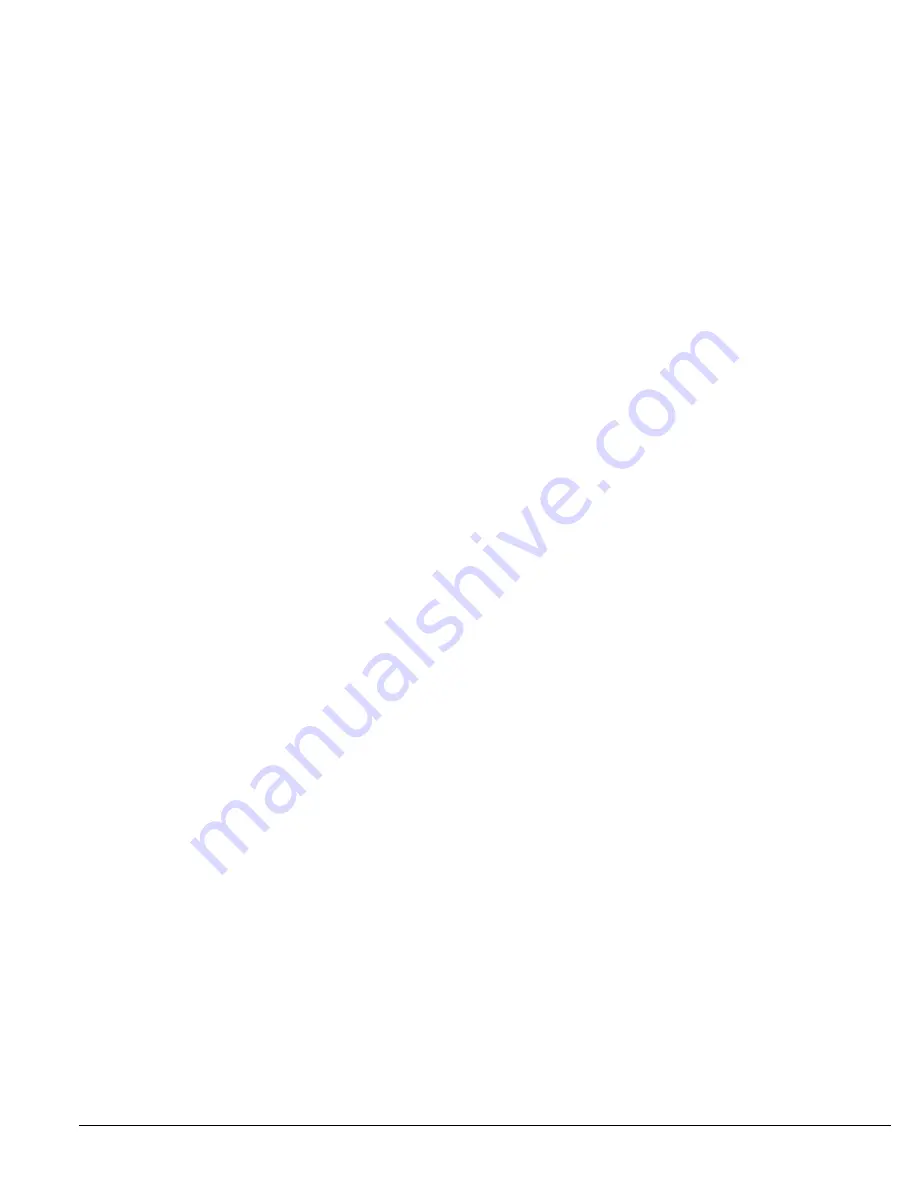
1310 3011 08
5
14 All regulating and safety devices shall be maintained
with due care to ensure that they function properly.
They may not be put out of action.
15 Care shall be taken to avoid damage to safety valves
and other pressure relief devices, especially to avoid
plugging by paint, oil coke or dirt accumulation,
which could interfere with the functioning of the
device.
16 Pressure and temperature gauges shall be checked
regularly with regard to their accuracy. They shall be
replaced whenever outside acceptable tolerances.
17 Parts shall only be replaced by genuine Atlas Copco
replacement parts.
