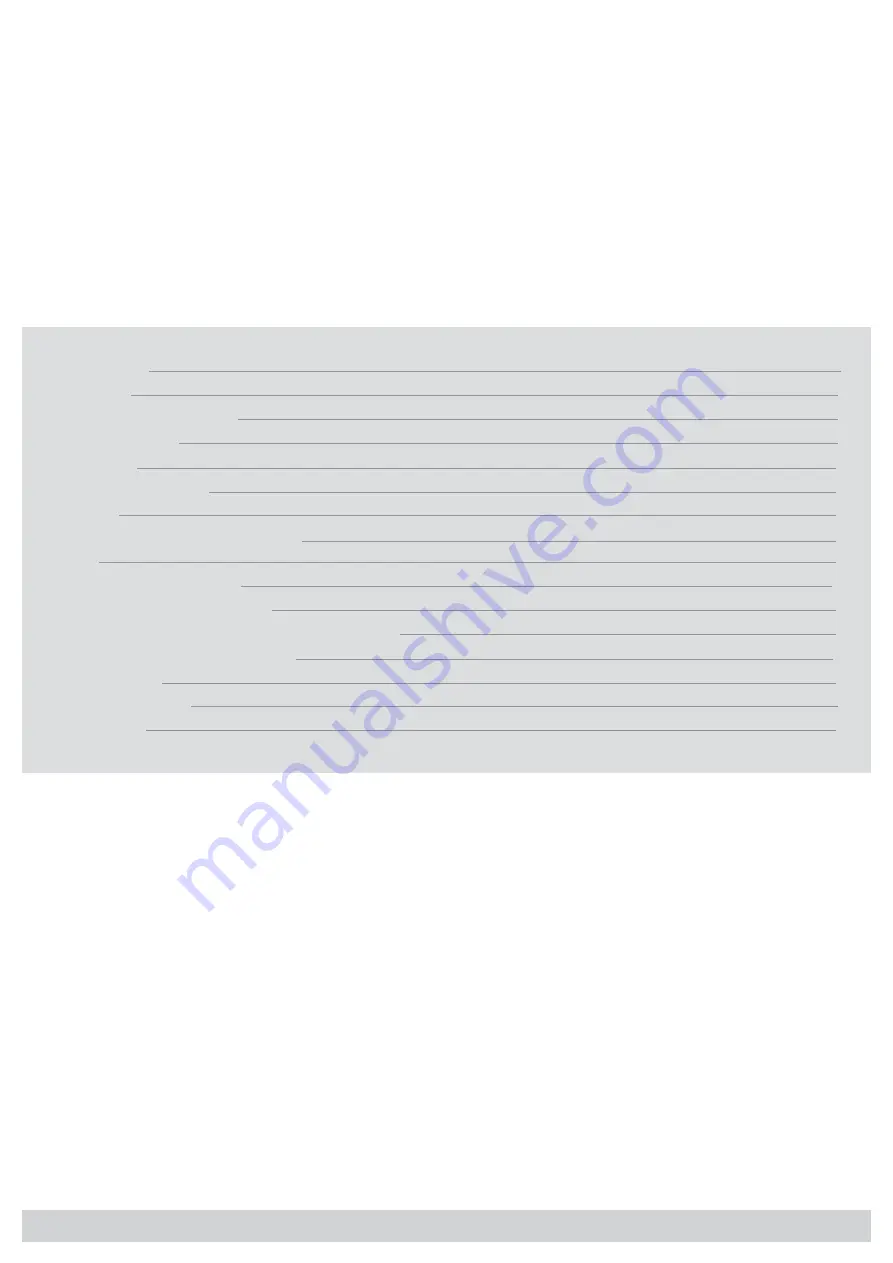
YL-240 4500KG BASE PLATE CAR HOIST
Installation and operation manual
3
CONTENTS
Important notice
4
Introduction 6
Check parts before assembly
8
Machine parameters
10
Tools required
12
Specifications of concrete
13
Installation 13
Important power unit installation notes
24
Test run
25
Lift start up/final adjustments
26
Optional and standard accessories
27
Owner/operator responsibilities & lift operation safety
28
Wire rope inspection and maintenance
33
Safe lift operation
34
Troubleshooting guide
35
Drawing details
37
PH 1300 232 153
HIGHLIFT