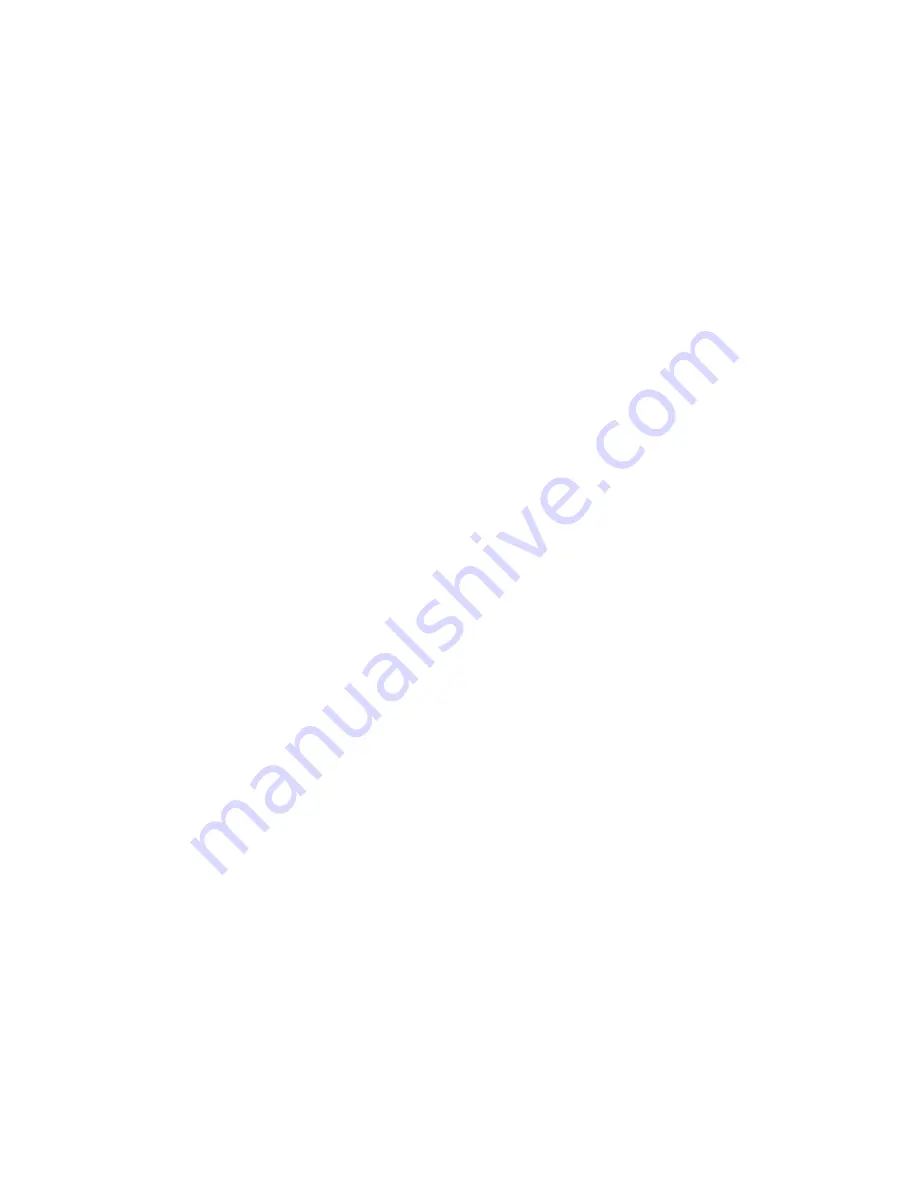
of 20
12
a 50 degree F (28 degree C) change in temperature. The
pressure will, therefore be less than indicated at high
temperatures.
4.4 Mass, Height, and Buoyancy
The density of air at room temperature and sea level
pressure is about 0.0012 grams/c.c., and the mass of the
piston assembly and weights under these conditions will
be reduced by about one part in 7,000 or .014%. When
the submerged part of the piston has a uniform cross
section, as with the 1305D Deadweight Tester, a buoyancy
correction is not necessary. In other designs, the piston is
sometimes enlarged to provide a stop for its upward mo-
tion or for increased strength. If these enlargements are
submerged in liquid, a buoyancy correction is necessary.
4.5 Absence of Friction
By rotating the weights and piston, friction effects are
greatly reduced.
4.6 Head of Transmitting Fluid
Oftentimes, the gauge being tested, or the point at which
pressure is being measured, is not at the same level as
the lower end of the piston. A correction, therefore, should
be made for the pressure distance between these points;
the height is considered positive when the gauge is above
the piston. When oil is used in the gauge tester, the cor-
rection will be approximately 0.03 psi (.2 kPa) for each
inch (2.54 cm) difference in level.
