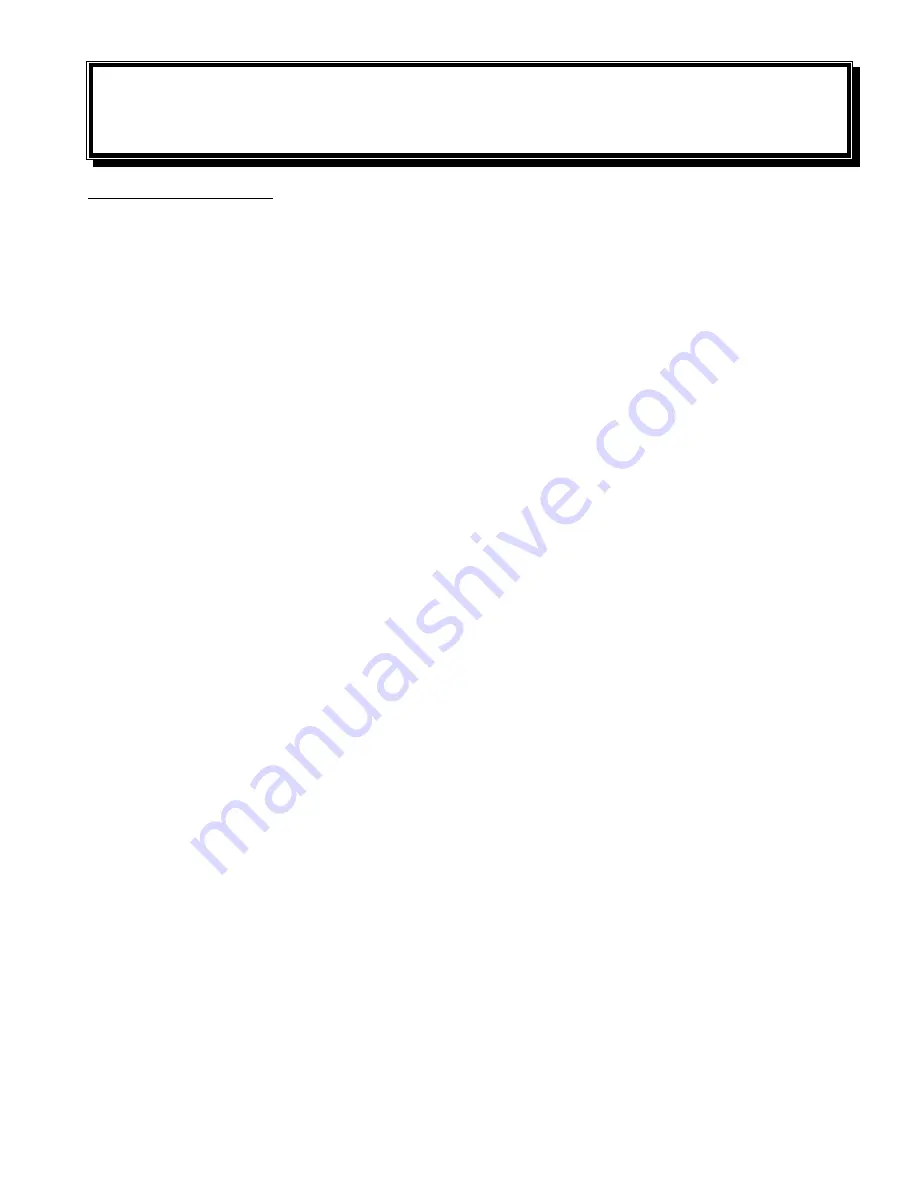
INSPECTION
REQUIREMENTS
3-2.0
8/16/05
PERIODIC INSPECTION
Any deficiencies, such as those listed below, shall be
carefully examined and determination made as to
whether they constitute a hazard:
1. Inspect for deformed, cracked or corroded
members in the crane structure and entire boom.
2. Inspect for loose bolts, particularly mounting bolts.
3. Inspect for cracked or worn sheaves and drums.
4. Inspect for worn, cracked, or distorted parts such
as pins, bearings, shafts, gears, rollers and
devices.
5. Inspect for excessive wear on brake and clutch
system parts and lining.
6. Inspect crane hooks for cracks.
7. Inspect travel steering, braking, and locking devices
for malfunction.
8. Inspect for excessively worn or damaged tires.
9. Inspect hydraulic hose, fittings, and tubing for the
following problems:
A. Evidence of leakage at the surface of the
flexible hose or its junction with metal and
coupling.
B. Blistering, or abnormal deformation to the outer
covering of the hydraulic or pneumatic hose.
