraulic hoses or electric cables must not get pinched or stretched in any
position of the boom
Summary of Contents for e5 2018
Page 104: ...Avant e5 104 Notes ...