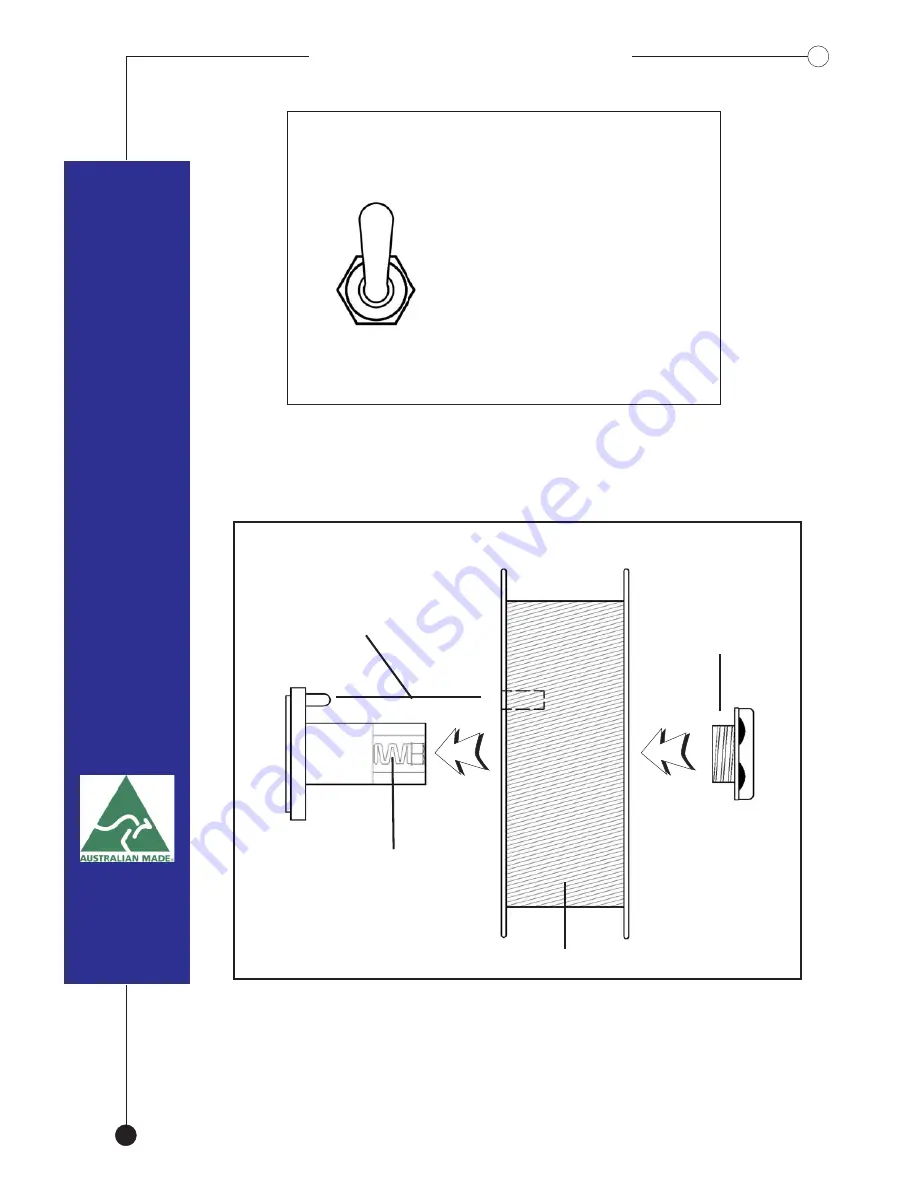
WIRE SPOOL ASSEMBLY
WIRE SPOOL ASSEMBLY
TIP..
12
NOTE
9
TOGGLE SWITCH
TOGGLE SWITCH
Steel
Alum
Select the appropriate
wire speed for your
application.
Slow speed for Steel.
Fast for Aluminium.
The Switch is located
on the back of the unit.
15 Kg Wire Spool
Spool hub
Adjustment
Locking Nut
Locating Pin
When fitting a spool of wire, ensure that the
locating lug is correctly aligned with the spool.
Do not overtighten the locking nut.