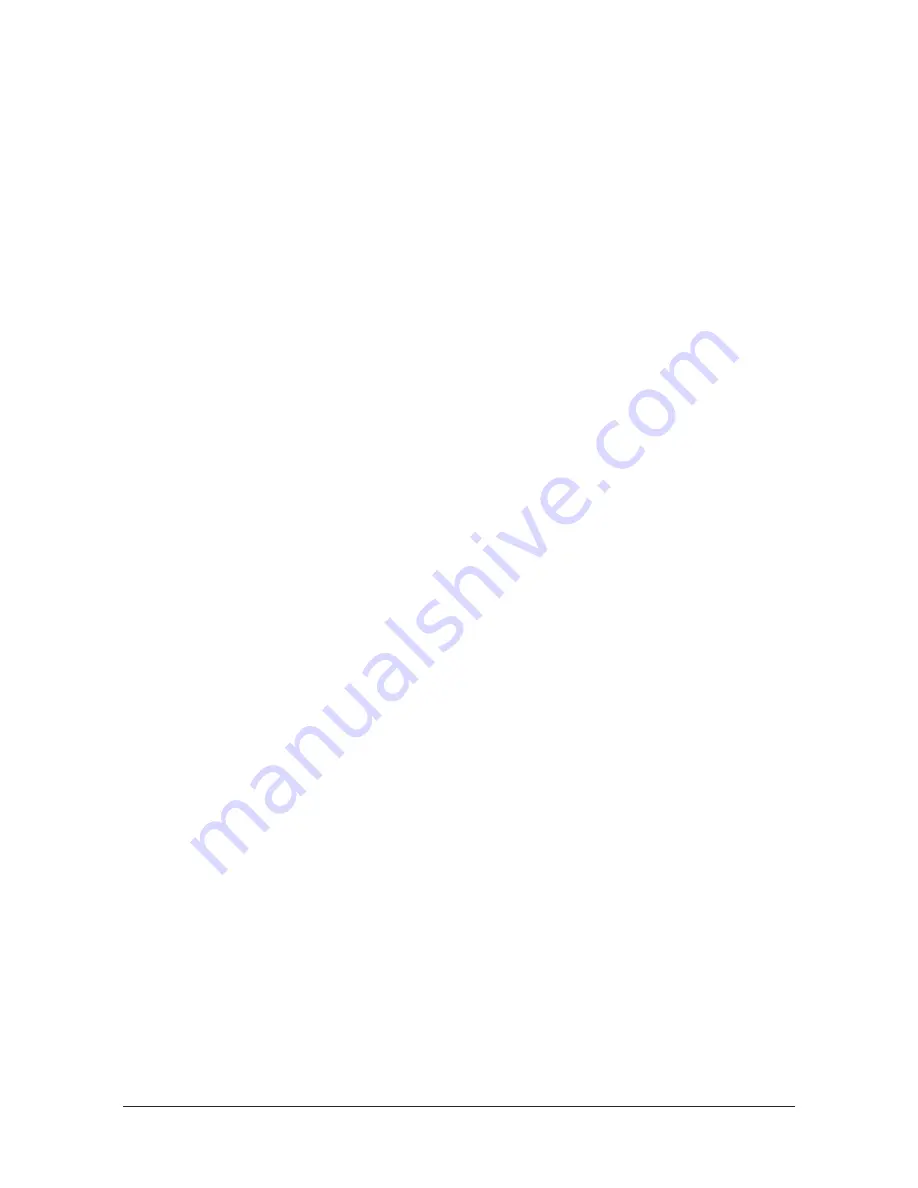
Manual, Control Module, PROFINET, DL12
Document #9620-20-C-DL12-06
Pinnacle Park • 1031 Goodworth Drive • Apex, NC 27539 • Tel: 919.772.0115 • Fax: 919.772.8259 •
C-5
C. Control and Signal Modules
DL12—PROFINET
®
Control/Signal Module
1. Product Overview
The modules enable the customer to control and communicate with the Tool Changer through a network using a
PROFINET interface. A PROFINET node is established on the Master module, but not on the Tool. Control of the
Tool Changer is realized through the Master node along with the reporting of various Tool Changer I/O. The Tool
module supports Tool‑ID reported through the Master module and functions as a pass‑through for PROFINET
network and power to downstream equipment.
The Master module is used in combination with a valve adapter with dual double solenoid valves, for Latch/
Unlatch control of the Tool Changer. When used in combination with a dual double solenoid valve adapter, the
modules achieves PLd safety reliability in accordance with ISO standard 13849‑1. The user is required to provide
a pneumatic supply source to the valve adapter. Refer to the appropriate valve adapter or Tool Changer manual for
requirements.
In addition to supporting the standard Tool Changer input signals (Locked, Unlocked, etc.) the modules also
support advanced diagnostic and fault reporting. Refer to
A minifast connector is provided on the Master and Tool modules for interfacing with power. The power source for
input and output power must be capable of outputting an operating voltage (reverse polarity protected, regulated)
of 20.4 to 28.8 VDC. A M12 D‑coded connector is provided on the Master and Tool modules for interfacing with
PROFINET. When the Tool Changer is coupled, the Master and Tool modules pass signals via spring loaded
pin blocks. Flexible V‑ring seals surround the pin blocks and are water resistant but not water proof. Refer to
To avoid unintentional Tool release, the power for the Unlatch valve is routed through a safety switch connector. A
safety switch must be connected to support this function. Refer to
.
1.1 Master Module
The module has the following connectors:
•
(1) integrated 4‑pin valve signal pin block for the Latch and Unlatch signals to the solenoid valves
•
(4) 3‑pin female M8 RTL sensors (R1 and R2), Lock (L), and Unlock (U) sensor connectors
•
(1) 3‑pin female M8 valve adapter proximity sensor connector
•
(1) 4‑pin female M8 valve adapter pressure sensor connector
•
(1) 4‑pin female M12 D‑coded PROFINET connector
•
(1) 4‑pin male minifast power connector
The module also incorporates ATI’s exclusive Arc Prevention Circuit which extends the life of electrical
power contacts by eliminating arcing caused by inductive loads and high inrush current during coupling/
uncoupling. Refer to
Section 2.2—Arc Prevention Circuit.
The module provides status LED’s to visually indicate its operation. A reset button provides the ability to
return to default settings. Refer to
Section 2.1.3—System Failure and Bus Failure LEDs
and
Ethernet 1 and Ethernet 2 LEDs
An electrical interface is provided on the module for support of two integrated double solenoid valves (DC
Voltage, sourcing type). The integrated valve is supplied from ATI as part of a dual double solenoid valve
adapter. Refer to the Valve Adapter Manual for more information (9620‑20‑C‑Jxx Valve Adapters with Dual
Double Solenoid, Valve Pass Through, Proximity and Pressure Sensors). Electrical interface drawings and
connector details are provided in drawings in
PROFINET requires a FE ground, the Master module provides a M8 threaded hole for FE ground terminal
that is passes FE ground to the Tool Module through the 7‑Pin contact block. The M8 set screw must be
removed prior to FE ground connection.