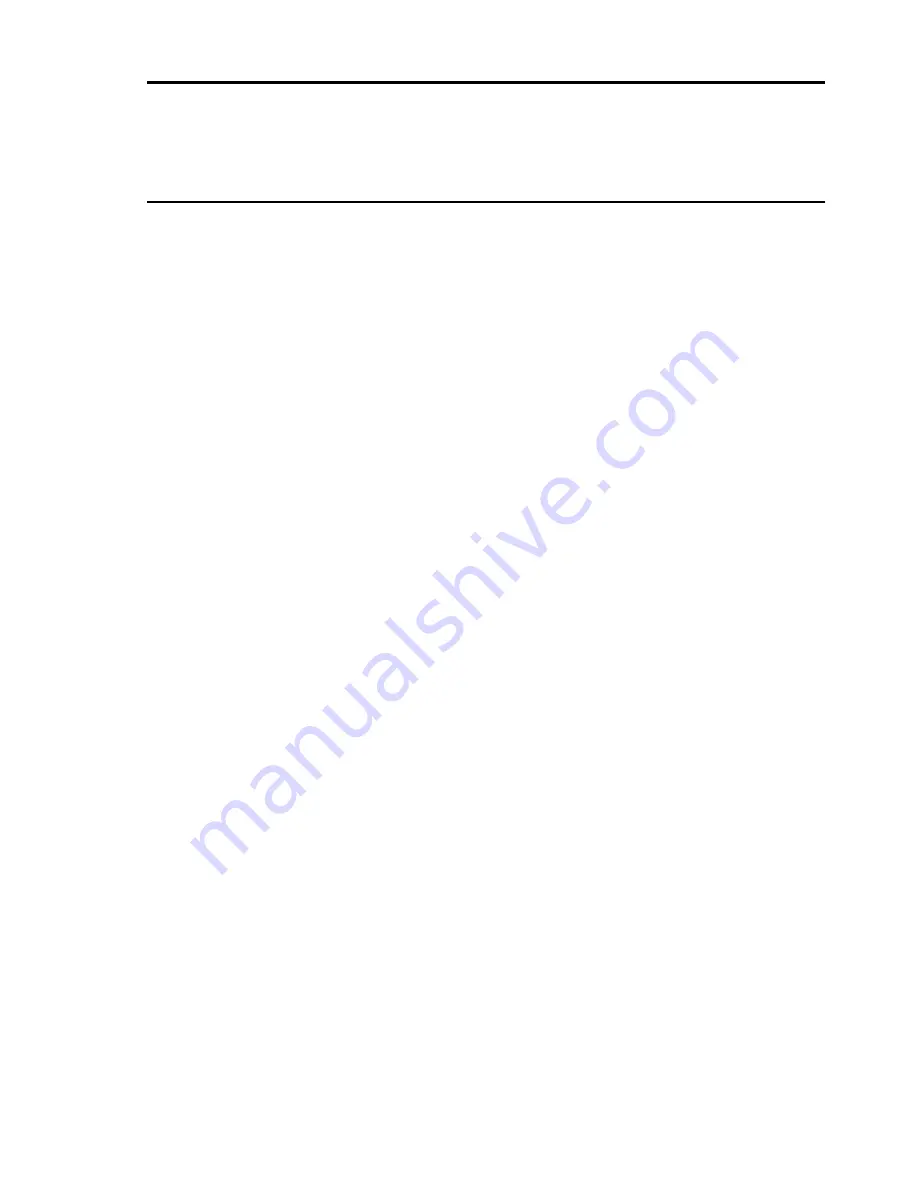
Equipment Faults, Diagnosis and Reporting
29
4.
Equipment Faults, Diagnosis and
Reporting
4.1.
Equipment Faults and their diagnoses using AMT
Toolkit
AMU uses a model based fault detection and diagnostics technique. In this technique, the
expected dynamic behavior (model) of the three-phase system is determined and
compared with the measured dynamic behavior to monitor abnormalities. AMU first learns
the system for a period of time through acquiring and processing the real-time data from
the system. The data is processed using system identification algorithms for the calculation
of expected dynamic behavior and the model parameters.
AMU analyzes the frequency spectrum of the electrical signals by extracting information
from the line current and voltage supplied to a motor. The variances in the stator-rotor air
gap are reflected back in the motor’s current through the air gap flux affecting the counter
electromotive force. Therefore, current carries information related to both mechanical and
electrical faults. Hence, faults will exhibit a change in the frequency spectrum of the current
evident in specific frequencies.
AMU uses differences between the expected current obtained from the model and the
actual current. These differences include only abnormalities generated by the motor.
Therefore, they are immune to the noise or harmonics present in the supply voltages. The
power levels of the power spectral densities (psd) of these differences are analyzed at
selected fault frequencies to determine if the equipment has existing faults. Similar to the
vibration analysis fault frequencies are in general associated with the rotational speed and
the line frequencies.
The power levels of the difference between measured and estimated current at fault
frequencies are compared with average expected values and threshold values. If they
exceed threshold values fault alarms are given at two levels; caution and high. It is
recommended that these faults maintenance but should be checked for verification and
corrective action should be taken at the next scheduled no later than six (6) months for
caution and no later than three (3) months for high alarm levels.
The fault types are selected using the distribution of faults for medium and high voltage
motors as shown below. Hence fault frequencies corresponding to these faults are also
determined.
Summary of Contents for AMT Toolkit
Page 2: ......
Page 34: ...Equipment Faults Diagnosis and Reporting 32...
Page 70: ...Appendices 68 7 6 2 Running AMU Learn...
Page 71: ...Appendices 69 7 6 3 Running AMU MONITOR IMPROVE UPDATE...
Page 72: ...Appendices 70 7 6 4 Running AMU Alarm conditions...
Page 73: ...Appendices 71...
Page 74: ...Appendices 72...