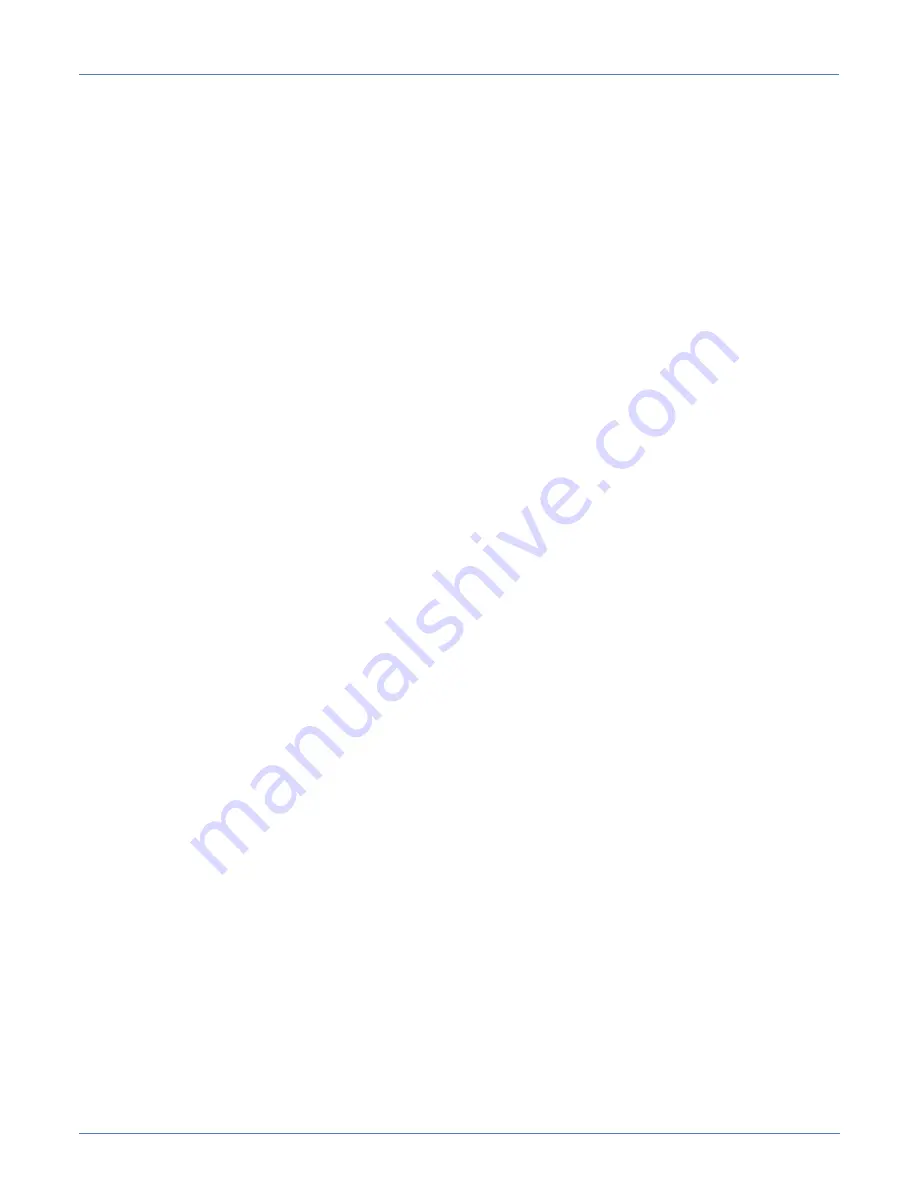
Technical Manual & Parts Lists
8
Repair
Replacement Parts
We cannot accept any liability whatsoever for damage due to the use of parts made by other
manufacturers or due to unqualified repair or modification of the machine.
Repair, Electrical
The power supply must be switched off (master switch off) and secured so that it cannot be switched on
again inadvertently before starting any work on live parts.
