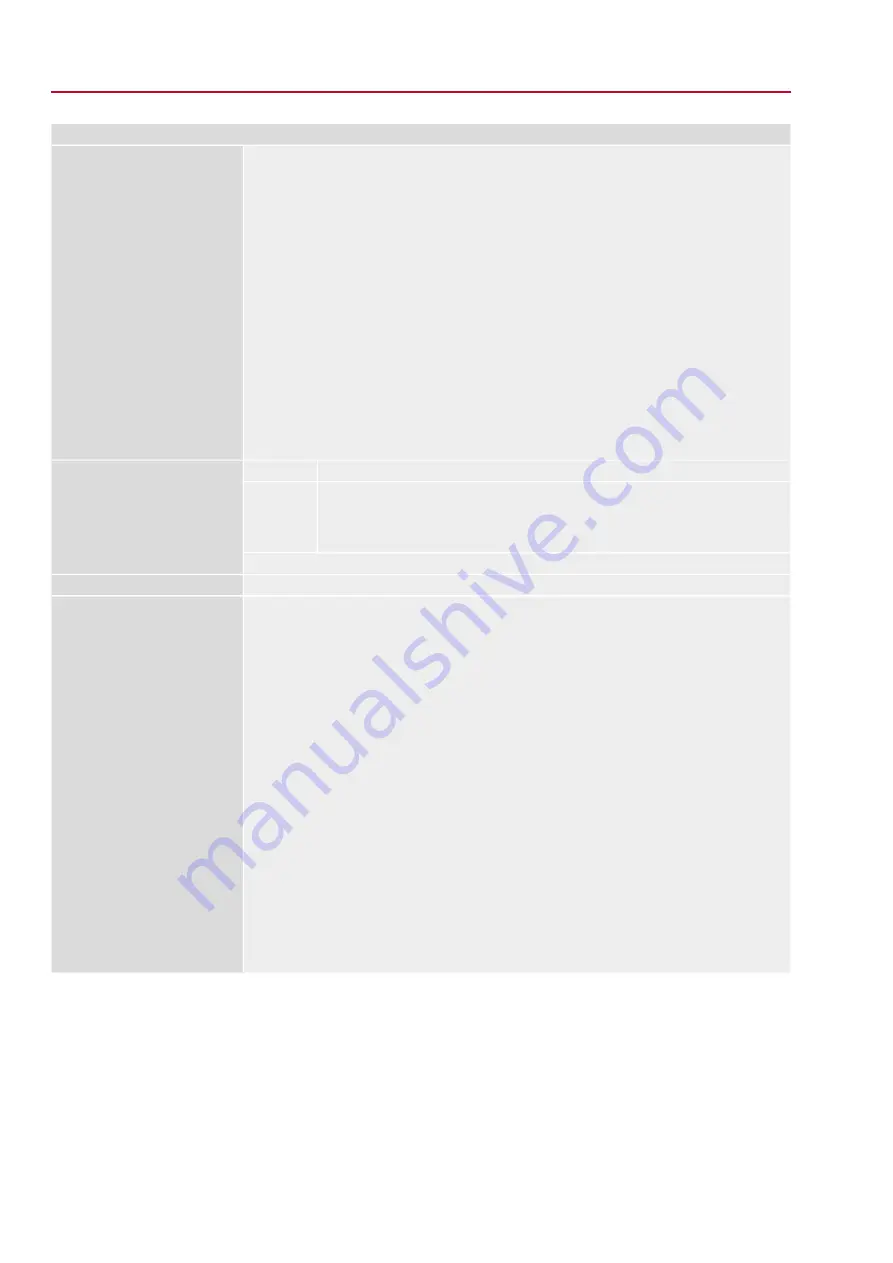
Features and functions
●
2 free analogue inputs (0/4 – 20 mA), 4 free digital inputs
-
Signal transmission is made via fieldbus interface
●
Inputs OPEN, STOP, CLOSE, EMERGENCY, I/O interface, MODE (via opto-isolator thereof OPEN,
STOP, CLOSE, MODE with one common and EMERGENCY, I/O interface respectively without
common)
-
OPEN, STOP, CLOSE, EMERGENCY control inputs
-
I/O interface: Selection of control type (fieldbus interface or additional input signals)
-
MODE: Selection between open-close duty (OPEN, STOP, CLOSE) or modulating duty (0/4 –
20 mA position setpoint)
-
Additionally 1 analogue input (0/4 – 20 mA) for position setpoint
●
Inputs OPEN, STOP, CLOSE, EMERGENCY, I/O interface, MODE (via opto-isolator thereof OPEN,
STOP, CLOSE, MODE with one common and EMERGENCY, I/O interface respectively without
common)
-
OPEN, STOP, CLOSE, EMERGENCY control inputs
-
I/O interface: Selection of control type (fieldbus interface or additional input signals)
-
MODE: Selection between open-close duty (OPEN, STOP, CLOSE) or modulating duty (0/4 –
20 mA position setpoint)
-
Additionally 1 analogue input (0/4 – 20 mA) for setpoint position and 1 analogue input (0/4 – 20
mA) for actual process value
Modbus TCP/IP interface with addi-
tional input signals (option)
24 V DC, current consumption: approx. 10 mA per input
Standard:
Control voltage/current consumption
for control inputs
48 V DC, current consumption: approx. 7 mA per input
60 V DC, current consumption: approx. 9 mA per input
100 – 125 V DC, current consumption : approx. 15 mA per input
100 – 120 V AC, current consumption : approx. 15 mA per input
Options:
All input signals must be supplied with the same potential.
Via Modbus TCP/IP interface
Status signals
Additional, binary output signals (only available in combination with additional input signals (option)
●
6 programmable output contacts:
-
5 potential-free NO contacts with one common, max. 250 V AC, 1 A (resistive load)
Standard assignment: End position CLOSED, end position OPEN, selector switch REMOTE,
torque fault CLOSE, torque fault OPEN
-
1 potential-free change-over contact, max. 250 V AC, 5 A (resistive load)
Standard assignment: Collective fault signal (torque fault, phase failure, motor protection tripped)
●
6 programmable output contacts:
-
5 potential-free change-over contacts with one common, max. 250 V AC, 1 A (resistive load)
-
1 potential-free change-over contact, max. 250 V AC, 5 A (resistive load)
●
6 programmable output contacts:
-
6 potential-free change-over contacts without one common, max. 250 V AC, 5 A (resistive load)
●
6 programmable output contacts:
-
4 mains failure proof potential-free NO contacts with one common, max. 250 V AC, 1 A (resistive
load), 1 potential-free NO contact, max. 250 V AC, 1 A (resistive load), 1 potential-free change-
over contact, max. 250 V AC, 5 A (resistive load)
●
6 programmable output contacts:
-
4 mains failure proof potential-free NO contacts, max. 250 V AC, 5 A (resistive load), 2 potential-
free change-over contacts, max. 250 V AC, 5 A (resistive load),
All binary output signals must be supplied with the same potential.
●
Analogue output signal for position feedback
-
Galvanically isolated position feedback 0/4 – 20 mA (load max. 500
Ω
)
Modbus TCP/IP interface with addi-
tional output signals (option)
74
SQEx 05.2 – SQEx 14.2 / SQREx 05.2 – SQREx 14.2 Control unit: electronic (MWG)
Technical data
ACExC 01.2 Non-Intrusive Modbus TCP/IP
Summary of Contents for SQEx 05.2
Page 91: ...91 AUMA worldwide...