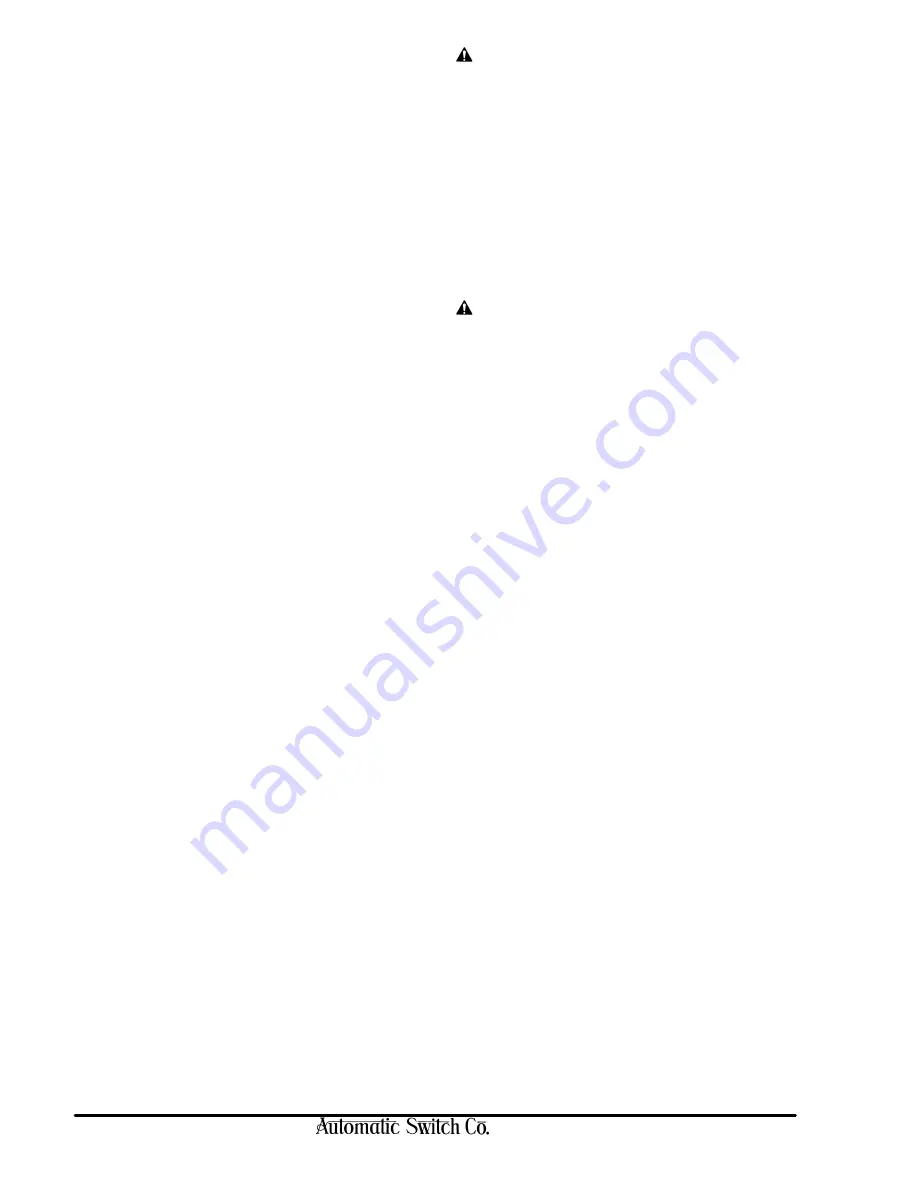
50-60 Hanover Road, Florham Park, New Jersey 07932
ASCO Valves
Page 4 of 8 (Section 1 of 2)
Form No.V6371R2-Sec.1
6. Lubricate stem/disc sub-assembly with Texaco, Inc.
Code No. 2346 Low Temp Grease EP supplied in ASCO
Rebuild Kit. Then install stem/disc sub-assembly into
valve body and through bonnet assembly.
7. Replace body gasket and body passage gaskets (2).
Body passage gaskets are only used on 2 1/2
and 3
NPT valve constructions.
8. Replace spring, valve bonnet and bonnet screws. For
valves with 3/4
NPT, torque bonnet screws in a
crisscross manner to 95 ± 10 in-lbs [10,7 ± 1,1 Nm].