Those parts of the machine and plant on which inspection, maintenance or repair work is to be carried
out must be isolated from the power supply, if specified. The isolated parts must first be checked to
determine that they are truly de-energized before being grounded and short-circuited. Adjacent live parts
must also be isolated.
The protective measures implemented (e.g. grounding resistance) must be tested before restarting the
machine after all assembly or repair work on electric parts.
Signal generators (limit switches) and other electrical parts on the safety mechanisms must not be
removed or bypassed. Only use original fuses or circuit overloads with the specified current rating. The
machine must be switched off immediately if a fault develops in the electrical power supply.
The electrical equipment of our machines must be checked at regular intervals and any defects found
must be remedied immediately.
If it is necessary to carry out work on live parts, a second person should be on hand to operate the
emergency OFF switch or master switch with voltage release in the event of an emergency. The working
area should be cordoned off and marked by a warning sign. Only use electrically insulated tools.
Ventilation/Hazardous Gases
It is the end users responsibility to ensure adequate ventilation is provided to exhaust any and all
noxious or hazardous gases that may be present in the working environment.
Hydraulic and Pneumatic Systems
Work on hydraulic or pneumatic equipment shall only be carried out by persons with training,
knowledge and experience of hydraulic systems. Pressure lines shall be depressurized before starting
any repair work.
General Liability
Liability for machine damage and personal injury is extinguished completely if any unauthorized
conversions or modifications are undertaken. The machine must not be modified, enlarged or converted
in any way capable of affecting safety without the manufacturer's prior approval.
Starting Machine Movements
Read the Instruction Manual carefully to establish which keys and functions start machine movements.
Summary of Contents for 4500A
Page 2: ......
Page 102: ...Technical Manual Parts Lists 94 ...
Page 104: ...Technical Manual Parts Lists 96 4500A ...
Page 105: ...Technical Manual Parts Lists 97 1312128 Thread Stand Assembly ...
Page 106: ...Technical Manual Parts Lists 98 1312122 Thread Stand Needles ...
Page 107: ...Technical Manual Parts Lists 99 4500347 Pre Tension Assembly ...
Page 108: ...Technical Manual Parts Lists 100 4500316 Stop Jog Stop Button Assembly ...
Page 109: ...Technical Manual Parts Lists 101 4500345 Console Sub Assembly ...
Page 110: ...Technical Manual Parts Lists 102 4500346 Roll Holder Assembly ...
Page 111: ...Technical Manual Parts Lists 103 4500600 Multi Needle Sew Assembly ...
Page 112: ...Technical Manual Parts Lists 104 4500230 Quilter Guard Assembly LH ...
Page 113: ...Technical Manual Parts Lists 105 4500233 Quilter Guard Assembly RH ...
Page 114: ...Technical Manual Parts Lists 106 4500313 Center Guide Assembly ...
Page 115: ...Technical Manual Parts Lists 107 4500473 Slack Arm Assembly ...
Page 116: ...Technical Manual Parts Lists 108 4500813 Tension Assembly ...
Page 117: ...Technical Manual Parts Lists 109 4500500 Multi Needle Quilter Assembly 1 of 5 ...
Page 118: ...Technical Manual Parts Lists 110 4500500 Multi Needle Quilter Assembly 2 of 5 ...
Page 119: ...Technical Manual Parts Lists 111 4500500 Multi Needle Quilter Assembly 3 of 5 ...
Page 120: ...Technical Manual Parts Lists 112 4500500 Multi Needle Quilter Assembly 4 of 5 ...
Page 121: ...Technical Manual Parts Lists 113 4500500 Multi Needle Quilter Assembly 5 of 5 ...
Page 122: ...Technical Manual Parts Lists 114 4500275 Needle Bar Guide Assembly ...
Page 123: ...Technical Manual Parts Lists 115 4500276 Middle Support Assembly ...
Page 124: ...Technical Manual Parts Lists 116 4500277 Left Side Plate Assembly ...