C. Leakage at threaded or clamped joints that
cannot be eliminated by normal tightening or
recommended procedures.
D. Evidence of excessive abrasion or scrubbing
on the outer surface of a hose, rigid tube, or
fitting. Means shall be taken to eliminate the
interference of elements in contact or otherwise
protect the components.
10. Inspect hydraulic pumps and motors for the
following problems:
A. Loose bolts and fasteners.
B. Leaks at joints between sections.
C. Shaft seal leaks.
D. Unusual noises or vibrations.
E. Loss of operating speed.
F. Excessive heating of the fluid.
G. Loss of pressure.
11. Inspect hydraulic valves for the following problems:
A. Cracks in valve housing.
B. Improper return of spool to neutral position.
C. Leaks at spools or joints.
D. Sticking spools.
E. Failure of relief valves to attain or maintain
correct pressure setting.
F. Relief valve pressure shall be checked as
specified by the manufacturers.
12. Inspect hydraulic cylinders for the following
problems:
A. Drifting caused by fluid leaking across piston.
B. Rod seals leaking.
C. Leaks at welding joints.
D. Scored, nicked, or dented cylinder rods.
E. Damaged case (barrel).
F. Loose or deformed rod eyes or connecting joints.
13. Inspect hydraulic filters for evidence of rubber
particles on the filter elements indicating possible
hose, “O” ring, or other rubber component
deterioration. Metal chips or pieces on the filter
may denote failure in pumps, motors, or cylinders.
Further inspection will be necessary to determine
the origin of the problem before corrective action
can be taken.
14. Inspect labels to confirm correct location and
legibility. Reference decal layout in this manual for
proper location of decals.
15.
Rope Inspections need not be at equal calendar
intervals and should be more frequent as the
rope approaches the end of useful life.
A
qualified person shall inspect the wire rope based
on such factors as:
A. Expected rope life as determined by experience
on the particular installation or similar
installations.
B. Severity of environment.
C. Percentage of capacity lifts.
D. Frequency rates of operation.
E. Exposure to shock loads.
This inspection shall cover the entire length of the
rope. Only the surface wires need to be inspected
and no attempt should be made to open the rope.
Any deterioration resulting in appreciable loss of
original strength shall be noted and determination
made as to whether use of the rope would constitute
a hazard. A few notable deterioration points are listed
below:
Summary of Contents for 6006EH
Page 2: ......
Page 4: ......
Page 6: ......
Page 10: ......
Page 33: ...NOTES ...
Page 37: ...NOTES ...
Page 45: ...6006EH GENERAL ASSEMBLY HARDWIRED W SLIP RING P N 366600000 6 1 2 15 11 ...
Page 46: ...6 2 2 15 11 6006EH GENERAL ASSEMBLY HARDWIRED W SLIP RING P N 366600000 ...
Page 47: ...6006EH GENERAL ASSEMBLY HARDWIRED W O SLIP RING P N 366780000 6 3 2 15 11 ...
Page 49: ...6 5 2 15 11 6006EH PEDESTAL ASSEMBLY W SLIP RING P N 366640000 ...
Page 50: ...6006EH PEDESTAL ASSEMBLY W SLIP RING P N 366640000 6 6 2 15 11 ...
Page 51: ...6006EH PEDESTAL ASSEMBLY W SLIP RING P N 366640000 2 15 11 6 7 ...
Page 52: ...2 15 11 6 8 6006EH PEDESTAL ASSEMBLY W SLIP RING P N 366640000 ...
Page 53: ...2 15 11 6 9 6006EH PEDESTAL ASSEMBLY W O SLIP RING P N 366781000 ...
Page 54: ...6 10 2 15 11 6006EH PEDESTAL ASSEMBLY W O SLIP RING P N 366781000 ...
Page 55: ...6 11 2 15 11 6006EH PEDESTAL ASSEMBLY W O SLIP RING P N 366781000 ...
Page 56: ...6 12 2 15 11 6006EH PEDESTAL ASSEMBLY W O SLIP RING P N 366781000 ...
Page 59: ...6006H ROTATION GEARBOX P N 160407 6 15 0 9 12 05 ...
Page 61: ...6006EH ACTUATOR ASSEMBLY P N 297025 6 17 0 04 26 10 ...
Page 77: ...NOTES ...
Page 81: ...6006EH HYDRAULIC POWER UNIT P N 366650000 8 3 0 9 12 05 ...
Page 97: ......
Page 99: ...NOTES ...
Page 101: ......
Page 103: ......
Page 104: ......
Page 105: ......