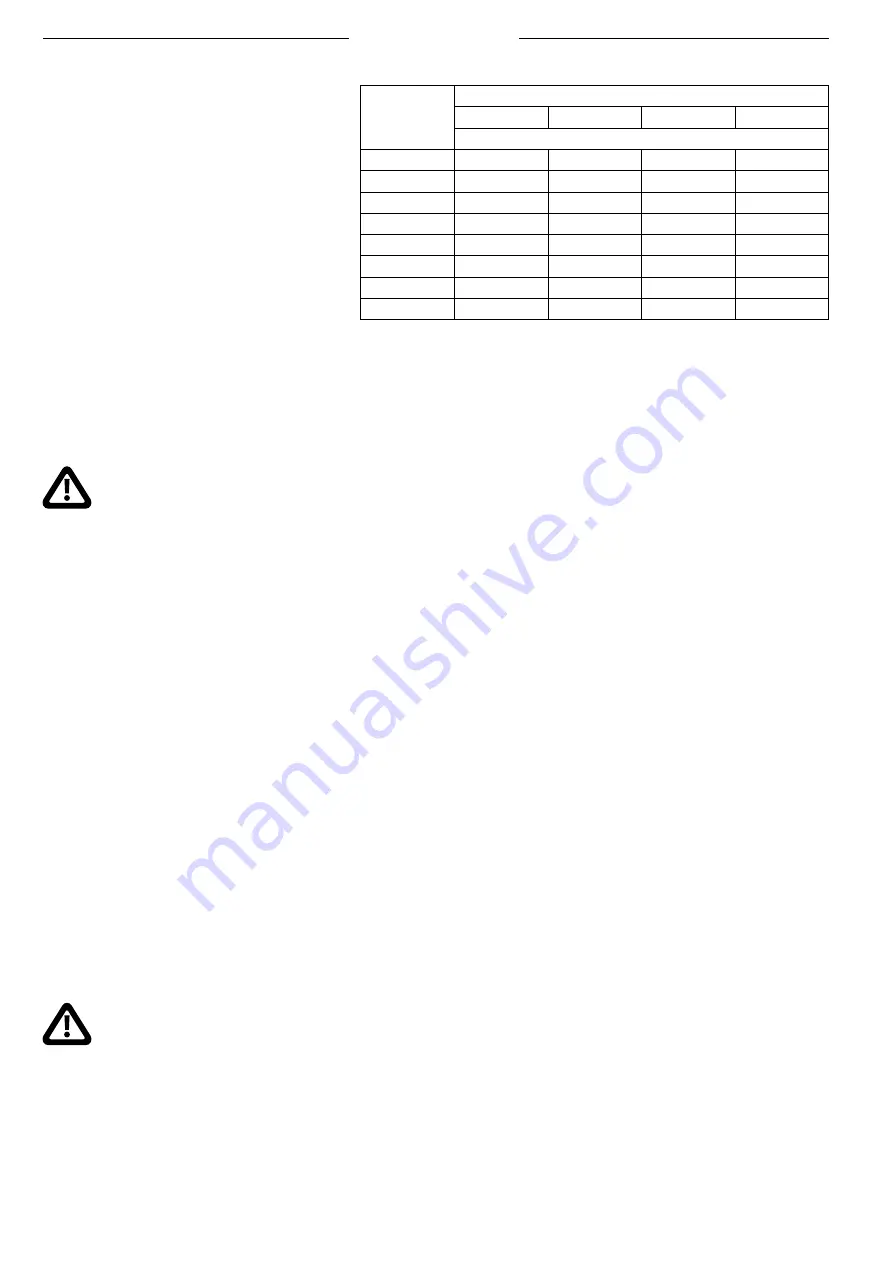
13
INSTALLATION AND OPERATION MANUAL
Δt and the intensity of the water flow circulating
through the boiler. The boiler will fail to reach
the desired temperature of the flow water if
the returning water temperature is too cold
or the circulation pump is too powerful. This
will happen because the boiler will be forced
to produce a larger heating output than it has
been designed for. The most effective boiler
operation occurs when the difference between
the flow and return water temperatures is 12-
14°C. If the boiler is forced to operate with a 20°C or even greater temperature difference, it will work ineffectively, consume
too much of fuel, and the combustion period of one fuel load will consequently shorten. If the previously mentioned difference
of temperatures is kept less than 10°C, the fuel in the boiler will again burn inefficiently and fume because of a lack of air
supply. If you know the water flow intensity near your boiler, in the above presented table you can check, what the difference
of flow and return temperatures your boiler is capable to maintain, when operating at the nominal heating output.
Do not forget to keep the returning water temperature as high as possible, at least 65°c or even higher!
It is necessary to assure that a thermometer is installed on the returning water pipe, in order to be able to
observe this temperature at any time!
• InsTallaTIon of THe boIleR RooM
The boiler room should be ventilated. The required air inflow necessary for combustion should be also ensured. For this
purpose, boiler room doors should have ventilation grating or there should be a sufficient gap between the doors and the
floor. If there is no possibility to supply air in from another rooms or the house is very tight, it will be necessary to install an
opening in the exterior wall. The cross-section area of the opening should be at least 0.001 m2/kW.
Place the boiler as close to the flue as possible on a hard concrete levelled basement. Leave at least 600 mm gap between the
backside casing of the boiler and the room wall for boiler servicing and cleaning. The smallest distance between a lateral casing
of the boiler and a building structure is 400 mm. If the building structure is made of flammable materials, this distance should be
doubled. A freely approachable space of at least 800 mm should be then left from the opposite side of the boiler to ensure access
to the backside of the boiler, for its servicing and cleaning. The floor under the boiler, within the distance of 50 cm in front of it and
within the distance of 30 cm around the boiler should be made of inflammable materials. Screw supporting legs onto the base of
the boiler and level the boiler with screw nuts using a level; then connect the heating system circulation pump to the boiler.
The smoke exhaust pipe of the boiler should be connected to the chimney through a metal duct. The internal diameter of
the metal connecting duct should be at least the same as the external diameter of the smoke exhaust pipe of the boiler. To
improve the draught, the connecting duct between the boiler and the chimney should be installed at an inclination towards
the boiler. All junctions should be carefully tightened using a heat-resistant material and insulated using thermal insulation.
If an additional damper is installed between the boiler and the chimney for the draught control purpose,
the damper should not close more than 2/3 of the cross-section area of the opening in its fully closed position.
• ReQUIReMenTs foR THe cHIMneY
It is recommended to insert acid-resistant stainless steel liner, if the chimney is made from masonry. It improves draught of
the chimney and protects the masonry from destruction due to the impact of condensate. Internal diameter of the liner should
Difference
of water
temperatures
Δt, °c
Heating output, kW
18
25
32
40
Water flow, l/min
11
24
33
43
53
12
22
31
39
49
13
20
28
36
45
14
19
26
33
42
15
18
24
31
39
16
16
23
29
37
17
16
22
28
34
18
15
20
26
33