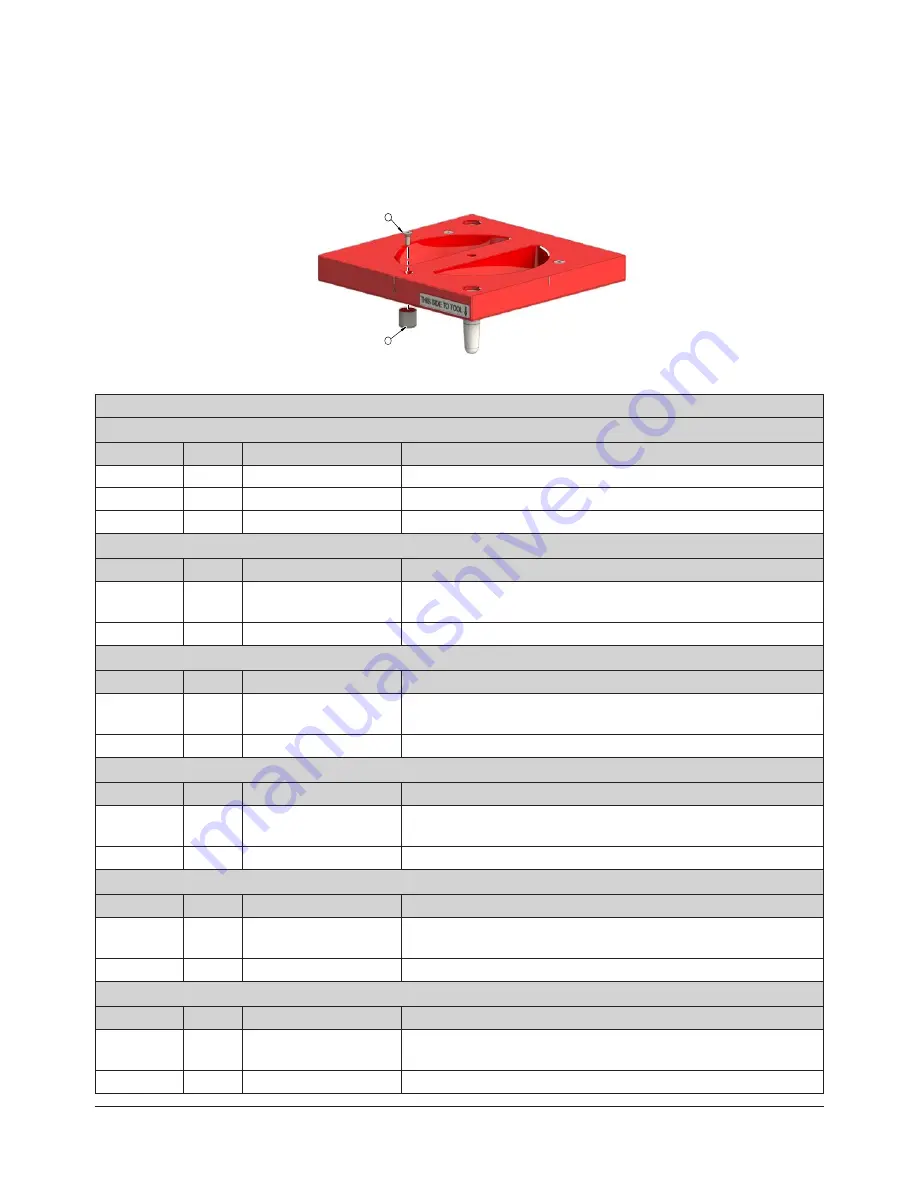
Manual, Robotic Tool Changer Teaching Aids
Document #9610-20-1419-07
Pinnacle Park • 1041 Goodworth Drive • Apex, NC 27539 USA • Tel: +1.919.772.0115 • Fax: +1.919.772.8259 • www.ati-ia.com
16
6. Serviceable Parts
6.1 Tool Teaching Aid Serviceable Parts
Figure 6.1—Tool Teaching Aid Plate (QC-210 Shown)
2
1
Table 6.1—Tool Teaching Aid Plate
QC-40
ITEM NO.
QTY
PART NUMBER
DESCRIPTION
1
4
3710-20-3484
Magnet, 0.625’’ x .18’’ K&J Magnets MMS-H-A
2
2
3500-1010050-21
#4-40 x 1/2 Stainless Steel Socket Head Cap Screw
3
2
3500-1010062-1
#4-40 x 5/8 Socket Head Cap Screw
QC-110, QC-210
ITEM NO.
QTY
PART NUMBER
DESCRIPTION
1
3
3710-20-3355
Encased Alinco 5 Magnet 1/2” Dia, 1/2” Thick, 6-32 Hole, 1.4
Pull lbs
2
3
3500-1215037-21
#6-32 x 3/8” Stainless Steel Flat Head Socket Cap Screw
QC-160, QC-213
ITEM NO.
QTY
PART NUMBER
DESCRIPTION
1
4
3710-20-3355
Encased Alinco 5 Magnet 1/2” Dia, 1/2” Thick, 6-32 Hole, 1.4
Pull lbs
2
4
3500-1215037-21
#6-32 x 3/8” Stainless Steel Flat Head Socket Cap Screw
QC- 310
ITEM NO.
QTY
PART NUMBER
DESCRIPTION
1
6
3710-20-3355
Encased Alinco 5 Magnet 1/2” Dia, 1/2” Thick, 6-32 Hole, 1.4
Pull lbs
2
6
3500-1215037-21
#6-32 x 3/8” Stainless Steel Flat Head Socket Cap Screw
QC-510
ITEM NO.
QTY
PART NUMBER
DESCRIPTION
1
8
3710-20-3355
Encased Alinco 5 Magnet 1/2” Dia, 1/2” Thick, 6-32 Hole, 1.4
Pull lbs
2
8
3500-1215037-21
#6-32 x 3/8” Stainless Steel Flat Head Socket Cap Screw
QC-1210
ITEM NO.
QTY
PART NUMBER
DESCRIPTION
1
9
3710-20-3355
Encased Alinco 5 Magnet 1/2” Dia, 1/2” Thick, 6-32 Hole, 1.4
Pull lbs
2
9
3500-1215037-21
#6-32 x 3/8” Stainless Steel Flat Head Socket Cap Screw