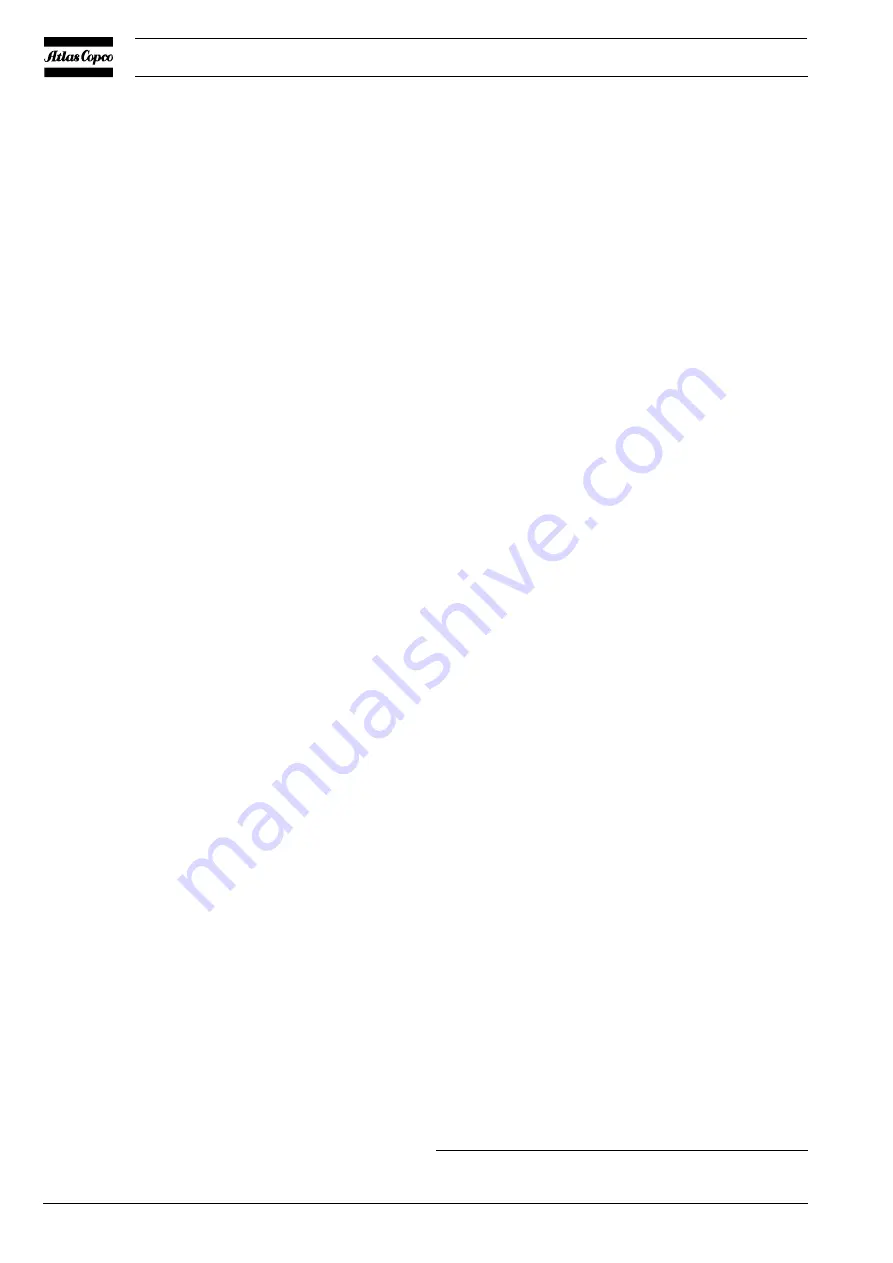
2920 1190 05
30
Industrial Air Division
Instruction book
6 Problem solving
-
Before starting repairs, press stop button O (9-Fig. 7a), wait
until the compressor has stopped, switch off isolator switch
(S0-Figs. 1 and 3a) and switch off the voltage. Close air
outlet valve (AV-Fig. 1), the air outlet valve can be locked
as described in section 4. Open manual drain valve (Dm-
Fig. 5) and wait for at least 2 minutes (time needed for
the compressor to depressurize) before starting any
mechanical repairs. Wait at least 6 minutes before
starting any electrical repairs as hazardous high voltage
remains on the condensers of the start and speed
regulation unit for 6 minutes after switching off the
voltage. Furthermore, apply all relevant safety precautions,
including those mentioned in this book.
-
The chart helps to solve mechanical problems. An electrical
fault must be traced by an electrician. Check that the wires
are not damaged and that they are clamped tight to their
terminals.
-
Consult the "User manual for Elektronikon regulator" if a
service message or fault message appears on the display
(4-Fig. 7a) or when alarm LED (3-Fig. 7a) is alight or blinks.
Mechanical faults and suggested remedies (Figs. 2)
Explanation of the table below:
-
Conditions of the compressor, always preceded by a number,
are printed in bold.
-
Each possible fault is followed by its relevant suggested
remedy and both are preceded by the same letter.
1. Condensate is not discharged from moisture trap during
operation
a. Discharge flexible clogged
a. Check and correct as necessary
b. Float valve malfunctioning
b. Remove float valve assembly, clean and check
2. Compressor air output or pressure below normal
a. Air consumption exceeds air output of compressor
a. Check equipment connected
b. Choked air inlet filter element (AF)
b. Replace filter element
c. Solenoid valve (Y1) malfunctioning
c. Remove and check valve, replace if necessary
d. Oil separator element (OS) clogged
d. Replace element
e. Air leakage
e. Check and correct as necessary
f. Safety valve (SV) leaking
f. Remove and check. Replace if not airtight after
reinstalling
g. Compressor element (E) out of order
g. Consult Atlas Copco
Only on GA50 VSD:
h. Nozzle (Rf1) in wrong position
h. Correct the position of the restrictor, consult section 4.2.1
3. Safety valve (SV) blows
a. Minimum pressure valve (Vp) malfunctioning
a. Remove and check. Replace defective parts
b. Oil separator element (OS) clogged
b. Replace element
c. Safety valve (SV) out of order
c. Remove and check. Replace if not airtight after
reinstalling
4. Element outlet 1) or air outlet temperature above normal
a. On air-cooled compressors: insufficient cooling air or
cooling air temperature too high
a. Check for cooling air restriction or improve ventilation
of compressor room. Avoid recirculation of cooling air.
If installed, check capacity of compressor room fan
b. On water-cooled compressors: insufficient cooling
water flow or cooling water temperature too high
b. Decrease temperature, if possible, or increase water flow
c. Oil level too low
c. Check and correct as necessary
d. Oil cooler (Co) clogged
d. Clean cooler
e. By-pass valve (BV) malfunctioning
e. Remove and test valve
f. Air cooler (Ca) clogged
f. Clean cooler
g. On water-cooled compressors: restriction of cooling
water system due to dirt or formation of scale
g. Consult Atlas Copco
h. Compressor element (E) out of order
h. Consult Atlas Copco
5. Motor temperature above normal
a. Insufficient cooling air or cooling air temperature too
high
a. Check for cooling air restriction or improve ventilation
of compressor room. Avoid recirculation of cooling air.
If installed, check capacity of compressor room fan
b. Insufficient sealing of door panels
b. Check that all doors are closed, check seals of door
panels.
1) A warning message will appear on display (4-Fig. 7a).