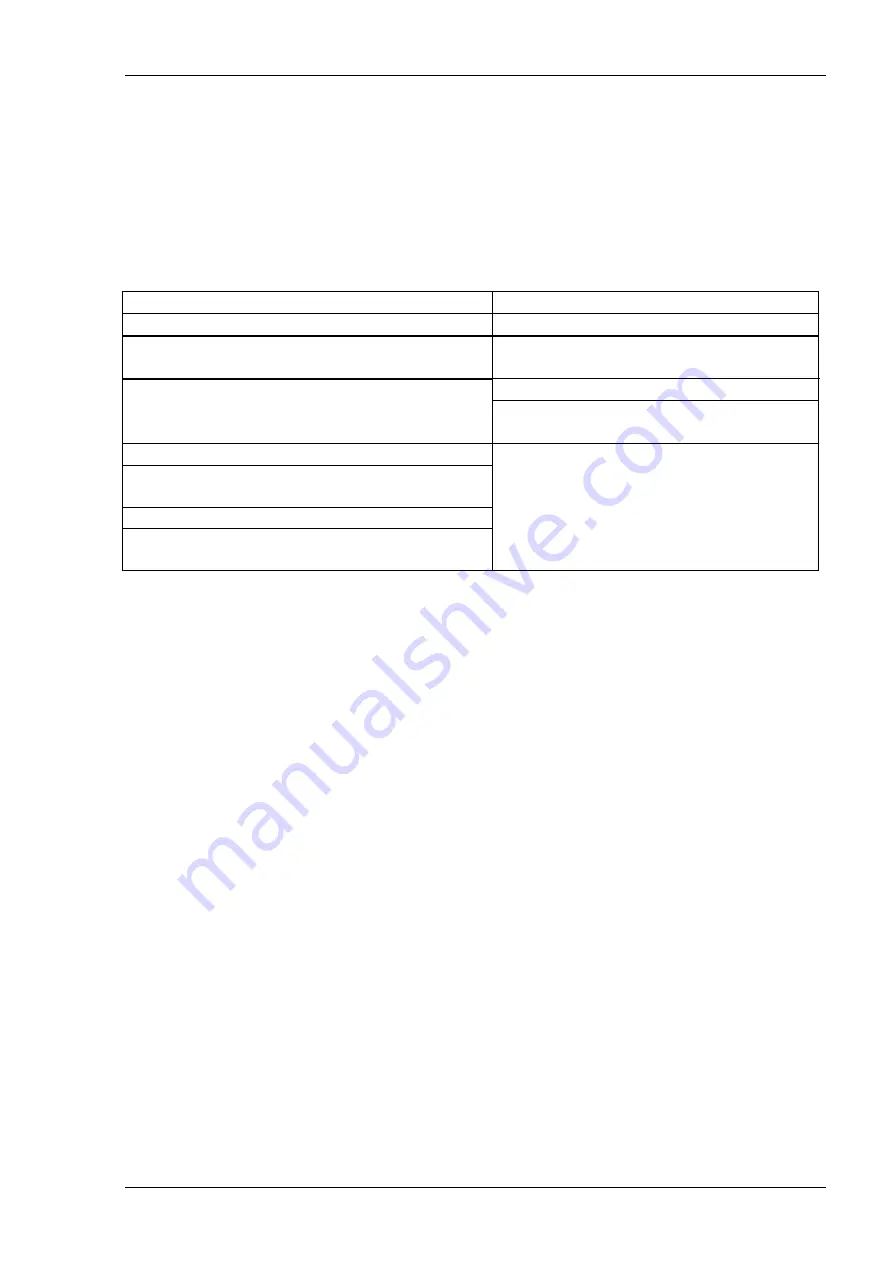
Page 21 / 49
9
AS-751 RC SAFETY SYSTEM
The AS-751 RC flail mower is remotely controlled. This means that the operator will at times
be away from the machine. In order to increase the safety for the operator and other persons, the
machine is provided with a safety system, which can be activated both manually and
automatically.
If the emergency stop is activated automatically, or if the emergency stop of the remote control
is activated, the following happens:
-
The motor stops.
-
The forward drive is put neutral.
-
The coupling of the mower remains engaged, until the motor stands
still.
When the emergency stop of the machine is activated, the power to all electric components will
be cut and cause the machine to stop.
If the mower gets out of reach of the radio signal Emergency stop is activated automatically
If the radio signal is disturbed
Emergency stop is activated automatically
Another machine is using the same radio
frequency
Emergency stop is automatically engaged
If dangerous situations occur
Activate the emergency stop at the machine
Activate the emergency stop of the remote
control
Flail mower is lifted into service position
Safety precautions will prevent the
Radio link between receiver and sender is not
established
motor from starting
Defective fuses
Emergency stop activated on remote control or
machine