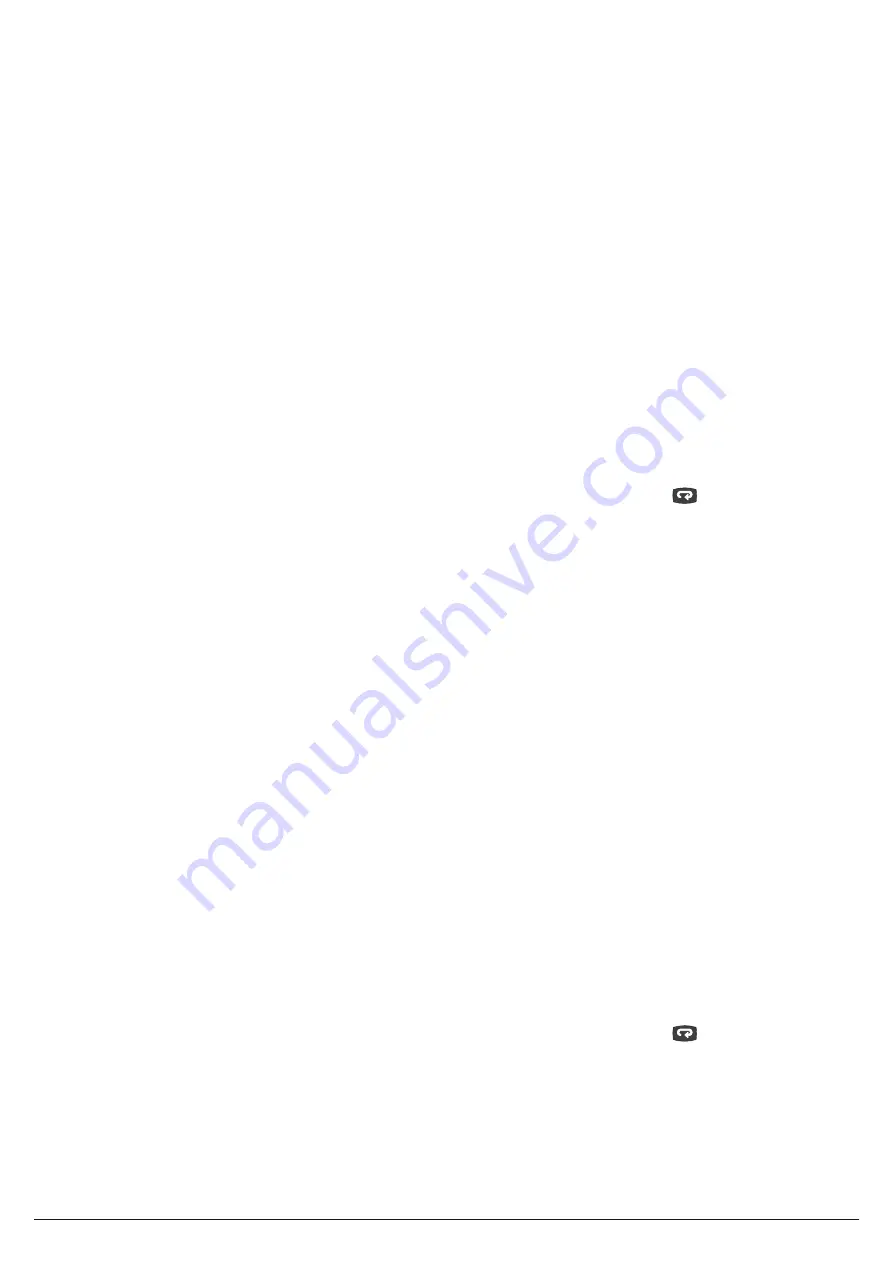
Ascon Tecnologic - KM1E/KR1E - Wine - ENGINEERING MANUAL -
PAG. 8
[4] SSc - Initial scale read-out for linear inputs
Available:
When a linear input is selected by [2] SenS.
Range:
-1999... 9999.
Notes: 1.
SSc allows the scaling of the analogue input to
set the minimum displayed/measured value.
The instrument is able to display the measured
value until it reaches a value of 5% lower than SSc,
below which shows the Underrange message.
2.
It is possible to set a initial scale read-out higher
than the full scale read-out in order to obtain a
reverse read-out scaling
e.g.:
0 mA = 0 mBar and 20 mA = -1000 mBar (vacuum).
