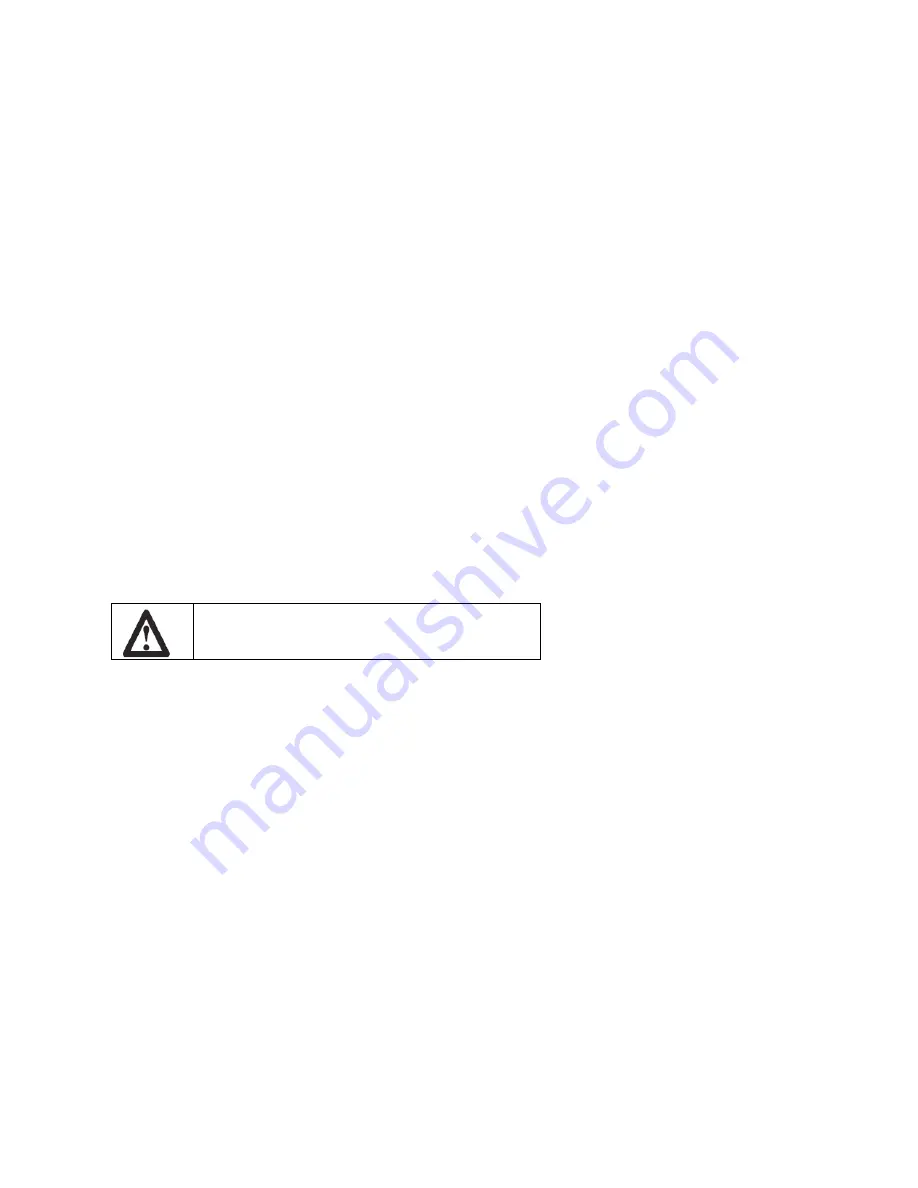
REV. 01 2012
7 / 30
CHAPTER 3 - PACKING, TRANSPORT AND STORAGE
Only skilled personnel who are familiar with the lift and this manual shall be allowed to carry out
packing, lifting, handling, transport and unpacking operations.
3.1
PACKING
The packing of the lift is delivered in following components:
¾
N. 2 base units packed in a steel frame, wrapped up in non-scratch waterproof material and
sealed with 2 straps
¾
N. 1 power unit packed in a plywood box
¾
N. 4 drive-on ramps wrapped up in non-scratch waterproof material, including N. 4 rubber
pads, N. 4 hydraulic hoses and N. 8 anchor bolts.
(If requested, optional accessories are available to satisfy each customer’s requirements).
The average weight of the package is
2,300 LBS.
3.2 LIFTING AND HANDLING
When loading/unloading or transporting the equipment to the site, be sure to use suitable loading (e.g.
cranes, trucks) and hoisting means. Be sure also to hoist and transport the components securely so that
they cannot drop, taking into consideration the package’s size, weight and center of gravity and it’s
fragile parts.
Hoist and handle only one package at a time
3.3
STORAGE AND STACKING OF PACKAGES
Packages must be stored in a covered place, out of direct sunlight and in low humidity, at a
temperature between 14°F and 104°F.
Stacking is not recommended: the package’s narrow base, as well as its considerable weight and size
make it difficult and hazardous.
3.4
DELIVERY AND CHECK OF PACKAGES
When the lift is delivered, check for possible damage due to transport and storage; verify that what is
specified in the manufacturer’s confirmation of order is included. In case of damage in transit, the
customer must immediately inform the carrier of the problem.
Packages must be opened paying attention not to cause damage to people (keep a safe distance when
opening straps) and parts of the lift (be careful the objects do not drop from the package when
opening).