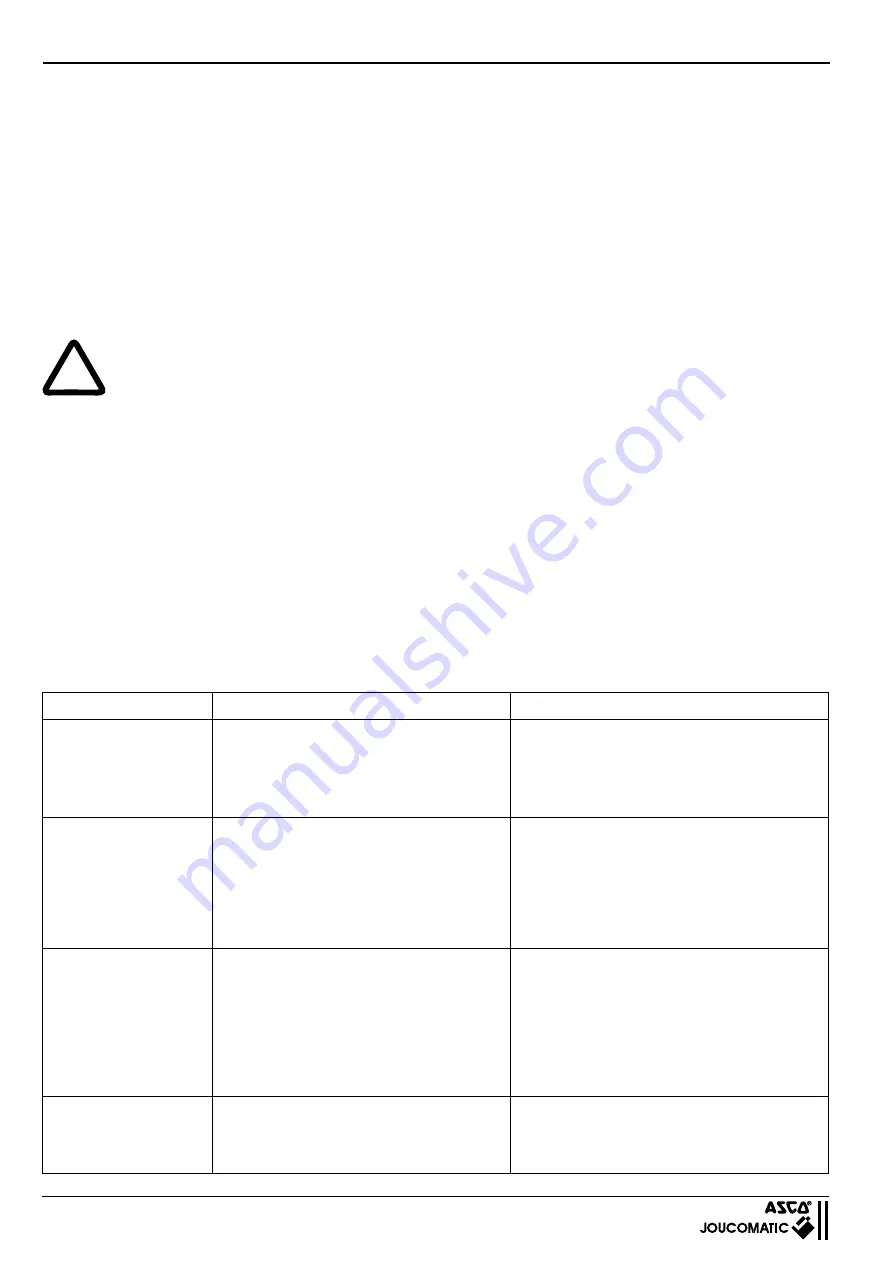
1 8
POSIMATIC
INSTALLATION
43: PROP GAIN
Proportional gain
Setting of proportional gain Kp
PROP GAIN = 10 % ... 1000 % corresponds to Kp = 0.1...10
Factory setting: PROP GAIN = 100 % corresponds to Kp = 1
44: DERIV TIME
Pre-act time
Setting of the pre-act time Tv (period of time in which a defined manipulated variable is reached more quickly than with a
P controller because of the D component).
DERIV TIME = 10 % ... 1000 % corresponds to Tv = 0.01s...1s
Factory setting: DERIV TIME = 100 % corresponds to Tv = 0.1s
Changing the factory setting of 43/44 may result in uncontrolled hunting of the valve.
45: FIELD BUS
Selection of the setpoint input
❑
Analog
❑
Fieldbus (future option)
46: RELEASE
Current software version VXX
11.
Error messages
!
PRESS
←
ERROR RUN 1
PRESS
←
ERROR RUN 2.1
PRESS
←
ERROR RUN 2.2
ADJUST NOZZLE(S)
Direction of action of the actuator cannot be
determined.
Reason:
a) No air supply
b) Wrong connection of position sensor
No zero adjustment possible.
Reason:
a) Faulty position sensor
b) Wrong position sensor (mechanical travel
does not correspond to the electrical
displacement of the position sensor).
No stroke adjustment possible.
Fieldbus:
a) Faulty position sensor
b) Wrong position sensor
c) Wrong connection of position sensor
(mechanical travel does not correspond to
the electrical displacement of the position
sensor).
Positioning time of valve under 1 second.
Connect pressure supply and check pneumatic
connections to the actuator.
Check assignment plan for correct terminal
connection (see fig. 3).
Drive valve by hand.
Display value x must change.
The display value must be > 2 % in CLOSE
position.
Drive valve by hand.
Display value x must change.
The display value must be < 98 % in OPEN
position.
Check assignment plan for correct terminal
connection (see fig 3).
Adjust flow restrictor D1 (single acting
actuator) and/or flow restrictors D1 and D2
(double acting actuators).
Turn clockwise for longer positioning time.
Display
Possible cause
Troubleshooting