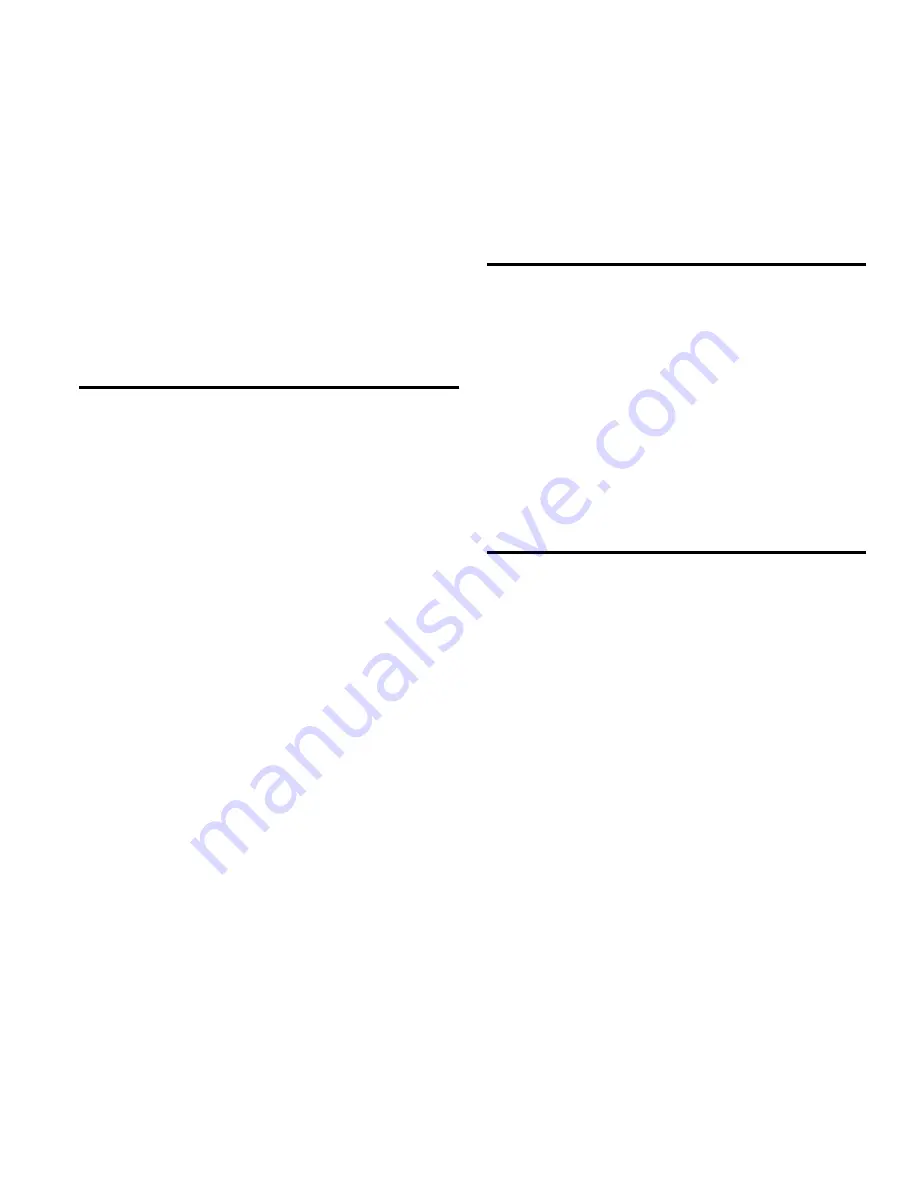
OPTIONAL FEATURES
HeatNet Control V3 2.x
If a pump fails (flow switch required), or the flow switch
fails, the boiler will cycle the start condition every 10 minutes
in an attempt get the boiler restarted.
If the damper fails to open and never closes its proof switch, a
retry algorithm will attempt a retry. Every 10 minutes the
damper relay will cycle and try to open the damper again.
