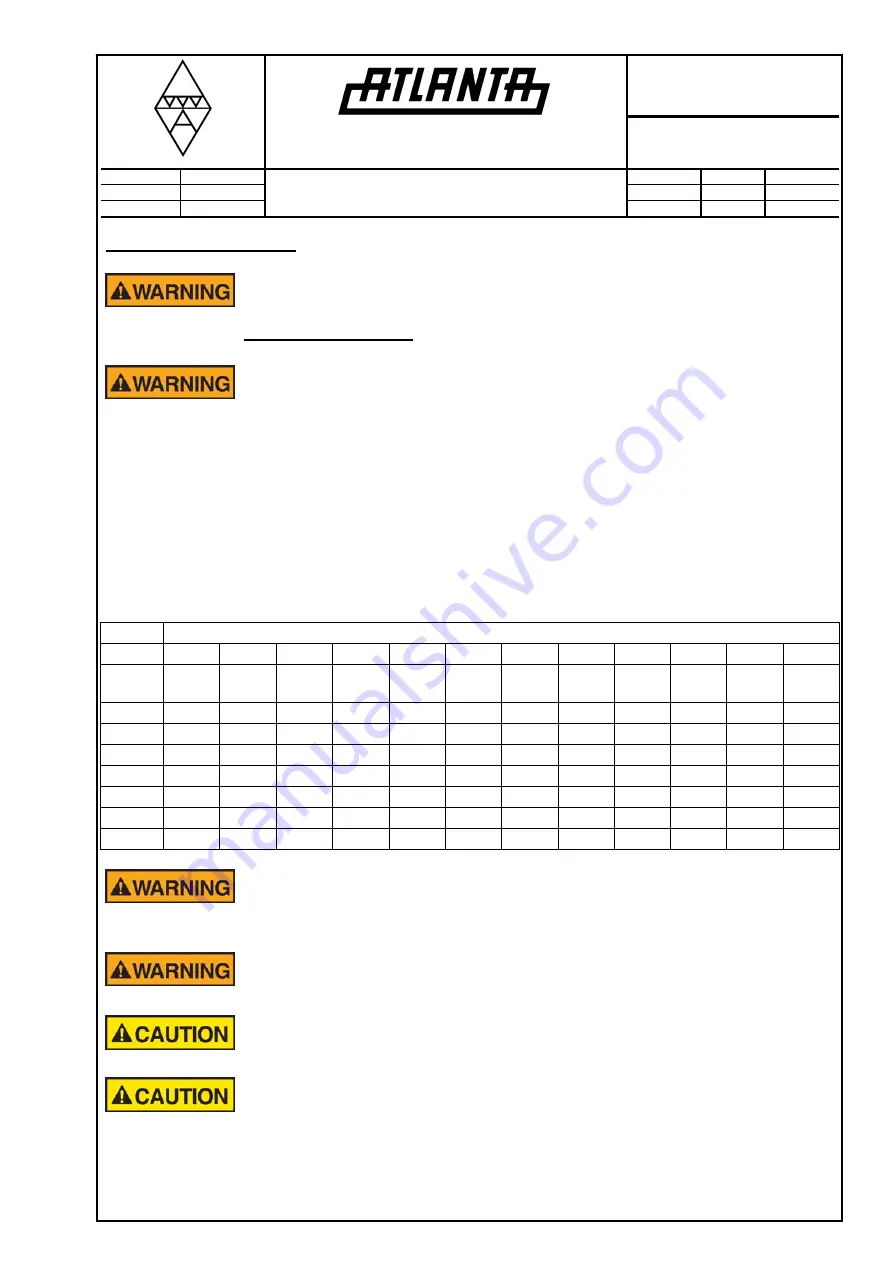
MPZ 001e
Handling, Installation
,
Operation &
Maintenance Instructions
4100-001-06.05
Department TB
Page 7
24
Rev. Index
B
Name 01.06.05
Schell
Date 01.01.09
Rack & Pinion Drives
Released 01.06.05
Lorch
Rack Handling Safety:
The racks must be assembled and installed only by skilled
personnel having the necessary knowhow and experience.
☞
See section “
Qualified Personnel
”
Always wear suitable safety helmet, goggles, protective gloves, and
safety shoes when lifting rack out of its packing and handling it.
A second person should be called in or a crane be used, if the weight exceeds 20 lb. A
second person should also be used if the rack length exceeds 1,000 mm, in order to prevent
injury due to bad posture. The crane must always be operated by a crane driver. The rack
to be carried must be properly secured and, if necessary, the ends of the rack marked in a
clearly visible way.
☺
The table below shows the weight of the individual racks. The lengths are rounded
to the nearest round length.
Mass of the Rack (in pounds)
Module
1 1.5
1.591
2 2.5 3
3.183
4 5 6 8 10
Length
(mm)
200 - - - 1.9 - 2.7 - 6 6.6 10 21 24
250 0.9 1.1 0.9 2.2 2.4 3.5 3.4 6.2 7.6 10.6
24.4 -
500 1.8 2.3 1.7 4.9 4.9 7.1 7 12.5 15 23 50 -
1,000
3.6 4.5 3.4 9.7 9.7 14 14 25 29 55 99 155
1,500
- - - 13.5 - 21 - 37 45 67 - -
2,000 - 9 - 20 20 28 28 50 57 110
197 -
3,000
- - - 30 - 43 - 75 - - - -
When pivoting with a rack in hand, mark the pivoting radius with
a warning sign and warning tape. This area must be blocked
during transport and handling so that no person may be endangered.
Before starting transport of racks, make sure that the travel path is
clean & clear, with ample room to maneuver with good footing.
Avoid twisting and bending while lifting or moving. Lift the racks
comfortably and smoothly, keeping them close to the body.
Before starting transportation of racks, it must be ascertained that
the overall dimensions of the rack permit safe handling. Never allow
the load to obstruct your view!
www.tekmatic.com 815.282.1775 [email protected]