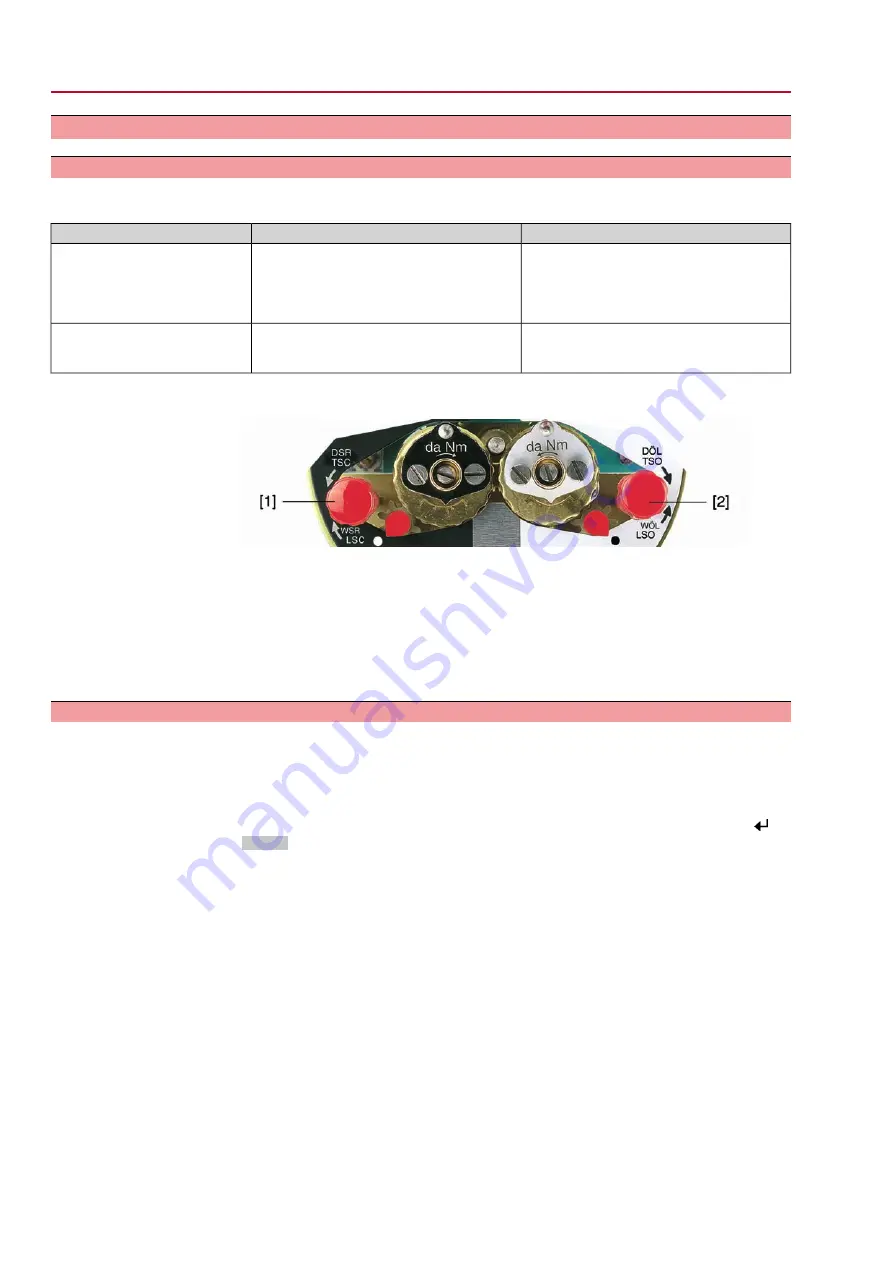
10.
Corrective action
10.1
Faults during commissioning
Table 12:
Faults during commissioning
Remedy
Possible causes
Fault description
Determine overrun: Overrun = travel covered
from switching off until complete standstill.
Set limit switching again considering the
overrun (turn handwheel back by the amount
of the overrun).
The overrun was not considered when setting
the limit switching.
The overrun is generated by the inertia of
both the actuator and the valve and the delay
time of the controls.
Fault in end position
Actuator runs to end stop alt-
hough the limit switches work
properly.
Check setting, if required, reset end positions.
→
Check switches and replace them, if requi-
red.
Switch is defective or switch setting is incor-
rect.
Limit and/or torque switches do
not trip.
Switch check
The red test buttons [1] and [2] are used for manual operation of the switches:
1.
Turn test button [1] in direction of the TSC arrow: Torque switch CLOSED trips.
2.
Turn test button [2] in direction of the TSO arrow: Torque switch OPEN trips.
If the actuator is equipped with a DUO limit switching (option), the intermediate
position switches (LSA and LSB) will be operated at the same time as the torque
switches.
1.
Turn test button [1] in direction of the LSC arrow: Limit switch CLOSED trips.
2.
Turn test button [2] in direction of the LSO arrow: Limit switch OPEN trips.
10.2
Fault indications and warning indications
Faults interrupt or prevent the electrical actuator operation. In the event of a fault,
the display backlight is red.
Warnings have no influence on the electrical actuator operation. They only serve
for information purposes.
Collective signals include further indications which can be displayed via the
Details
push button.
58
SGExC 05.1 – SGExC 12.1 Control unit: electromechanic
Corrective action
ACExC 01.2 Intrusive Modbus RTU