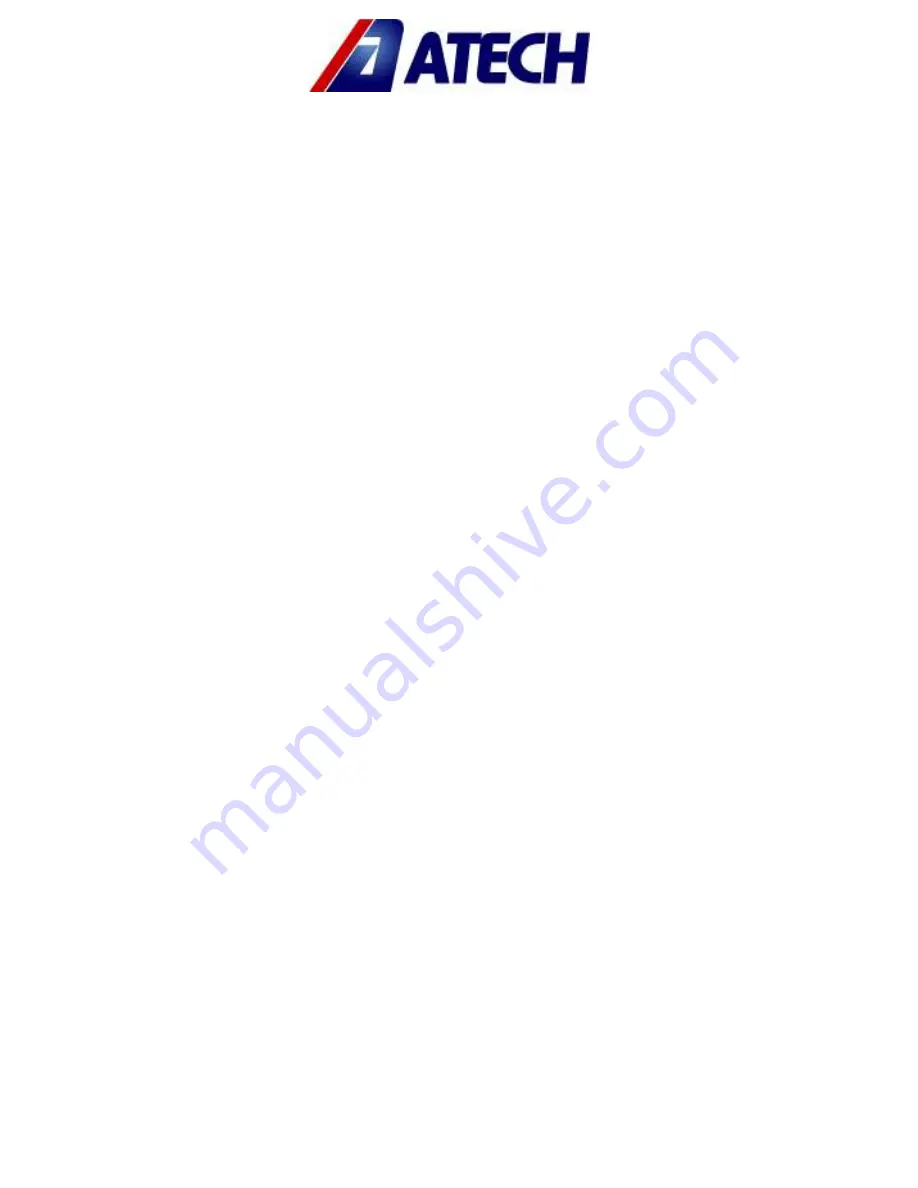
16
Operating and Safety Instructions
8.1.2.
The machine is equipped with vertical & horizontal clamps. These clamps can be
adjusted easily according to the material.
8.1.3.
Avoid randomly pressing the buttons on the panel. If you feel danger during the
cutting operation, push the emergency stop button immediately, which will terminate the
operation.
8.1.4.
Close the front cover on the main frame and the control panel, and lock it with its
key. See Illustration - 1 (For safety reasons, the motor will not start unless the main frame
front cover is closed)
NOTE: The main frame front cover and the rear panel cover can be open only during
maintenance and cleaning of the machine. During this work switch the MAIN SWITCH to
“0” before opening the cover.
8.1.5.
Ensure clamping of the work piece by the vertical & horizontal pneumatic clamps
pressing the clamp button on the machine
8.1.6.
Start the machine by pressing the Motor Start Button.
8.1.7.
Press the button for rising the saw blade to move the saw blade.
8.1.8.
The circular saw blade will rise and cut the work piece, and will move down
automatically after cutting the work piece.
8.1.9.
Press the clamp button to release the work piece, and take it out.