Page 125: ...Technical Manual Parts Lists 117 4500278 Right Side Plate Assembly ...
Page 126: ...Technical Manual Parts Lists 118 4500279 Looper Rod Assembly ...
Page 127: ...Technical Manual Parts Lists 119 4500280 Spreader Drive Rod Assembly ...
Page 128: ...Technical Manual Parts Lists 120 4500281 Looper Drive Rod Assembly ...
Page 129: ...Technical Manual Parts Lists 121 4500518 Looper Take Up Assembly ...
Page 130: ...Technical Manual Parts Lists 122 4500534 Looper Holder Assembly ...
Page 131: ...Technical Manual Parts Lists 123 4500380 Cable Support Assembly ...
Page 132: ...Technical Manual Parts Lists 124 4500410 Pattern Sew Assembly ...
Page 133: ...Technical Manual Parts Lists 125 4500420 Pattern Sew Sub Assembly ...
Page 134: ...Technical Manual Parts Lists 126 4500138 Control Box Assembly ...
Page 135: ...Technical Manual Parts Lists 127 4500180 Regulator Panel Assembly ...
Page 136: ...Technical Manual Parts Lists 128 4500407 Rear Clamp Plate Assembly ...
Page 137: ...Technical Manual Parts Lists 129 4500415 Thread Stand Assembly ...
Page 138: ...Technical Manual Parts Lists 130 4500460 Puller Assembly ...
Page 139: ...Technical Manual Parts Lists 131 4500490 Idler Roller Assembly ...
Page 140: ...Technical Manual Parts Lists 132 4500496 Idler Sprocket Assembly ...
Page 141: ...Technical Manual Parts Lists 133 4500540 Idler Roller Assembly ...
Page 142: ...Technical Manual Parts Lists 134 4500421 Pattern Sew Assembly ...
Page 143: ...Technical Manual Parts Lists 135 4500045 Drive Pulley Assembly ...
Page 144: ...Technical Manual Parts Lists 136 4500053 Idler Pulley Assembly ...
Page 145: ...Technical Manual Parts Lists 137 4500418 Pattern Sew Head Assembly ...
Page 146: ...Technical Manual Parts Lists 138 4500068 Sew Head Motor Assembly ...
Page 147: ...Technical Manual Parts Lists 139 4500105 Sew Head Assembly ...
Page 148: ...Technical Manual Parts Lists 140 4500650 Border Rewinder Assembly ...
Page 149: ...Technical Manual Parts Lists 141 1961 320M Rewind Assembly ...
Page 150: ...Technical Manual Parts Lists 142 4500106 Tension Rod Assembly ...
Page 151: ...Technical Manual Parts Lists 143 4500910 Control Cabinet Assembly ...
Page 152: ...Technical Manual Parts Lists 144 1388986 Touchscreen Assembly ...
Page 153: ...Technical Manual Parts Lists 145 4500902 Backplane Back Side Assembly ...
Page 154: ...Technical Manual Parts Lists 146 4500904 Backplane Front Side Assembly ...
Page 155: ...Technical Manual Parts Lists 147 4500A PD Pneumatic Diagram ...
Page 156: ...Technical Manual Parts Lists 148 4500 WD3 Wiring Diagram Pattern Sew PLC I O ...
Page 157: ...Technical Manual Parts Lists 149 4500 WD4 Wiring Diagram Main Cabinet ...
Page 158: ...Technical Manual Parts Lists 150 4500 WD5 Wiring Diagram Pattern Sew SOL ...
Page 159: ...Technical Manual Parts Lists 151 4500 WD6 Wiring Diagram Pattern Sew Thread Breaks ...
Page 160: ...Technical Manual Parts Lists 152 4500 WD7 Wiring Diagram Sew Motors ...
Page 161: ...Technical Manual Parts Lists 153 4500 WD8 Wiring Diagram Encoder Remote ...
Page 162: ...Technical Manual Parts Lists 154 4500 WD9 Wiring Diagram Main Power Servos ...
Page 165: ......