18 Safety devices shall be tested as described in the
maintenance schedule of the instruction book(s) to
determine that they are in good operating condition.
19 Never use flammable solvents or carbon tetrachloride
for cleaning pans. Take safety precautions against
toxic vapors when cleaning parts in or with cleaning
products.
20 Observe scrupulous cleanliness during maintenance
and repair. Keep away dirt by covering the parts and
exposed openings with clean cloth, paper or tape.
21 Protect the engine, alternator, air intake filter,
electrical and regulating components, etc. to prevent
moisture ingress, e.g. when steam-cleaning.
22 When performing any operation involving heat,
flames or sparks on a machine, the surrounding
components shall first be screened with non-
flammable material.
23 Never use a light source with open flame for
inspecting the interior of a machine, pressure vessel,
etc.
24 On portable units, support the drawbar and axle(s)
securely if working underneath the units or when
removing a wheel. Do not rely on jacks.
25 Prior to stripping a compressor, engine or other
machine or undertaking major overhaul on it, prevent
all movable parts with a mass exceeding 15 kg (30
lbs) from rolling over or moving.
26
When repair has been completed, make sure that no
tools, loose parts or rags are left in, or on, the
machine, the prime mover or the driving gear. The
machine shall be barred several revolutions to ensure
that there is no mechanical interference within the
machine or driver.
1.3
Safety during use and operation
To lift a unit, all loose or pivoting parts, e.g. doors shall
first be securely fastened. Do not attach cables, chains or
ropes directly to the lifting eye; apply a crane hook or
lifting shackle meeting local safety rules.
Helicopter lifting using the lifting eye is forbidden.
It is strictly forbidden to dwell or stay in the risk zone under a
lifted load. Never lift the unit over people or residential areas.
Lifting acceleration and retardation shall be kept within safe limits.
1
Before towing the unit:
- ascertain that the pressure vessel(s) is (are) depressurized,
- check the drawbar, the brake system and the towing eye.
Also check the coupling of the towing vehicle,
- check that the pivot wheel or stand leg is safely locked in
the raised position,
- ascertain that the towing eye can swivel freely on the hook,
- check that the wheels are secure and that the tires are in
good condition and inflated correctly,
- connect the signal cable, check all lights and connect the
pneumatic brake couplers,
- attach the safety break-away cable to the towing vehicle,
-
remove wheel chocks, if applied, and disengage the parking
brake.
-
Apply safety chains to tow vehicle.
2
If the unit is to be backed up by the towing vehicle, disengage
the overrun brake mechanism (if equipped).
3
Never exceed the maximum towing speed of the unit.
4
Place the unit on level ground and chock the wheels before
disconnecting the unit from the towing vehicle. Unclip the
safety break-away cable
5
When the unit has to operate in a fire-hazardous environment,
each engine exhaust has to be provided with a spark arrestor
to trap incendiary sparks.
6
The exhaust contains carbon monoxide which is a lethal gas.
When the unit is used in a confined space, conduct the engine
exhaust to the outside atmosphere by a pipe of sufficient
diameter (min. 4 inches); do this in such a way that no extra
back pressure is created for the engine. If necessary, install an
extractor.
7
When operating in a dust-laden atmosphere, place the unit so
that dust is not carried towards it by the wind. Operation in
clean surroundings considerably extends the intervals for
cleaning the air intake filters and the cores of the coolers.
8
Locate the unit away from walls. Take all precautions to
ensure that hot air exhausted from the engine and driven
machine cooling systems cannot be recirculated. If such hot
air is taken in by the engine or driven machine cooling fan,
this may cause overheating of the unit; if taken in for
combustion, the engine power will be reduced.
9
No external force may be exerted on the air outlet valves, e.g.
by pulling on hoses or by installing auxiliary equipment
directly to a valve, e.g. a water separator, a lubricator, etc.
10 Distribution pipework and air hoses must be of correct size
and suitable for the working pressure. Never use frayed,
damaged or deteriorated hoses. Replace hoses and flexibles
of which the lifetime expired. Use only the correct type and
size of hose end fittings and connections.