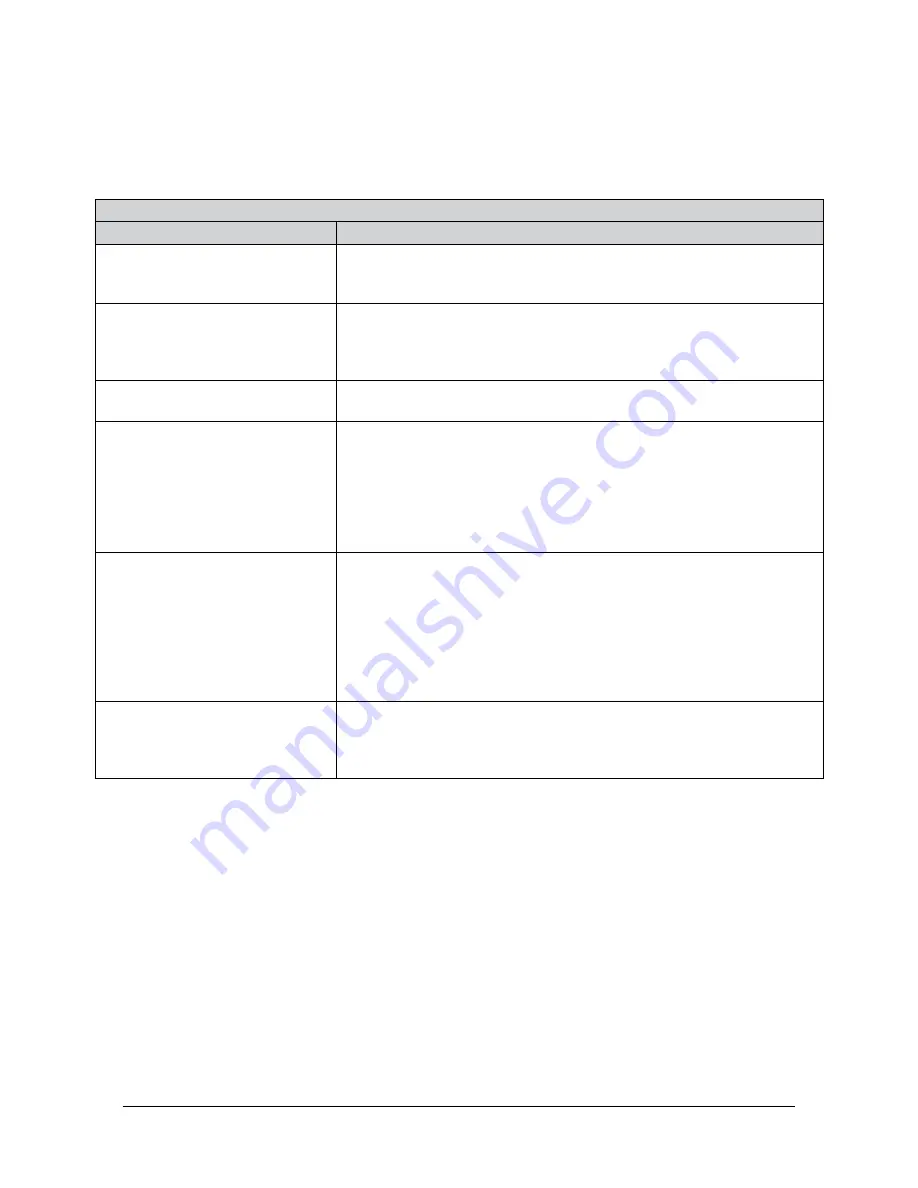
Manual, F/T Sensor, Ethernet Axia
Document #9610-05-Ethernet Axia-09
Pinnacle Park • 1031 Goodworth Drive • Apex, NC 27539 • Tel:+1 919.772.0115 • Fax:+1 919.772.8259 •
87
14.5 Errors with Force and Torque Readings
Incorrect data from the sensor’s strain gages can cause errors in force/torque readings. Listed in the
following table are the basic conditions of incorrect data. Use this table to troubleshoot a problem. In most
cases, problems can be better identified while looking at the raw strain gage data, displayed on the Snapshot
Section 6.2—Snapshot Page (rundata.htm)
for more details.
Table 14.5—Errors with Force and Torque Readings
Symptom
Cause and Resolution
The sensor is not streaming
measurement data to the
customer devices.
Verify the sensor is correctly installed. Ensure the robot mounting and
tool adapter plates are installed on the proper side of the sensor. Refer
to
for more information.
Either the “Force/Torque Out of
Range” or the “Gage Out Range”
bit is set (refer to
),
The sensor is reporting that it is no longer within the calibrated range
and may experience inaccuracy and reduced life.
The “Broken Gage Bit” is set (refer
to
).
An electrical failure has potentially occurred inside the sensor. The
sensor must be returned to ATI for diagnosis.
Noise
Jumps in force torque data readings (with the sensor unloaded) greater
than 0.05% of full scale counts is abnormal. Noise can be caused by
mechanical vibrations and electrical disturbances, possibly from a poor
ground. Noise can also indicate component failure within the system.
Make sure that the DC supply voltage for the Axia sensor has little
to no noise superimposed. The sensor should be grounded through
installation construction. See
.
Drift
After a load is removed or applied, the raw gage reading does not
stabilize but continues to increase or decrease. A shift in the raw gage
reading is observed more easily in the resolved data mode using the
bias command. Some drift from a change in temperature or mechanical
coupling is normal. Mechanical coupling occurs when a tool plate
contacts the sensor body, for example, debris between the tool adapter
plate and the sensor body or in applications such as hoses and wires
attached to a tool.
Hysteresis
When the sensor is loaded and then unloaded, gage readings do not
return quickly and completely to their original readings. Hysteresis is
caused by mechanical coupling (explained in Drift section) or internal
failure.
14.6 Reducing Noise
14.6.1 Mechanical Vibration
In many cases, perceived noise is actually a real fluctuation of force and/or torque, caused by
vibrations in the tooling or the robot arm. The Ethernet Axia sensor offers digital low-pass filters
that can dampen frequencies above a certain threshold. If digital low-pass filters are insufficient, a
digital filter may be added to the application software.
14.6.2 Electrical Interference
To reduce the effects of electrical noise on the sensor, do the following:
•
If interference by motors or other noise-generating equipment is observed, check the sensor’s
ground connections.
•
If sufficient grounding is not possible or does not reduce noise, consider using the sensor’s
digital low-pass filters.
•
Verify the power supply is Class 1, which has an earth ground connection.