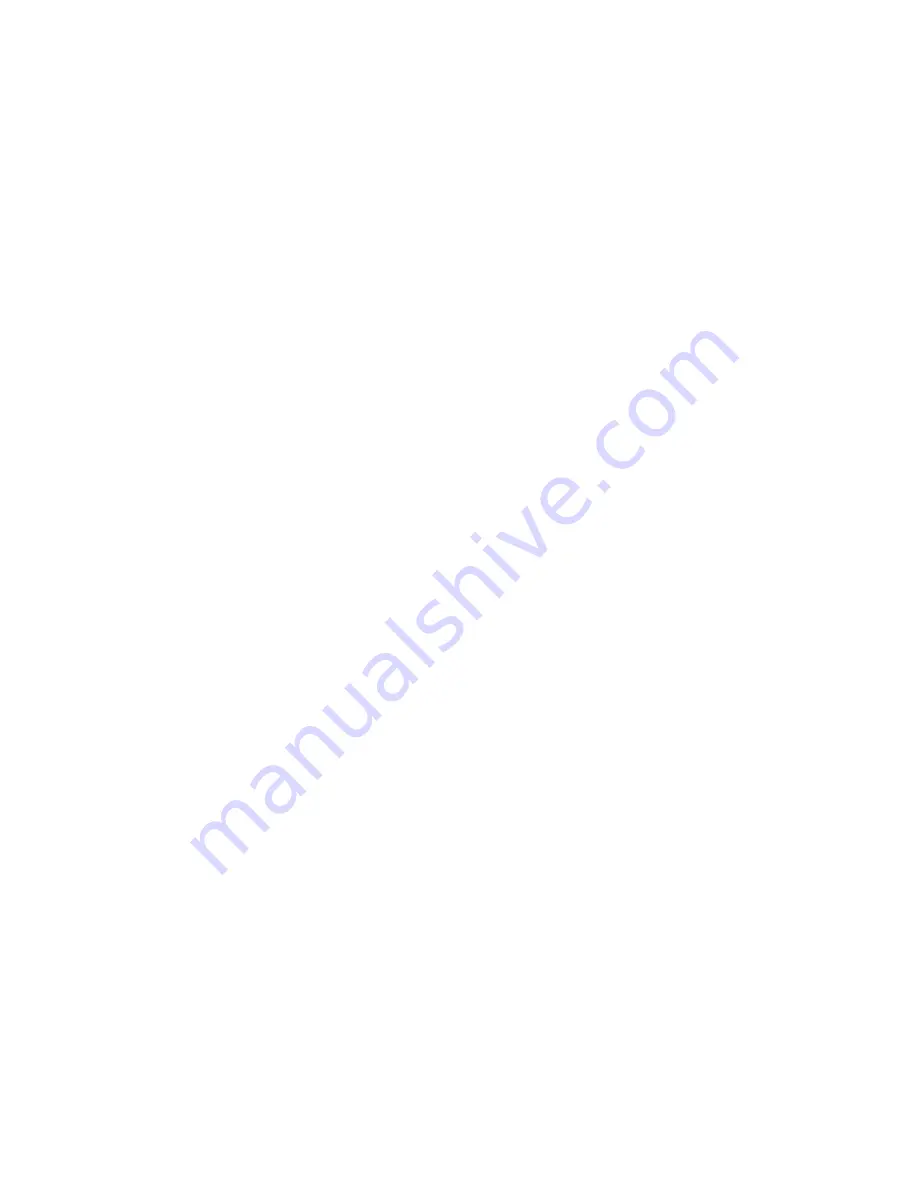
TM Page 18
4.2
RE3D CONTROLS & CONNECTIONS
Rotary Encoders:
The Display and Set rotary encoders are used to control all settings of the RE3D. The
Display encoder is used to change the information shown on the display. Various options
are available; a summary screen, large character display of strain, transmitter temperature,
transmitter supply volts etc. Pressing the Display encoder brings up the Program menu.
Each main heading can be expanded or collapsed by pressing the encoder. When the unit
is in any program menu pressing the Display encoder for 2 seconds will return to the data
Display screen.
The Set encoder is used alter any of the programmable settings and control the function of
the RE3D. Press the Set encoder to select the number to be changed, turn the encoder to
alter the amount and press again to exit setting. For example, to change the number of
teeth used by the tachometer. Press the Display encoder for enter the program menu and
turn to the Tachometer Settings option. Press again to expand the menu and select Tacho
Flags. Press the display encoder again to enter setting menu. Now turn the Set encoder to
select the digit to be changed and press Set again to change it. The digit will now be
highlighted and change altered by turning the Set encoder. When the desired number is
displayed press Set to exit the alter mode and allow the next digit to be selected. Once the
desired number of teeth has been entered press Display to return to the Program menu or
press and hold for 2 seconds to return to the data Display screen.
O/P Output(s):
This is a standard BNC socket and is the signal output. Full scale for Strain data can be set
to various output levels, for example ±5V, ±10V, 0-5V 0-10V etc. The outputs can also be
set to allow analogue logging or monitoring of the transmitter temperature and display volts.
Data Error LED:
The red DATA ERROR led will light when invalid data is received from the transmitter. This
is an excellent indication of signal integrity and system function as a micro controller is
constantly checking the received signal to ensure that uncorrupted data is present. Only
then is the DATA ERROR led extinguished. This led is always active, even when the unit is
in program mode.
12VDC Power Connector:
Power supply input connector. Nominal 12VDC at 1A. Pin 1 = +12V, Pin 2 = Ground.
Input voltage range is 9 – 36VDC allowing the RE3D to be powered from 24V automotive
supplies.
IEC Power Connector:
Mains AC Power supply input connector. 85 – 264 VAC @ 47 – 440 Hz.
Fuses:
European type TR5. Main fuse 2A Anti Surge. Inductive power fuse 1A Anti Surge. This
fuse only powers the inductive power supply in the RE3D. Removing the fuse enables the
unit to be used with the inductive head type IH1 (IH1 type is signal pickup only - no
inductive power) for maximum pickup range with a battery-powered transmitter.
Pickup Head TNC
This is connected to the inductive pickup head or loop, IH1, IH2 or IL2. For use with the IH1
the fuse MUST be removed – see above. The TNC connector is a screw version of the
BNC connector. DO NOT POWER THE UNIT WITH THE INDUCTIVE POWER ENABLED
(fuse in) AND NO HEAD CONNECTED.
4.2.1
RE3D Specifications
Bandwidth:
DC to 1000Hz.
Linearity:
±
1 bit.
Zero Stability RTO:
±
0.5 mV/
°
C
Output Noise Level:
3.5mV RMS at maximum output level setting (
±
5V output setting).
External Adjustments/Controls:
1). 10 turn locking dial- ZERO.
2). 10 turn locking dial- OUTPUT LEVEL adjust.
3) Remote Cal Pushbutton (RE2D/IFM/2 only)
Power Requirement:
12VDC @ 0.15A (No inductive power), @ 0.85A (With inductive power).
Operating Temperature:
-20 °C to +60 °C.
Summary of Contents for TX31D/1/IFM
Page 2: ...TM Page 2 ...