For valves with 1
through 2
NPT, torque bonnet
screws in a crisscross manner to 144 ±
15 in-lbs
[16,3 ±
1,7 Nm]. For valves with 2 1/2
and 3
NPT,
torque bonnet screws to 250 ± 25 in-lbs [28,3 ± 2,8
Nm].
9. Install end cap gasket and end cap. For valves with 3/4
(8044A1 only), 2 1/2
and 3
NPT, torque end cap to
50 ± 5 ft-lbs [67,8 ± 6,8 Nm]. For valves with 3/4
through 2
NPT, torque end cap to 175 ± 25 in-lbs
[19,8 ± 2,8 Nm].
10. Install operating movement assembly over the stem
assembly and bonnet assembly. Simultaneously, install
housing nut and position indicator assembly over stem
assembly. Be sure screw and nut on position indicator
assembly are facing inwards (to the middle of the
operator housing).
11. Rotate operating movement to desired position.
Torque housing nut to 175 ± 25 in-lbs [19,8 ± 2,8 Nm].
12. To adjust position indicator, replace instruction plate on
operating movement and install two cover screws
temporarily. Adjust position indicator on stem
assembly until orange indicator line is in the center of
the
shut
window. Torque indicator screw to 25 ± 5
in-lbs [2,8 ± 0,6 Nm]. Remove cover screws and
instruction plate.
13. Install cover gasket, operator cover and cover screws on
solenoid side of operating movement. Install cover
gasket, position indicator window, instruction plate and
cover screws on lever side of operating movement.
Torque screws in a crisscross manner to 10 +5 -2 in-lbs
[1,1 ± 0,6-0,2 Nm].
14. Position solenoid bushing (if present) and solenoid base
gasket in operator housing.
15. Install core assembly into solenoid base sub-assembly.
Then install assembly into operator housing.
NOTE:
On
valves
supplied
with
an
watertight/explosionproof solenoid enclosure, position
plugnut gasket over the core assembly and down against the
lower flange. Torque solenoid base sub-assembly to
175 ± 25 in-lbs [19,8 ± 2,8 Nm].
16. Replace solenoid enclosure and make electrical hookup
to solenoid, see separate instructions.
WARNING: To prevent the possibility of
severe personal injury or property damage,
check valve for proper operation before
returning to service. Also perform internal
seat and external leakage tests (with a
nonhazardous, noncombustible fluid if
practical).
17. Check valve for external leakage as indicated under the
Piping
section, and for internal (seat) leakage as
follows.
Testing for Internal (Seat) Leakage
CAUTION: Be sure valve can be tested without
affecting other equipment.
1. Using a 3/16 hex key wrench, remove the 1/8
NPT
pipe plug from the downstream side of the valve body.
Then install suitable test piping (e.g.; two short nipples
and an elbow or tubing) to check for leakage.
2. Block flow downstream of valve.
3. Restore electrical power supply and pressurize valve to
nameplate rating.
4. With valve de-energized, immerse end of test piping
in a cup of water for 20-30 seconds and look for
bubbles, which would be indicative of seat leakage.
Repeat this procedure several times. Between each
test, remove cup of water and operate valve.
5. If seat leakage is detected, turn off electrical power and
depressurize valve. Disassemble and check for proper
placement of parts, or any foreign matter that may have
entered the valve. Clean as necessary, reassemble and
re-test valve for both external and internal leakage.
6. If no seat leakage is detected, remove test piping.
Apply a small amount of Loctite Corporation's PST
Pipe Sealant 567 (or equivalent) to the pipe plug
threads. Reinstall the pipe plug and tighten securely.
7. Test for external leakage as described in
Piping
section.
8. When maintenance is complete, operate the valve a
few times to be sure of proper operation. A metallic
click
indicates the solenoid is operating.
ORDERING INFORMATION
FOR ASCO REBUILD KITS
Parts marked with an asterisk (*) in the exploded view are
supplied in Rebuild Kits. When Ordering Rebuild Kits for
ASCO valves, order the Rebuild Kit number stamped on the
valve nameplate. If the number of the kit is not visible, order
by indicating the number of kits required, and the Catalog
Number and Serial Number of the valve(s) for which they
are intended.