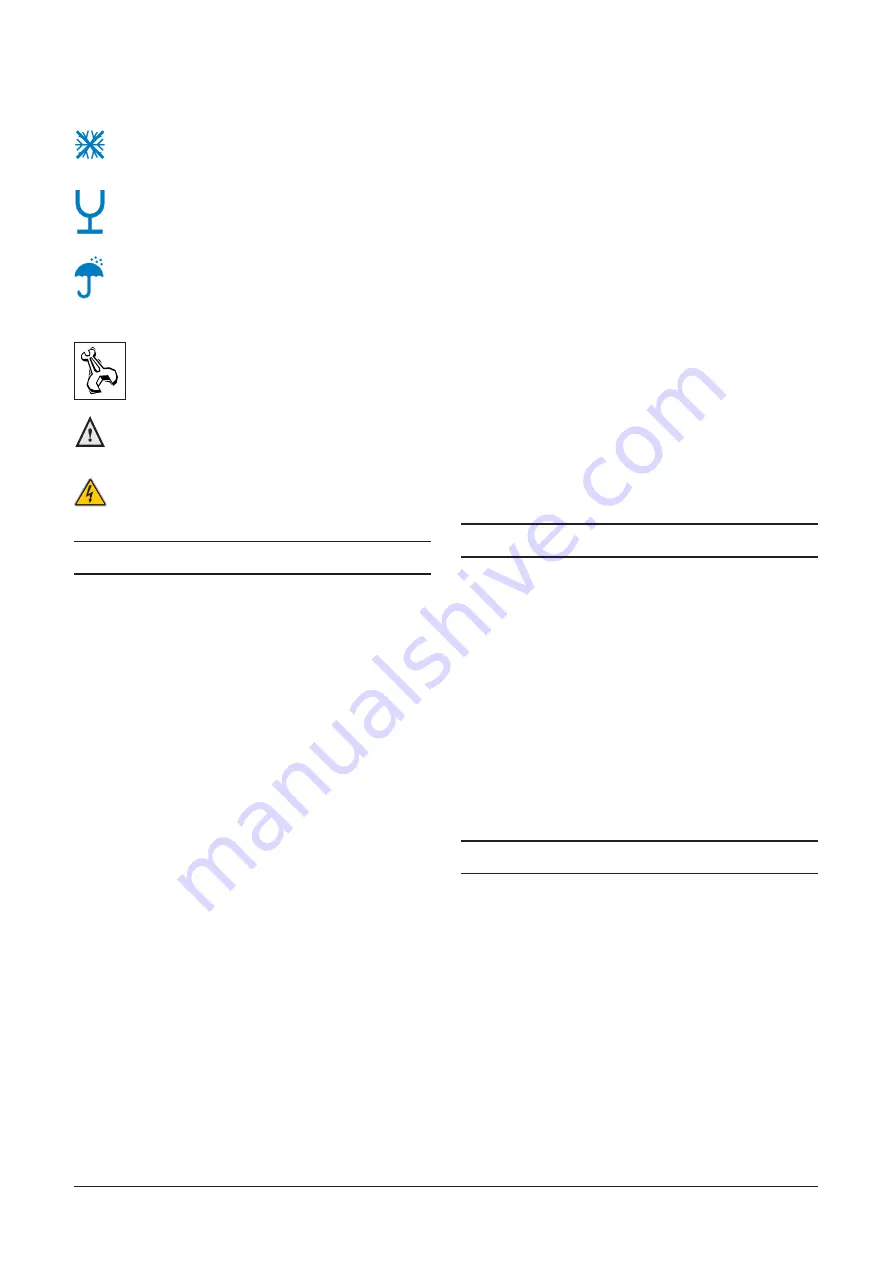
Installation instructions S-HR series page 5
The following (safety) symbols may be encountered in
these installation instructions and on the unit:
This symbol indicates that the unit must be
stored away from frost.