[5] FSc - Full scale read-out for linear input
Available:
When a linear input is selected by [2] SenS.
Range:
-1999... 9999
Notes: 1.
FSc allows the scaling of the analogue input to
set the maximum displayed/measured value.
The instrument is able to display the measured
value until it reaches a value of 5% higher than
FSc, above which shows the Overrange message.
2.
It is possible to set a full scale read-out lower
than the initial scale read-out in order to obtain a
reverse read-out scaling.
e.g.:
0 mA = 0 mBar and 20 mA = -1000 mBar (vacuum).
[6] unit - Engineering unit
Available:
When a temperature sensor is selected by
[2] SenS parameter.
Range:
°c Centigrade;
°F Fahrenheit.
D
D
The instrument does not rescale the temperature
values inserted by the user (thresholds, limits etc.).
[7] FiL - Digital filter on the measured value
Available:
Always.
Range:
oFF (No filter);
0.1... 20.0 s.
Note:
This is a first order digital filter applied on the measured
value. For this reason it will affect the measured value
but also the control action and the alarms behaviour.
[8] io4.F - I/O4 function selection
Available:
Always.
Range:
on
Out4 is forced to ON (used as a transmitter
power supply);
out4
Used as digital output 4;
dG2.c Digital input 2 for contact closure;
dG2.U Digital input 2 driven by 12... 24 VDC.
Notes: 1.
Setting [8] io4.F = dG2.C or dG2V, the
[19] O4F parameter becomes not visible while
[10] diF2 parameter becomes visible.
2.
Setting [8] io4F = on the [19] O4F parameter and
the [10] diF2 parameter become NOT visible.
3.
Setting [8] io4F different than dG2.c or dG2.U, the
instrument forces [10] diF2 parameter to nonE.
If [9] diF1 was equal to (SP4 or UPDN) it will be
forced to nonE too.
4.
Changing [8] io4F = on to [8] io4F = Out4 makes
the [19] O4F parameter visible and equal to nonE.
[9] diF1 - Digital input 1 function
Available:
Always.oFF = No function;
Range:
nonE No function;
AAc
Alarm Reset [status];
ASi
Alarm acknowledge (ACK) [status];
HoLd Hold of the measured value [status];
St.bY Standby mode of the instrument [transient].
A first contact closure force the instrument
in Standby mode while a second closure
reactivate the Auto mode;
St.b2 Standby mode of the instrument [status].
When the contact is closed the instrument
operates in Standby mode. When the contact
is open the instruemnt operate in Auto mode;
HC.tr Control action and set point selection [transient].
Every contact closure revert the control
action from Heat (SP1) to Cool (Sp2) and
viceversa;
HC.St Control action and set point selection [status].
When the contact is closed the control action is
Cool with SP2 while when the contact is open
the control action is Heat and it uses SP1.
Notes: 1.
When [1] nodE = 3, HC.tr and HC.St are masked.
2.
When [1] nodE is equal to 1 or 2 and [9] diF1
is equal to HC.St, the
button manages the
Standby only.
3.
When [1] nodE is equal to 1 or 2 and [9] diF1 is
equal to HC.St, control action changes coming
from serial link are ignored.
[10] diF2 - Digital input 2 function
Available:
When [8] Io4.F = diG2.
Range:
nonE No function;
AAc
Alarm Reset [status];
ASi
Alarm acknowledge (ACK) [status];
HoLd Hold of the measured value [status];
St.bY Standby mode of the instrument [transient].
A first contact closure force the instrument
in Standby mode while a second closure
reactivate the Auto mode;
St.b2 Standby mode of the instrument [status].
When the contact is closed the instrument
operates in Standby mode. When the contact
is open the instruemnt operate in Auto mode;
HC.tr Control action and set point selection [transient].
Every contact closure revert the control
action from Heat (SP1) to Cool (Sp2) and
viceversa;
HC.St Control action and set point selection [status].
When the contact is closed the control action is
Cool with SP2 while when the contact is open
the control action is Heat and it uses SP1.
Notes: 1.
When [1] nodE = 3, HC.tr and HC.St are masked.
2.
When [1] nodE is equal to 1 or 2 and [9] diF1
is equal to HC.St, the
button manages the
Standby only.
3.
When [1] nodE is equal to 1 or 2 and [9] diF1 is
equal to HC.St, control action changes coming
from serial link are ignored.