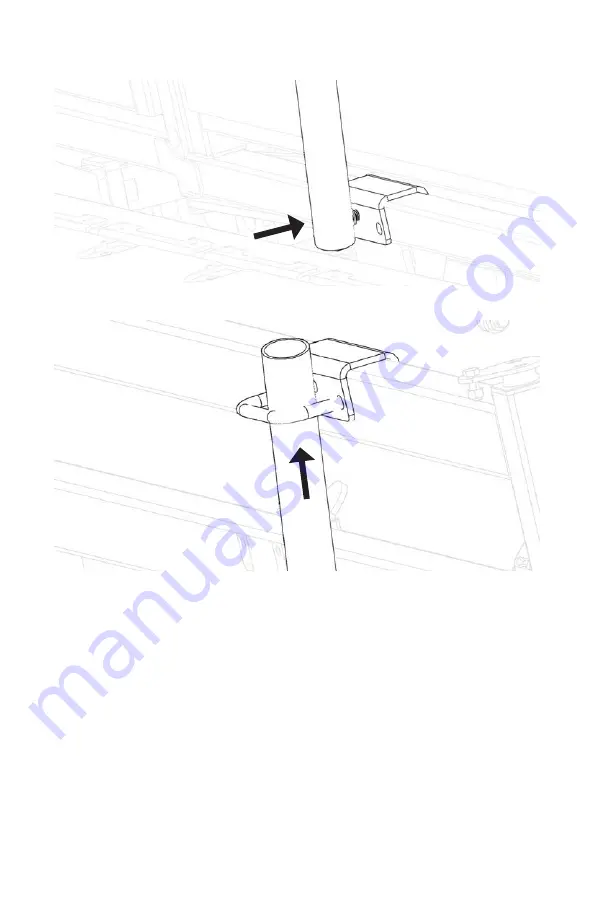
2
Attach the clipping rail to the bottom bracket.
3
Insert the clipping rail into the top bracket.
4
Adjust clipping rail position to your preference. Tighten bolts to secure.
Safety Precautions:
1. Ensure the clipping rail is installed and secured correctly before running cattle through
the crush.
31 | Q-POWER 107 SERIES ADD-ONS