If the H-Net control closes the last interlock string connected
to the ignition control and the ignition control never closes its
Blower Relay, the H-Net control will wait 2 minutes. The H-
Net control will then retry for the duration of the local pump
post purge time and then retry the ignition sequence. During
this time “retry strt” will be displayed in the status screen.
After (5) attempts the H-Net control will lock out and display
call service.
Blower Protection
With the use of the Ametek blower the HeatNet control has
assumed many of the responsibilities that the Variable
Frequency Drive provided. Some of these include
Acceleration, Deceleration, Braking, and Soft Start.
The most sensitive of these (4) functions is the Soft Start. The
Soft Start overcomes the motor‟s attempt to run at a high rate
of speed before overcoming inertia. In the larger Ametek
blowers a higher starting torque is required to break the inertia
of the Ametek‟s flywheel effect. If the Ametek motor cannot
transform its electrical energy into mechanical energy fast
enough, (due to this inertia) a high input current to the motor
will result. The Ametek motor would then shut down and lock
out due to this current. The only way to reset the Ametek
blower due to the over current condition is to power cycle the
boiler.
Also, due to the nature of the inverter circuit that is used to
change the AC line input to a DC voltage to power the motor,
a sizable bank of capacitors is used. When the blower is first
powered up, these capacitors are empty and develop a large
inrush of current.
In order to provide a means of controlling these situations and
preventing downtime, the HeatNet control allows a relay to
control the power fed to the blower. This is done by wiring
the 120 VAC power to the J13A.1 Stage 4 relay contact using
black 18 gauge MTR/TEW wire. Then wiring (same wire
type) from J13A.2 to the Ametek blower contactor‟s enable
input. This allows the HeatNet control firmware to control
power to the blower by switching the contactor ON or OFF.
The reasons for this are as follows:
1.
The Stage 4 relay has been allocated to help bring the
power up in steps. These steps are used to minimize
inrush currents by engaging the blower‟s contactor (7)
seconds after the main power has been applied.
2.
In the event a blower lockout has been determined, a
(10) minute retry cycle, (3) times will occur. At the time
the blower has been detected as locked out, the retry
cycle will start. The Stage 4 relay will be de-energized
for (8) minutes. Then the Stage 4 relay will be energized
for (2) minutes. This will effectively power cycle just
the blower. The call for heat will then be allowed in an
attempt to start the boiler. After (3) failed retry attempts,
the boiler will lock out.
Communications
The H-Net control has the ability to communicate using the
MODBUS protocol with a building management system.
Most registers and functions are available for MODBUS
access. Access is allowed using the RS485 MODBUS PORT
connecter on the communication board. Version 2.x Control
has these connections integrated on the main board.
An optional BACnet or LonWorks bridge module can be used
to connect the MODBUS network to a BACnet or LonWorks
network. See Method 5 control.
Failsafe Modes
FAILSAFE MODES have been added to help protect systems
from loss of heat conditions. When using one of these modes
ensure that you connect any DAMPER control, or system
pump control to safely allow operation
with the assumption
that the MASTER boiler or BMS system is DOWN.
FAILSAFE REQUIREMENTS:
1.
Since the Member boiler that will be assigned the
Failsafe duty will always turn the system pump ON, this
boiler should not be used for DHW heating. If the Master
controls the system pump, then the Failsafe Member
boiler would need to control the system pump in parallel
with the Master boiler. Wire the System Pump contacts in
parallel with the Master.
2.
If the combustion air damper is used as a common system
damper, the Failsafe boiler should be wired to control the
damper in parallel with the Master boiler.
3.
The Failsafe boiler must have the LOCAL SETPOINT
set to the same setpoint temperature as the Master
boiler‟s SYSTEM SETPOINT.
Be aware that the boiler may start without a call-for-heat in
the FAILSAFE MODES. FAILSAFE MODES can be
accessed through the:
35
Summary of Contents for KN-10
Page 107: ...107 ...