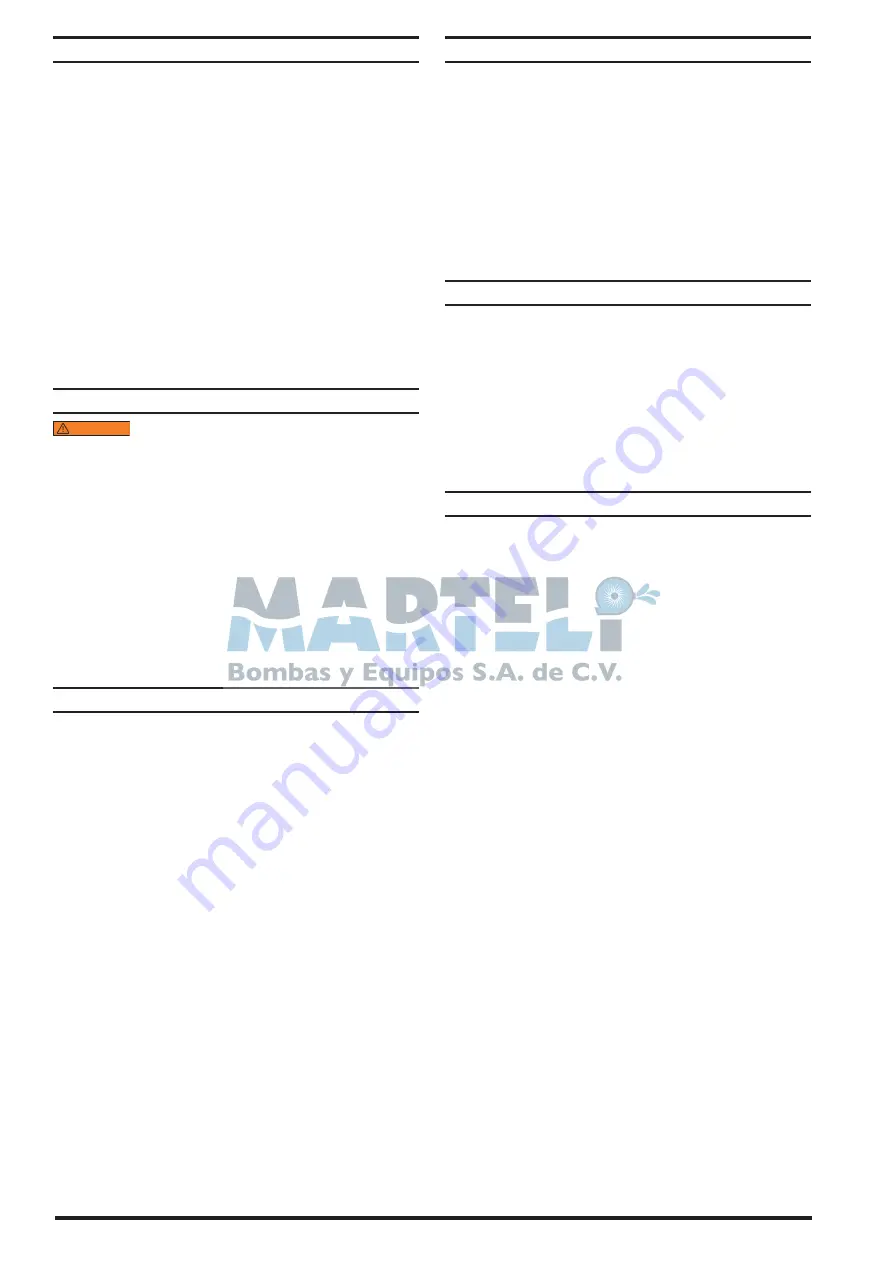
Page 4 of 12
PX01X-XXX-XXX-AXXX (en)
y
Kynar® is a registered trademark of the Arkema Inc.
