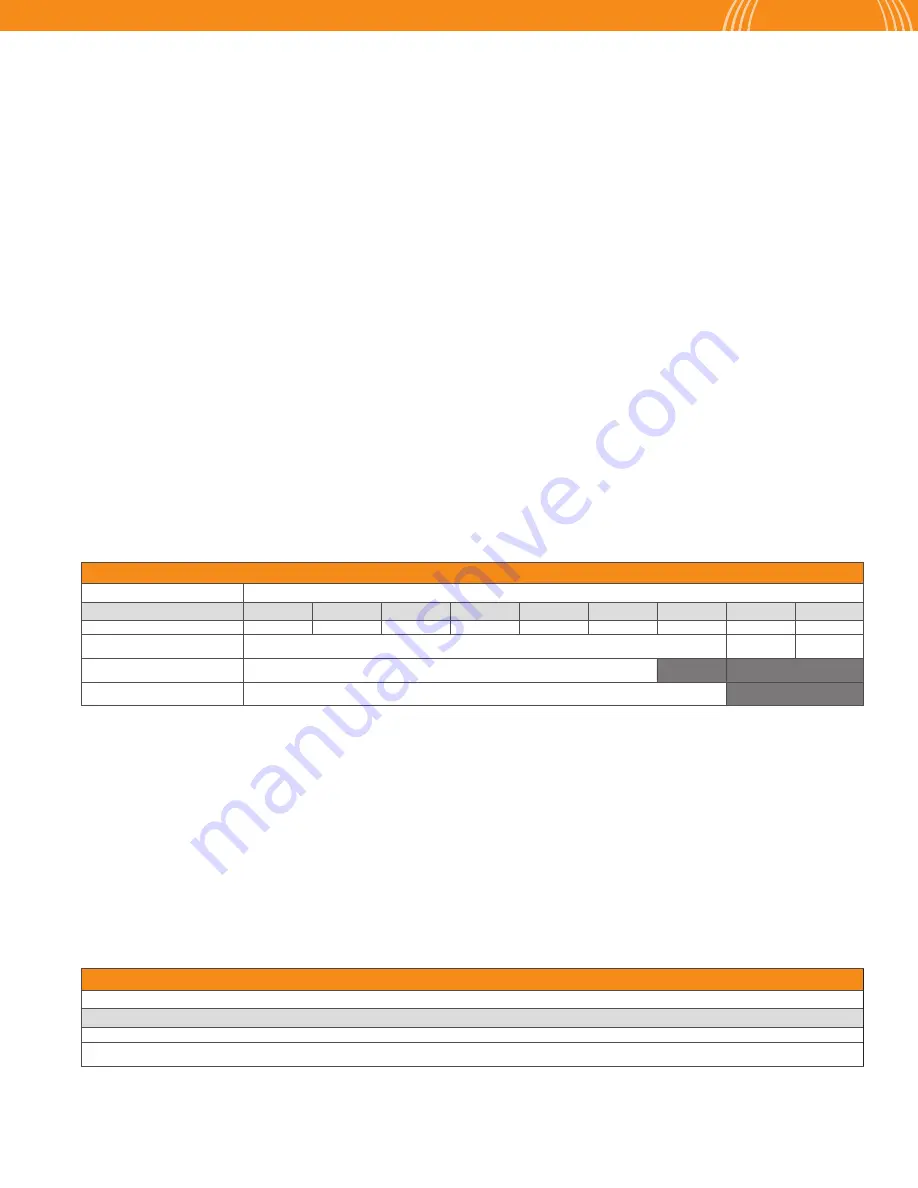
BUILDING CONNECTIONS THAT LAST
5
GROOVER DESCRIPTION
*“
RIDGID” is a registered trade mark of Emerson Electric Company.
Note: See Section XI for further details of parts for the 3006 and 3006C Roll Groover.
A. 3
006 STANDARD EQUIPMENT
Roll Groover complete with Adjustable Support Leg Assembly and
roller sets for grooving 2"-6" and 8"-12" steel pipe, Steel/CTS Dual
Guide Roll Assembly, hydraulic pump with pressure gauge, and two
depth adjustment gauges. This unit is designed for direct attachment
to your Ridgid
®
300 Power Drive. Complete with comprehensive setup,
operating and troubleshooting instructions.
Shipped in a reusable wooden storage crate.
Approximate shipping weight: 225 pounds.
Required Ridgid® 300 Power Drive not included.
B. 3006 OPTIONAL EQUIPMENT
CTS COPPER SYSTEM:
• 2"- 8" CTS Copper System Grooving Rolls, 2"- 4" CTS Depth
Gauge, and 5"- 8" CTS Depth Gauge.
A. 3
006C STANDARD EQUIPMENT
Roll Groover complete with Adjustable Support Leg Assembly and
CTS Copper System roller set for grooving 2"-6" copper tube, CTS
Guide Roll Assembly, hydraulic pump with pressure gauge, and 2"-6"
Universal Diameter Gauge. This unit is designed for direct attachment
to your Ridgid
®
300 Power Drive. Complete with comprehensive setup,
operating and troubleshooting instructions.
Shipped in a reusable wooden storage crate.
Approximate shipping weight: 215 pounds.
Required Ridgid
®
300 Power drive not included.
B. 3006C OPTIONAL EQUIPMENT
STEEL OPTION:
• Consisting of 2"-6" and 8"-12" roll sets, Steel/CTS Dual
Guide Roll Assembly, and two depth adjustment gauges
1. All wall thicknesses shown are the maximum wall thicknesses for the indicated pipe material.
2. Minimum wall thickness for each pipe material and size is:
Steel: 2"-12" Schedule 10
Stainless Steel: 2"- 12" Schedule 10S, 40S
Copper:
2"- 21/2" - Type M
3"- 8" - Type DWV
3. Please contact an Anvil Representative for information on grooving alternate materials and wall thickness.
GROOVER CAPABILITY
Pipe Material
Pipe Size/Wall Thickness (Schedule)
1,2
In.
2
2
1
⁄
2
3
4
5
6
8
10
12
DN(mm)
50
65
80
100
125
250
200
250
300
Steel
Schedule 10, 40
0.188
"
0.219
"
Stainless Steel
Schedule 10S, 40S
Copper
K, L, M & DWV
MODEL 3006/3006C STEEL PIPE GROOVING TIMES (MINUTES: SECONDS)
Pipe Size (In./DN(mm))/Max Steel Pipe Wall Thickness
2
2
1
⁄
2
3
4
5
6
8
10
12
50
65
80
100
125
150
200
250
300
0:20
0:20
0:25
0:30
1:00
1:20
1:35
1:50
2:20
C. 3006/
3006C GROOVER CAPABILITY
D. GROOVING TIMES
This chart shows approximate grooving times with the groover set-up for the proper size and groove diameter and the pipe properly positioned on the
groover. The times shown are average times from the start of rotation of the pipe in the grooving rolls to completed groove.