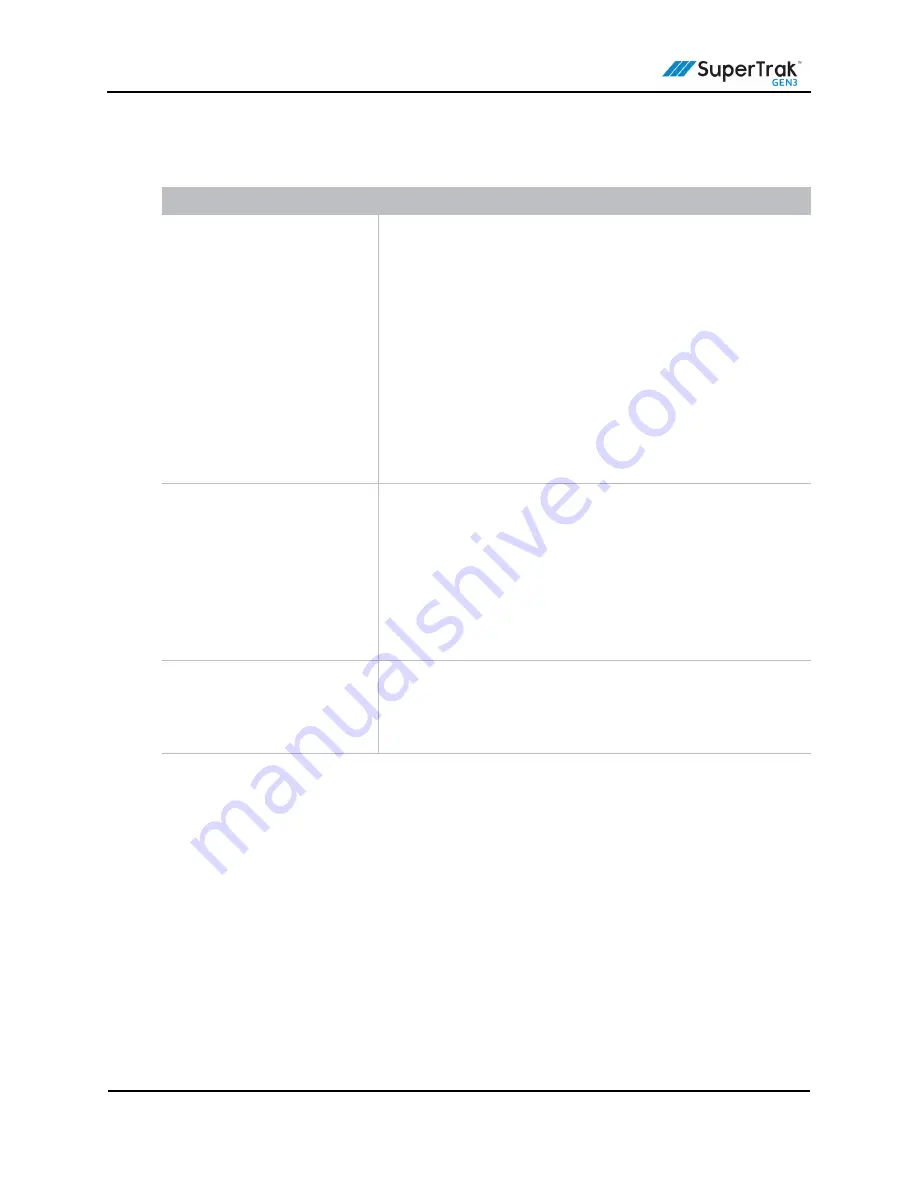
258
SuperTrak™ GEN3 System Operation and Maintenance Manual
Rev. 9 (12-2021)
Troubleshooting
Pallet Faults
Fault
Resolution
Pallet following error
• Check for mechanical or other interference with the pallet
(for example, a jammed part). The fault indicates the
location.
• Inspect the pallet.
• Verify that a coil fuse is not blown.
If a pallet travels across a coil with a blown fuse, pallet
momentum is usually adequate to allow acceptable
control. However, if the pallet attempts to stop in the
vicinity of this coil, it will have poor control, which will
trigger a following error.
See
• Check for a damaged upper v-rail, flat wear strip, or
motor cover label.
Pallet lost position
• Check the encoder strip, to make sure that it is not
damaged.
See
• Check encoder calibration.
See the TrakMaster built-in help for the calibration
procedure.
• Verify the encoder functionality. View the TrakMaster
Encoder screen, to make sure the encoders are
functioning.
Pallets stop at section joints
Verify that the rails are correctly aligned. If the rails of
sections are not correctly aligned, pallets may not be able to
move across the joints of low power sections. Make sure that
magnetic shunts are installed in the correct orientation.
Summary of Contents for SuperTrak GEN3
Page 1: ...Rev 9 December 2021...
Page 2: ......
Page 3: ...SuperTrak GEN3 Conveyance Platform Modular Conveyor Operation and Maintenance Manual...
Page 6: ......
Page 12: ...This page is intentionally blank...
Page 30: ...This page is intentionally blank...
Page 58: ...This page is intentionally blank...
Page 296: ...This page is intentionally blank...
Page 300: ...This page is intentionally blank...
Page 364: ...This page is intentionally blank...
Page 366: ...This page is intentionally blank...