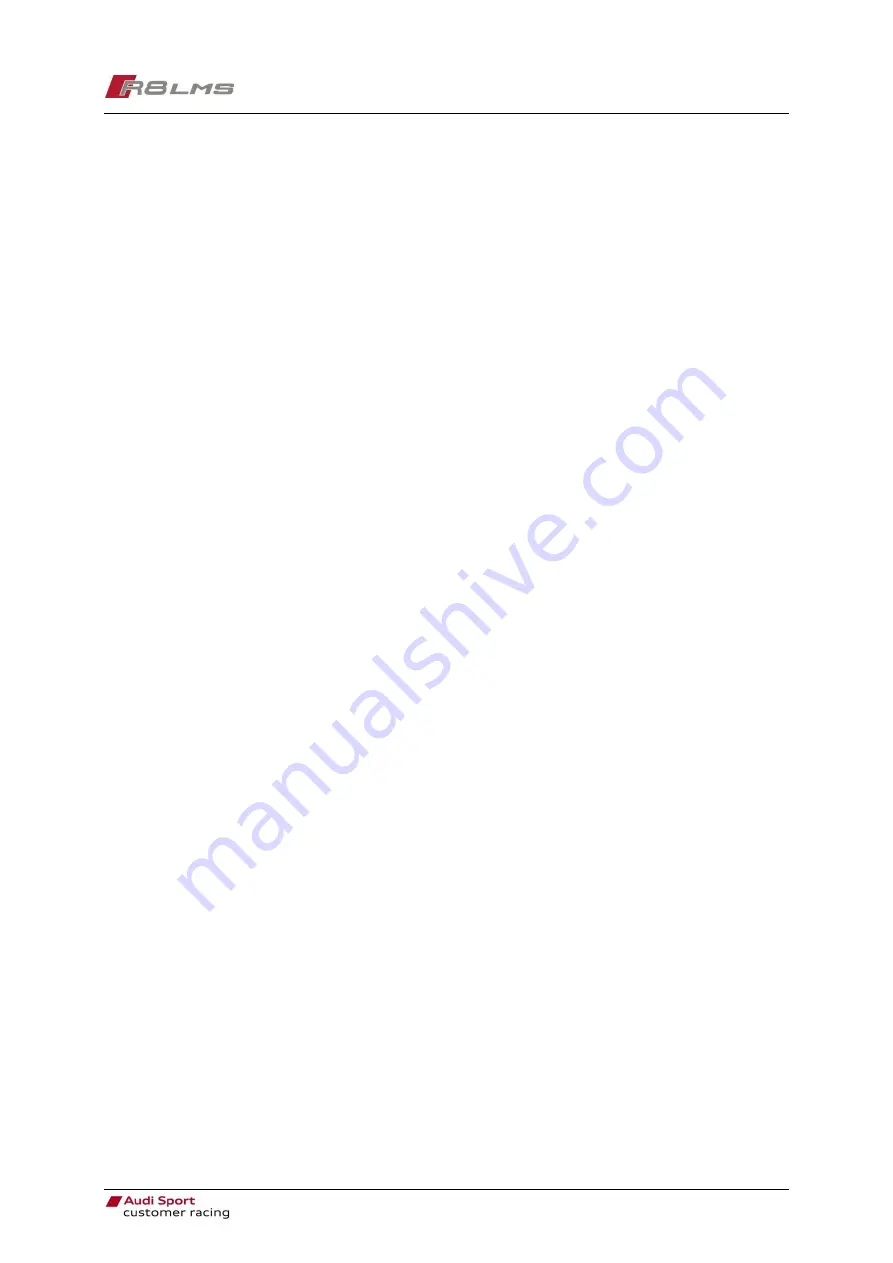
Contents
Version 1 2016-01-01
3 / 113
700- Pneumatic Gearshift and Pedals ..................................................... 65
700 - 1.1 Longitudinal Adjustment Pedal Unit ........................................ 65
700 - 1.2 Throttle Pedal ........................................................................ 69
800- Bodywork, Chassis Parts, Seat and Air Conditioning .......................... 77
800 - 1.1 Homologation ........................................................................ 77
800 - 1.4 Additional Inserts................................................................... 81
800 - 1.5 Shoulder Strap Mounting ........................................................ 82
801- Aerodynamics .............................................................................. 83
900- Electric and Data Acquisition .......................................................... 87
901- Engine Warm-Up Procedure / Engine Start ...................................... 98
901 - 1 Preparation before Engine Start .................................................... 98
901 - 1.1 Checking / Adjusting Gearbox Potentiometer ............................ 98
901 - 1.2 Checking Engine Oil Level ...................................................... 100
901 - 1.3 Checking Gearbox Oil Level .................................................... 101
901 - 1.4 Fuel, Coolant and Coolant Additive, Steering Oil and Brake Fluid
................................................................................................ 102
901 - 1.5 Preparation Warm Up Procedure / ‘Warm up’ ......................... 104
901 - 2 Warming up / Cooling down the Engine and Gearbox .................... 105
901 - 2.1 Warm up Procedure .............................................................. 105
901 - 2.2 Cooling Down Procedure ....................................................... 106
902 – Service and Maintenance Contacts ............................................... 107
Summary of Contents for R8 LMS 2018
Page 1: ...Handbook Audi R8 LMS MODIFIED TO COVER 2018...
Page 8: ...Car Views Version 1 2016 01 01 8 113 Car Views...
Page 9: ...Car Views Version 1 2016 01 01 9 113...
Page 10: ...Car Views Version 1 2016 01 01 10 113...
Page 78: ...800 Bodywork Chassis Parts Seat and Air Conditioning Version 1 2016 01 01 78 113...