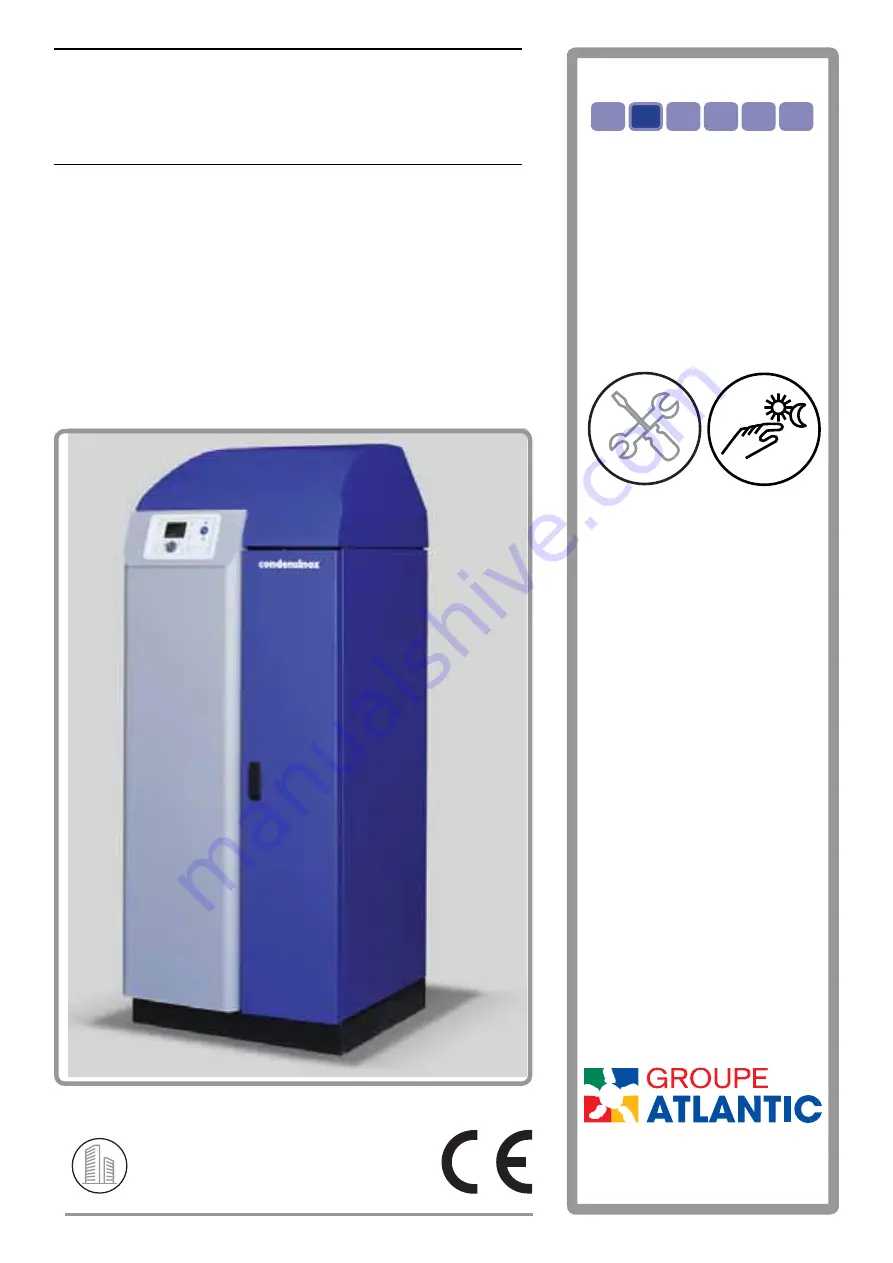
CONDENSINOX
GAS CONDENSING BOILER
40, 60, 80 or 100 kW
with modulating burners
for natural gas and propane gas
FR EN DE ES
IT
NL
Installation,
use and
maintenance
instructions
Document No. 00CNO0183-C / 02/09/15
C
O
L
L
E
C
T
IV
E P
RODUC
T
SITE DE PONT-DE-VAUX
1 route de Fleurville - BP 55
FR - 01190 PONT-DE-VAUX