This symbol indicates that the packaging
and/or contents can be damaged as a result of
insufficient care taken during transport.
This symbol indicates that, whilst still in its
packaging, the unit must be protected from
weather conditions during transport and
storage.
KEY-symbol. This symbol indicates that
assembly or dismantling, must be carried
out.
ATTENTION symbol. This symbol indicates
that extra attention must be paid in
connection with a particular operation.
Danger: High Voltage!
3
Description of the appliance
The ATAG Blauwe Engel
S-HR boiler is a room sealed,
condensing and modulating central heating boiler, with
or without an integrated hot water facility.
The built-in fan sucks the combustion air from outside
and provides full premixing of the gas and air. The gas
mixture is guided through the ceramic burner which is
fitted above the heat exchanger. As a result of the small
flame height a compact construction is possible. The
combustion gasses are exhausted after passing
through the stainless steel heat exchanger. The formed
condensate water is discharged through the waste trap.
The boiler has been tested according to valid CE*
standards and has a CE* certificate and SEDBUK A-
rating.
The operating efficiency of the boiler is higher than 98%
(on upper value Hs). As a result of its compact
construction the radiation, convection and stand by
losses are very low. The emission of damaging
substances is far below the standard set for equipment
with the gas quality-control label for clean combustion.
The boiler is provided with an automatic venting program.
In case of a recently topped up or filled up installation this
program takes care of the removal of any present air in the
boiler. In this case the control will check the water
pressure and if it is to low, will report this on the display.
The boiler anticipates the heat requirement of the central
heating installation or the hot water supply. As a result the
boiler will adjust its capacity to the installation and will
switch on less often, which means that the boiler will
operate longer and at a low level. It is possible that the boiler
will only have to switch on once an hour. In this case the
aim is to obtain maximum comfort and efficiency.
In order to be able to anticipate installation heat
emissions the boiler has been fitted with a proportional
gradient control system. After the boiler goes into
operation this control provides a uniform increase of
power, instead of immediately burning at full power.
When the installation does require full power the control
will adjust as required. By this means a uniform increase
of the water temperature is effected.
If an outside sensor is connected, the control will
operate weather-dependent. This means that the
control measures the outside temperature and the flow
water temperature. On the basis of this data the control
calculates the optimal flow water temperature in the
installation.
The S-HR-T combination boiler provides a hot water
supply by means of a high output cylinder fitted on the
right hand side of the boiler. An adjustable thermostatic
mixing valve is fitted which provides a constant hot water
temperature (60°C factory setting).
4
Scope of the supply
The boiler is supplied ready for use. The supply kit is
composed as follows:
-
Boiler with casing;
-
Automatic vent (inside the boiler);
-
Safety valve (inside the boiler);
-
Suspension bracket
-
Filling and draining valve with T-piece;
-
Fixing material consisting of plugs and screws;
-
Template on the package wrapper;
-
Installation instructions
-
Operating manual;
-
Warranty card;
-
Benchmark logbook.
5
Mounting of the boiler
The boiler can be mounted practically to any wall with the
suspension bracket and the enclosed fixing equipment.
The wall must be flat and of sufficient strength in order to
be able to carry the boiler weight.
Above the boiler there must be at least 250 mm working
space in order to be able to fit a coaxial flue system or a
twin supply. On the left side of the boiler at least 50 mm
and on the right side 10 mm must be reserved in
connection with fitting or removing of the casing. The
location of the boiler can be determined by using the
template located inside the boiler packaging.
Summary of Contents for Blauwe Engel S-HR 15
Page 2: ......
Page 15: ...Installation instructions S HR series page 15 electrical connecting diagram figure 11...
Page 31: ...Installation instructions S HR series page 31 19 CE Certificate United Kingdom...
Page 32: ...Installation instructions S HR series page 32 20 CE Certificate Ireland...
Page 33: ......
Page 34: ......
Page 35: ......