4.7 Method of Operation
It is important that the piston be kept floating in mid-posi-
tion, either spinning or oscillating.
4.8 Levelness
The piston assembly should be vertical to within ±1 de-
gree. A 3 degree tilt to piston axis may cause a .13% of
1% error. The deadweight tester is manufactured and
tested to 1/10th of 1% accuracy, to this degree of level-
ness. A tilt piston/cylinder axis causes excessive friction,
due to side loading of the piston against the cylinder.
4.9 Cleanliness
The weights have been manufactured and tested to a
precision of 0.05%. A buildup of dirt and grease may
cause the weight value to exceed its original tolerance and
produce erroneous pressure readings.
Periodically clean the weights to assure proper
performance.
5.0 MAINTENANCE INSTRUCTION
5.1 General Maintenance
The Deadweight tester and test pump are designed to
serve as precise pressure measuring standards. They are
precision built units and should be cared for in the same
manner as other sensitive laboratory equipment. General
maintenance is limited to cleaning and replacement of
O-ring packings, which can be done with tools supplied
with the equipment and requires only limited disassembly
of the gauge tester.
The piston supporting the weight platform has been man-
ufactured to very close tolerances. It has an area accuracy
of 1/20th of 1% and a weight accuracy of 1/20th of 1%.
The deadweights have been certified traceable to N.I.S.T.
with the accuracy of the finished weights better than
1/20th of 1%. To maintain deadweight tester accuracy,
handle the weights with care and keep the piston and cyl-
inder in clean condition.
The tester should be flushed with a solvent occasionally,
preferably every six months, so that operating fluid is al-
ways clean. This will prolong component life, and provide
protection against possible sticky action between the
piston and cylinder. After cleaning, always lubricate parts
before assembly.
If a deadweight tester is not used for long periods of time,
or if a piston and cylinder assembly is being replaced, the
piston should be removed from the cylinder and coated
with the hydraulic fluid, so that it never operates in a dry
state. When removing or replacing the piston, it should be
rotated back and forth.
Should a piston or cylinder wear excessively, the tester will
leak oil at a high rate, and will not be operable. A new pis-
ton and cylinder assembly should be installed.
Piston wear will result from improper or contaminated
lubrication, excessive dirt, or from several years of
continuous use.
5.2 Cleaning
Both the Tester and Test Pump should be cleaned thor-
oughly whenever the operating fluid is seriously contam-
inated with dirt, grit, or chemicals. A good practice is to
clean the test unit prior to anticipated periods when the
unit will not be in use.
5.3 To Disassemble for Cleaning
(See Figure 2-1, Figure 2-2 and Figure 5-1)
It is necessary to disassemble only those components
which come in contact with the operating fluid. Complete
disassembly is rarely necessary.
a. Remove pipe extension assembly (58) or piston and
cylinder assembly(67) and (79).
b. Then remove lower or back connection pipe assembly
(64, 66).
5.4 Removing Pump Handle and Piston
a. Remove four retaining rings (8).
b. Slide out two clevis pins (9).
c. Remove clevis (10).
d. Lift hand assembly (4) with piston pin (7) piston (20)
O-ring packing (12, 19) and back-up ring (11)
attached to it, out of piston sleeve (6).
e. Remove back-up washers (18, 11) and O-ring pack-
ing
(12, 19).
f. Unscrew piston (20)
g. Remove piston sleeve (6) and O-ring packing (45, 16)
and back-up washers (46, 17)
5.5 Removing Reservoir and Fill Tube
a. Unscrew filler plug (35) from reservoir.
b. Remove gasket (36).
c. Remove reservoir (5) by removing three screws (24).
d. Twist reservoir to free O-ring packing (21) seat.
e. Remove O-ring packing (21) from body (2).
f. Remove fill tube assembly (23) and O-ring packing (27).
g. Remove plug (22).
5.6 Removing Shuttle Valve, Shuttle Valve Plug
and Check Valve
a. Remove set screw (33) and spring (32).
b. Slide shuttle valve piston (31) out of body (2). Operate
back and forth as necessary to dislodge pin (31)
engagement.
c. Remove shuttle pin (31) by pushing it into the shuttle
valve piston cavity using a plastic shaft less than
1
⁄
8
inch (3mm) in diameter.
d. Unscrew shuttle valve plug (43) and remove O-ring
packing (27).
e. Remove check valve spring (14) and check valve (44).
f. Remove O-ring packing (15) from check valve (44).