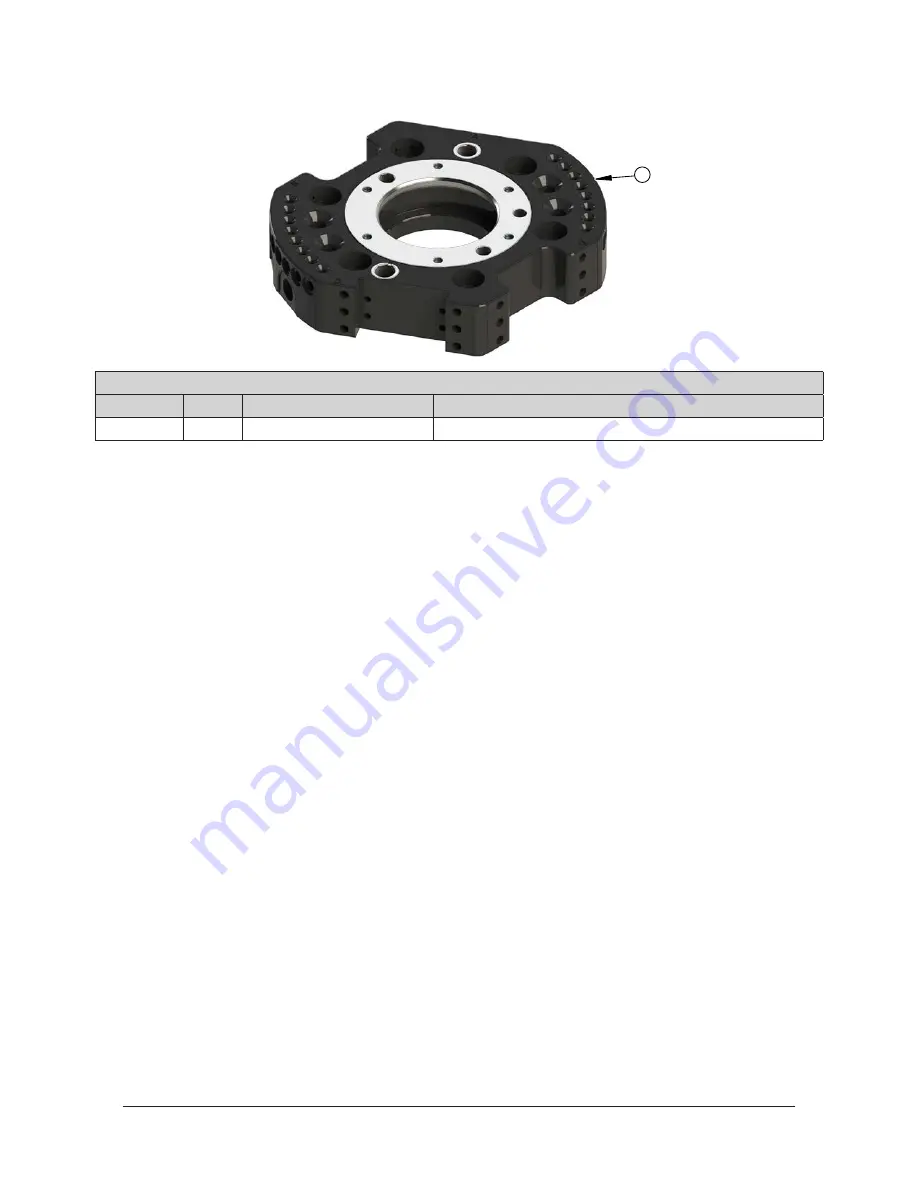
Manual, Tool Changer, QC‑50
Document #9620‑20‑B‑50 Tool Changer‑04
Pinnacle Park • 1031 Goodworth Drive • Apex, NC 27539 • Tel: 919.772.0115 • Fax: 919.772.8259 •
B-31
6.2 QC-50 Tool Plate
1
Table 5.3—Tool Plate
Item No.
Qty
Part Number
Description
1
1
9120-050BT-0-0-0-0-E
QC-50 Tool Assembly, BSPP and M5