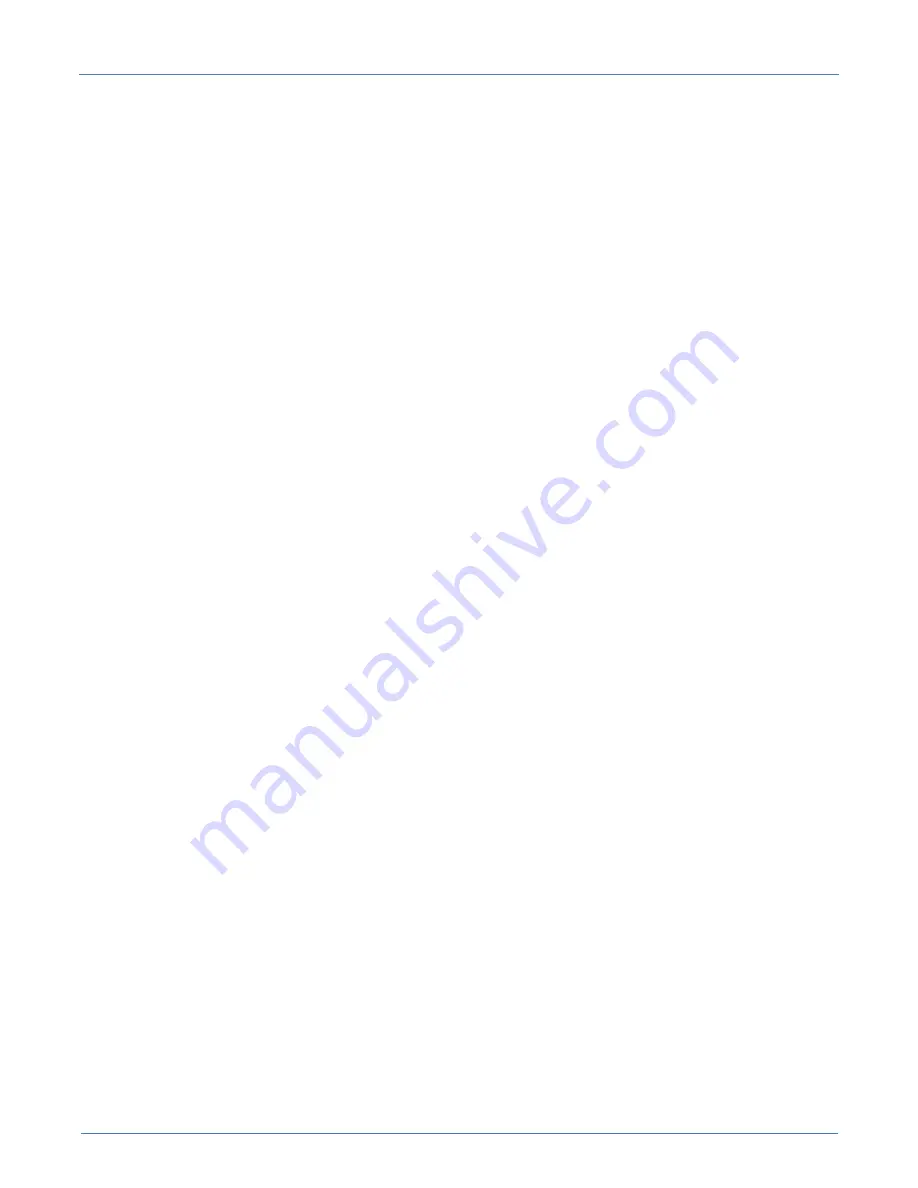
Technical Manual & Parts Lists
9
A Word to the End User
The end user has sole responsibility to enforce the use of safety procedures and guards on the machine.
Any other safety devices or procedures due to local regulations should be should be retrofitted in
accordance to these regulations and/or the EC Directive on the safety of machines.
Operator’s position must always be readily accessible. Escape routes must always be kept clear and
safety areas should be identified.
Safety Precautions
Safety should be a constant concern for everyone. Always be careful when working with this equipment.
While normal safety precautions were taken in the design and manufacture of this equipment, there are
some potential safety hazards.
Everyone involved with the operation and maintenance of this equipment should read and follow
the instructions in this manual.
Operate the equipment only as stated in this manual. Incorrect use could cause damage to the
equipment or personal injury.
It is the owner’s responsibility to make certain that the operator reads and understands this
manual before operating this equipment. It is also the owner’s responsibility to make certain that
the operator is a qualified and physically able individual, properly trained in the operation of this
equipment.
Specific safety warning decals are located on the equipment near the immediate areas of potential
hazards. These decals should not be removed or obliterated. Replace them if they become non-readable.
•
ALWAYS keep safety shields and covers in place, except for servicing.
•
ALWAYS maintain a safe distance from people when operating.
•
ALWAYS operate equipment in daylight or with adequate working lights.
•
Follow daily and weekly checklists, making sure hoses are tightly secured and bolts are
tightened.
•
ALWAYS watch and avoid holes or deep depressions.
•
ALWAYS wear adequate eye protection when servicing the hydraulic system and battery.
•
NEVER operate a poorly maintained machine.
•
NEVER allow persons to operate this machine without proper instruction.
•
NEVER put hands or feet under any part of the machine while it is running.
•
NEVER attempt to make any adjustments or repairs to the machine while running. Repairs or
maintenance should be performed by trained personnel only.
•
NEVER work under the machine unless it is safely supported with stands, blocks or a hoist and
blocks.
•
NEVER touch hot parts of machine.
Summary of Contents for 3304A
Page 2: ......
Page 15: ...Technical Manual Parts Lists 11 ...
Page 17: ...Technical Manual Parts Lists 13 ...
Page 19: ...Technical Manual Parts Lists 15 ...
Page 23: ...Technical Manual Parts Lists 19 3304A PD PNEUMATIC DIAGRAM AAC Drawing Number 125975C Rev 0 ...