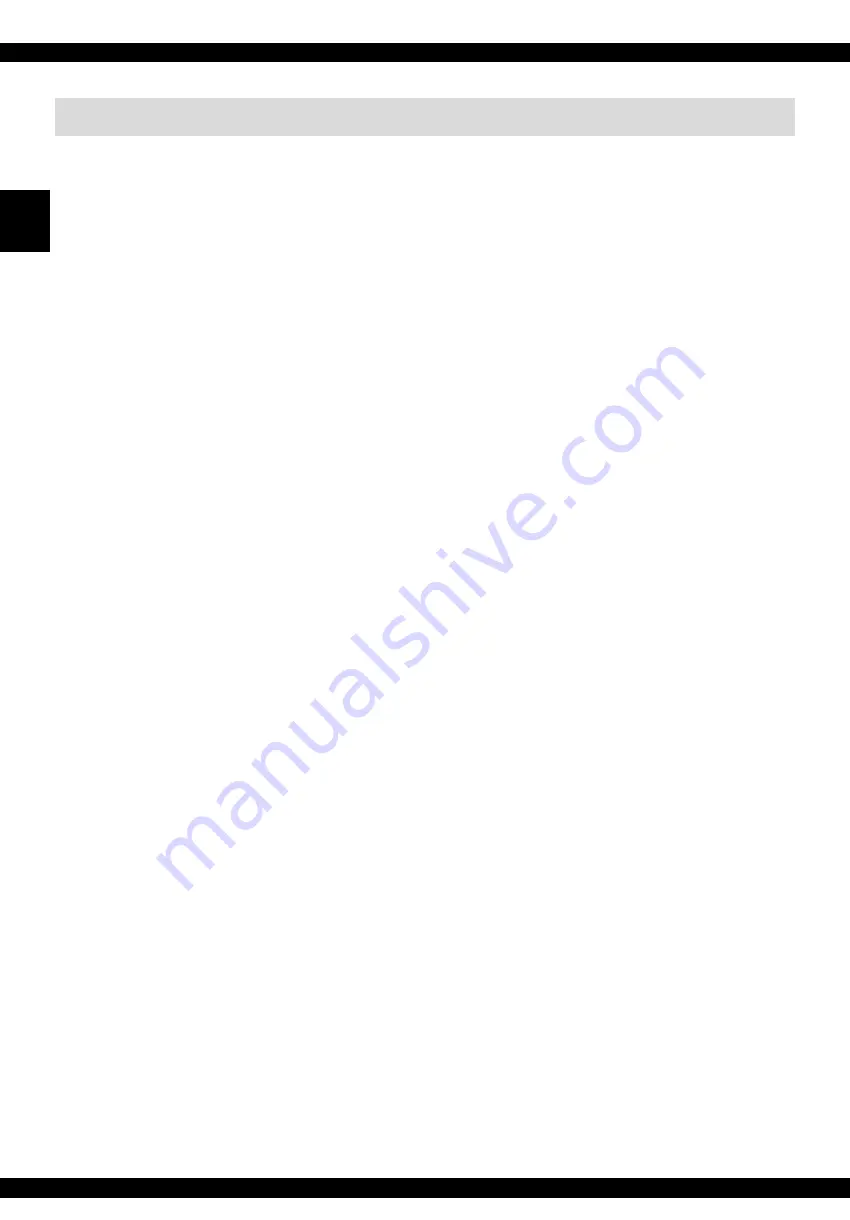
EN
www.atmos.cz
36 - EN
Operation manual - EN
RECORD OF INSTALLATION OF THE BOILER AND BURNER
The installation was performed by:
Company: ...............................................................................................................................................
Street: ..................................................... Town: .............................................................................
Telephone: ..............................................
Country: .........................................................................
Ascertained data:
Chimney:
Flue-gas
duct:
Dimensions: ............................................. Diameter: ..................................................
Height: ...................................................... Length: ......................................................
Chimney draught: .....................................* Number of elbow pieces: ..........................
Date of last inspection: ............................. Waste gas temperature: .............................*
Boiler connected with mixing valves and fittings (brief description of connection):
.........................................................................................................................................
.........................................................................................................................................
.........................................................................................................................................
.........................................................................................................................................
Fuel:
Measured
data:
Type: .....................................................
Waste gas temperature: ............................. °C
Size: ......................................................
Emissions in stabilised state : CO .................
Moisture content: .................................*
CO
2
................
O
2
..................
Person responsible for the inspection: ............................................ Date: ............................
Stamp : ...............................................
Customer’s signature: .....................................
(Responsible person’s signature)
* measured values