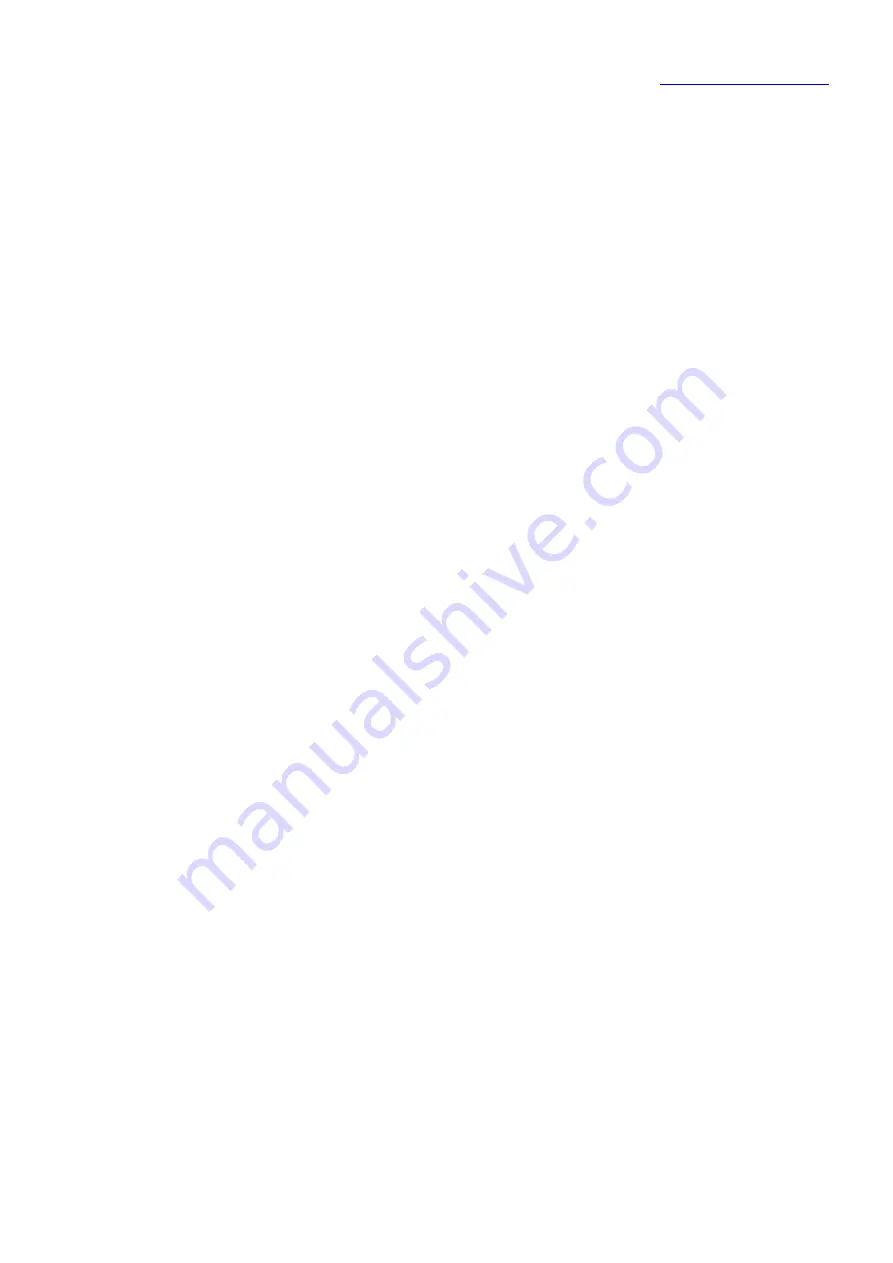
Aston Technologies Inc.
5
personal injury.
1.3.8 During tires demount/mount operation, the Clamp Wheel should always rotate
clockwise; Counterclockwise rotation indicates that machine fault or operator error. It is
operation error please do it in right way. If there is machine fault, please stop the electric
power and send the machine to repair.
1.3.9 The manufacturers will not be responsible for the damage or injury if users use parts
from other factories.
1.3.10 Regularly inspect the level of oil in Oil Drier. If the oil level is low, it needs unscrew
the cover and add oil. Professional oil for Oil Drier ISO Hg with viscosity of ISO vg32 is
recommended. (such as: Esso Fedis k32, 1405, Mobil Vacouline, KLUBER32)
1.3.12 If the product is not used for a long time, please disconnect all power supply, and
lubricate the Clamp Wheel and Center Spindle to prevent oxidation.
1.3.13 When deciding to scrap equipment, please do ensure all power supply has been cut
off. Follow native and national laws and regulations about all non-ferrous metals and
non-ferrous metal scrap.