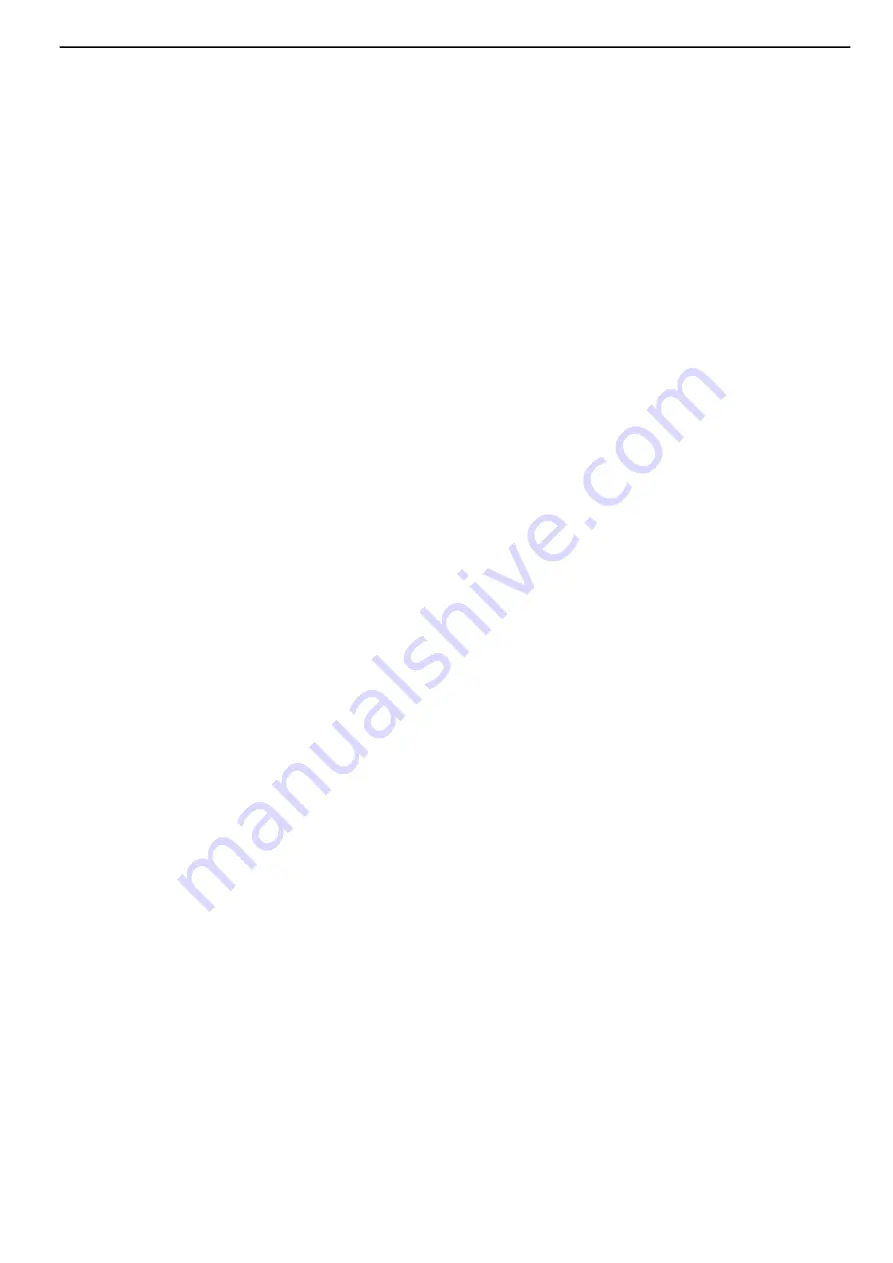
Maintenance
Service instructions
Overhaul and preventive maintenance are recommended at regular inter-
vals once a year or after max. 100 000 tightening operations at the latest,
whichever comes first. More frequent overhauls may be required if the
machine is used for heavy-duty applications. If the machine fails to
function correctly, it must be decommissioned immediately for inspec-
tion.
The strainer at the air inlet must be cleaned regularly in order to pre-
vent clogging due to contamination. The machine capacity will otherwise
be reduced.
All parts must be cleaned thoroughly during overhaul work and defect-
ive or worn parts must be replaced
It is important to ensure that the threaded connections on the machine
are tightened properly; i.e. in accordance with the specifications in the
exploded views. Lubricate the threads with grease prior to fitting.
A
All O-rings must be greased prior to assembly.
When the machine is in constant operation, installation of an Atlas Copco
DIM oil mist lubricating device or a Dosol type single point lubricating
device is recommended.
Impact mechanism
Check the specified wear limits and replace all parts which exceed these.
See Inspection.
A
Recommended maximum wear limits for the clutch jaw, anvil
and driver.
Rust protection and internal cleaning
Water in the compressed air, dust and wear particles cause rust and
sticking of vanes, valves etc. An air filter should be installed close to
the machine (see 'Air quality'). Before longer standstills, flush with oil
(some drops) into the air inlet, run the machine for 5-10 seconds when
absorbing the oil in a cloth.
How to optimize service and performance of your
impact wrench
The service life of the impact mechanism is mainly de-
pendent on:
•
service intervals
•
air pressure
•
tightening time/torque
•
number of tightening
•
socket/bolt size
•
socket length
7
© Atlas Copco Industrial Technique AB - 9836 6515 00
Service
EN
LMS08 SR42