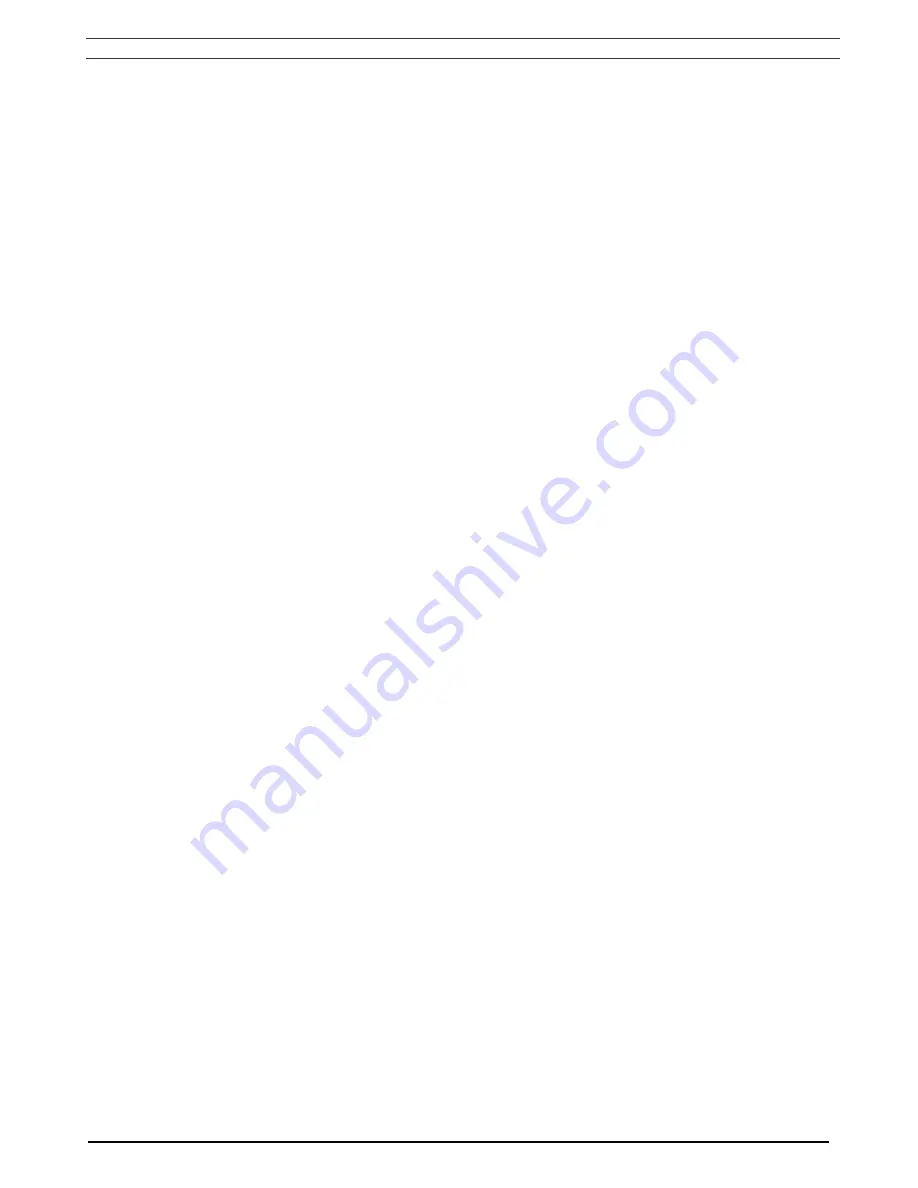
Instruction book
2920 1521 00
29
3.3 During operation
3.3.1 Multi
1. If the automatic operation LED (8-Fig. 1.11) is alight, the regulator is automatically controlling the
compressor modules (starting/stopping).
2. Check the readings on display (2-Fig. 1.11). In case of a warning or shut-down condition, see
section 8.3.
3. Check that condensate is discharged automatically from outlet (2-Figs. 1.9) during running.
Note:
The dewpoint will deviate from nominal when the nominal conditions are exceeded. If the
dewpoint remains too high or unstable, consult section 6.
3.3.2 Skid - Tank-mounted - Twin
1. Check the starting and stopping pressures (1-Fig. 1.10).
2. Regularly open the drain valve underneath the air receiver for a few seconds, close the valve after
draining.
3.4 Stopping
3.4.1 Multi
1. Press stop button (9-Fig. 1.11).
2. Close air outlet valve (3-Figs. 1.5/1.6).
3. Switch off the voltage.
4. Open condensate drain valve (1-Fig. 1.9).
3.4.2 Skid - Tank-mounted - Twin
1. Move switch (2-Fig. 1.10) to OFF.
2. Close air outlet valve (2-Figs. 1.2/1.4).
3. Switch off the voltage.
4. Open the condensate drain valve underneath the air receiver (if provided) for a few seconds, close
the valve after draining.
3.5 Taking out of operation at end of compressor service life
1. Stop the compressor and close the air outlet valve.
2. Switch off the voltage and disconnect the compressor from the mains.
3. Open the condensate drain valve. Depressurize the compressor
4. Shut off and depressurize the part of the air net which is connected to the outlet valve. Disconnect
the compressor from the air net.
5. Disconnect the condensate piping from the local condensate drain system.