y
Loctite® and 242 are registered trademarks of the Henkel Loctite Corporation
y
y
ARO® is a registered trademark of Ingersoll-Rand Company
y
Santoprene® is a registered trademark of Monsanto Company, licensed to Advanced Elastomer Systems, L.P.
y
y
Lubriplate® is a registered trademark of Lubriplate Division (Fiske Brothers Refining Company)
y
OPERATING INSTRUCTIONS
y
Always flush the pump with a solvent compatible with
the material being pumped if the material being pumped
is subject to “setting up” when not in use for a period of
time.
y
Disconnect the air supply from the pump if it is to be in-
active for a few hours.
y
The outlet material volume is governed not only by the
air supply, but also by the material supply available at
the inlet. The material supply tubing should not be too
small or restrictive. Be sure not to use hose which might
collapse.
MAINTENANCE
y
This product is not intended to be repairable. However,
some service items are available.
y
Provide a clean work surface to protect sensitive internal
moving parts from contamination from dirt and foreign
matter during service disassembly and reassembly.
y
Keep good records of service activity and include the
pump in preventive maintenance program.
y
At the end of its service life, please dispose of pump and
contents properly.
PE01X PUMP OPERATION
y
Solenoid control allows the cycle rate of the pump to be
controlled electronically.
With Solenoid control, when the solenoid is energized,
the pump strokes and dispenses the fluid in one cham-
ber. When the solenoid is de-energized, the pump
strokes in the opposite direction, dispensing the fluid in
the other chamber.
By providing continuous ON - OFF signals to the so-
lenoid, the fluid transfer rate may be increased or de-
creased remotely.
y
End of stroke feedback can be used in conjunction with
the solenoid valve to cycle the pump based upon com-
pletion of each stroke.
y
The leak detection option incorporates an optical fluid
sensor in each air chamber to provide a signal when a
diaphragm has failed and fluid is leaking through the
pump.
GENERAL DESCRIPTION
The ARO diaphragm pump offers high volume delivery even
at low air pressures, easy self priming and the ability to pump
various viscosity materials. The pump is designed to corre-
spond to the needs of the user by offering a variety of wetted
parts configurations to handle almost any application.
Air operated double diaphragm pumps utilize a pressure
differential in the air chambers to alternately create suction
and positive fluid pressure in the fluid chambers. Flat checks
insure a positive flow of fluid.
Pump cycling will begin as air pressure is applied and it will
continue to pump and keep up with the demand. It will build
and maintain line pressure and will stop cycling once maxi-
mum line pressure is reached (dispensing device closed) and
will resume pumping as needed.
The Acetal material used in this pump contains stainless steel
fibers. It’s conductivity allows it to be connected to a suitable
ground. A ground screw is provided for this.
AIR AND LUBE REQUIREMENTS
WARNING
EXCESSIVE AIR PRESSURE. Can cause pump
damage, personal injury or property damage.
y
A filter capable of filtering out particles larger than 50
microns should be used on the air supply. In most ap-
plications there is no lubrication required other than the
“O” ring lubricant which is applied during assembly or repair.
y
The pump, when fitted with flex checks, can be rotated
360° to suit the application. It may be mounted upside
down or on the wall with no effect on suction lift or op-
erating efficiency. The filter and regulator need to be ori-
ented in a normal vertical direction to function properly.
y
If lubricated air is present, make sure that it is compatible
with the “O” rings and seals in the air motor section of the
pump.
INSTALLATION
y
Apply PTFE tape or pipe sealant to threads upon assem-
bly to prevent leakage.
y
Secure the diaphragm pump legs to a suitable surface to
insure against damage by vibration.
y
When the diaphragm pump is used in a forced-feed
(flooded inlet) situation, it is recommended that a “Check
Valve” be installed at the air inlet.
RELEASED 28/Apr/2014 16:33:18 GMT
MARTELI BOMBAS Y
EQUIPOS S.A. DE C.V.
www.marteli.com.mx
Tel.(81)800-804-11 y 12